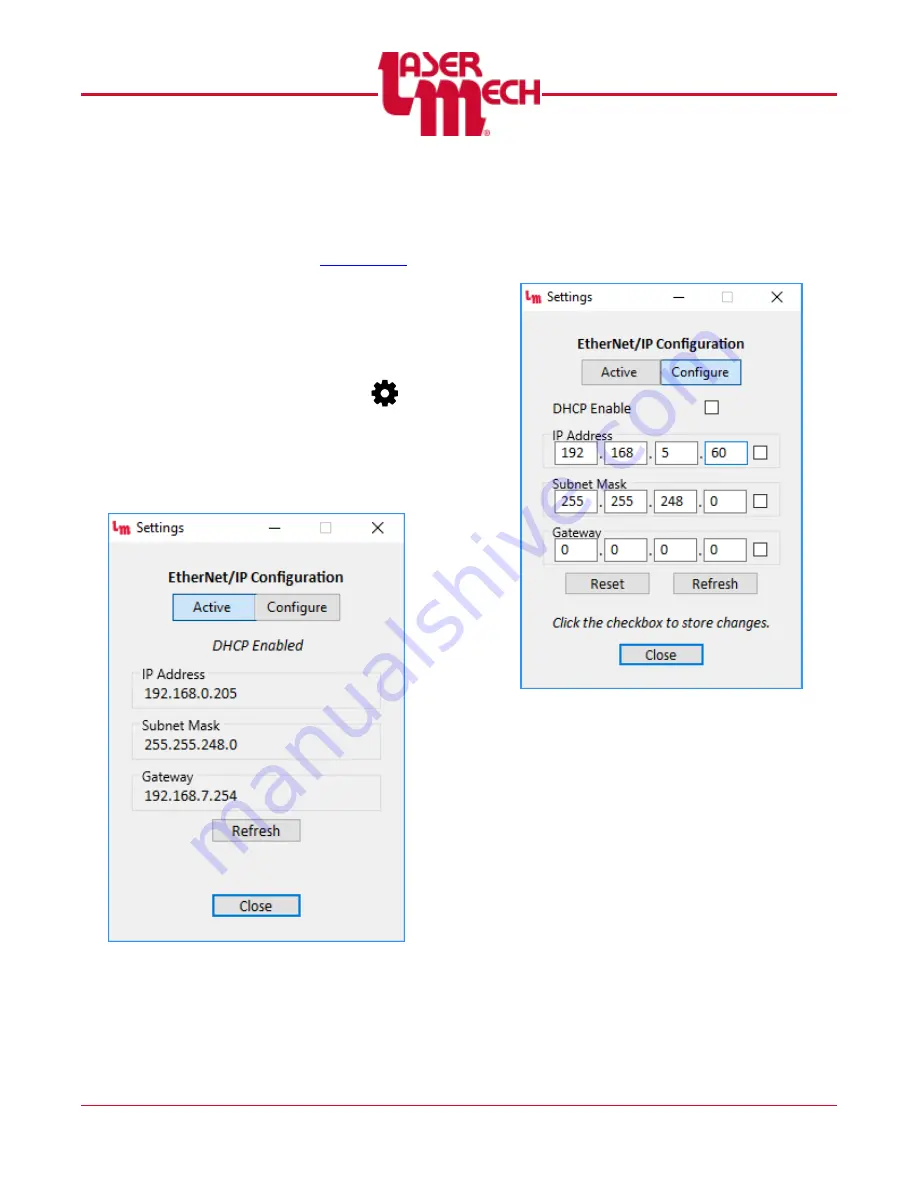
PLMNL0286 REV. B, Effective Date: 06/06/19
32
FiberMINI
®
with Auto Focus (AF) Operation Manual
4. If necessary, click
Cancel
to exit
the screen.
5. If a height sensing tip is selected,
perform steps 3 in
4.5.8 EtherNet/IP (If Equipped)
FiberMINI
®
controllers are set by
default to use DHCP for EtherNet/IP
communications. A static IP address
can be set using FiberMINI
®
Monitor.
1. Click the
Settings
button (
) in
the toolbar and select
Industrial
Network
.
The EtherNet/IP Configuration screen
appears showing the active network
settings. See
Figure 37
2. To modify the configuration, click
on the
Configure
tab and update
the
DHCP, IP Address, Subnet
Mask
, and
Gateway
settings as
Figure 38
3. If desired, click the check box next
to each set of values to save the
changes to the network module.
To cancel changes that have
not yet been saved, click
Refresh.
Содержание FiberMINI 2.0
Страница 1: ...FiberMINI 2 0 With Auto Focus AF Operation Manual ...
Страница 23: ...PLMNL0286 REV B Effective Date 06 06 19 18 FiberMINI with Auto Focus AF Operation Manual Figure 17 ...
Страница 52: ...PLMNL0286 REV B Effective Date 06 06 19 47 FiberMINI with Auto Focus AF Operation Manual Figure 55 ...