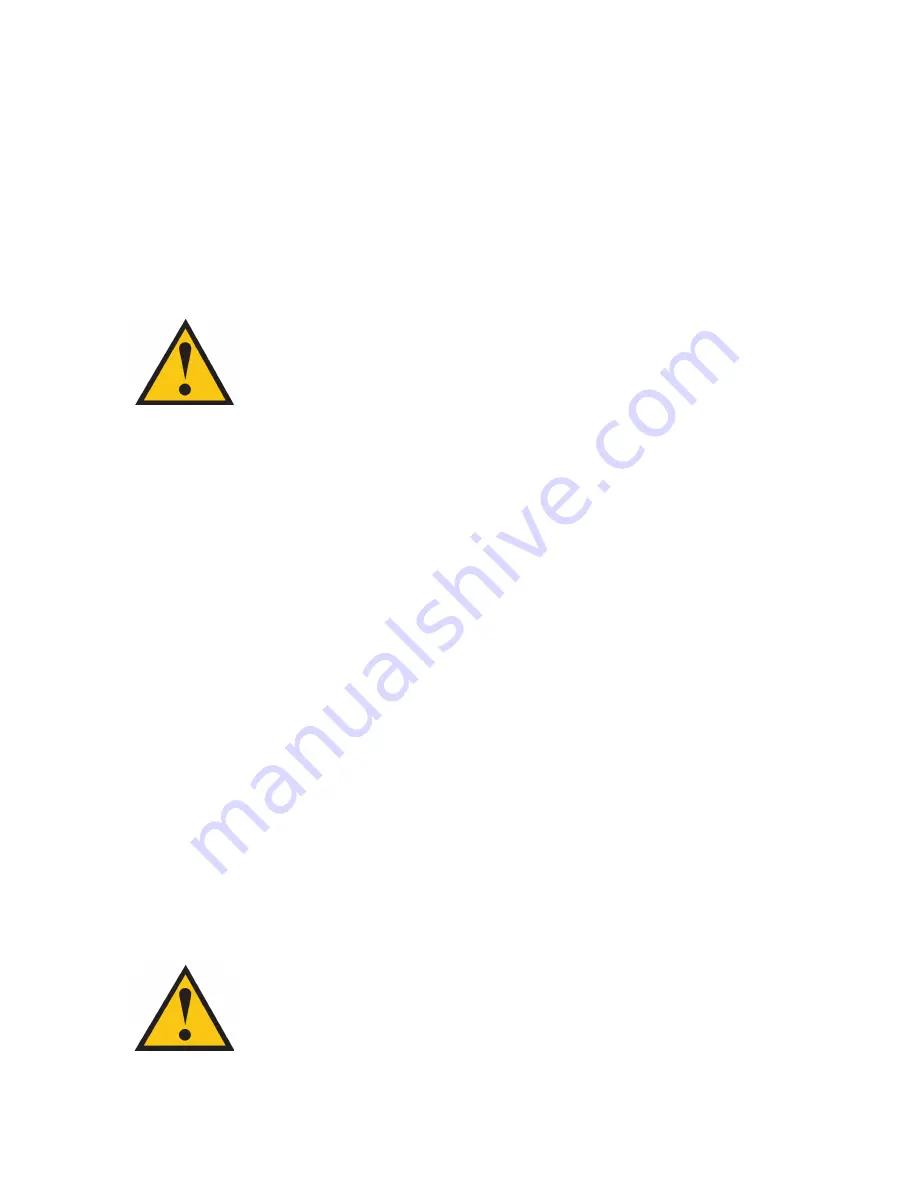
13
P.N. 28-0580/02
1.5 CONNECTING TO WATER SUPPLY LINES
A. Use a filter in the water line to avoid equipment damage and beverage off-taste.
Check the water filter periodically, as required by local conditions.
B. Protect the water supply by means of an air gap, a backflow prevention device,
or another approved method that complies with NSF standards. A leaking inlet
water check valve will allow carbonated water to flow back through the pump
when it is shut off and will contaminate the water supply. Ensure the backflow
prevention device complies with ASSE and local standards.
It is the
responsibility of the installer to ensure compliance.
C. Provide an adequate potable water supply. Water pipe connections and fixtures
directly connected to a potable water supply must be sized, installed, and
maintained according to federal, state, and local laws.
D. For the plain water supply line, the inlet water flowing pressure should be at
least 75 PSI. If the water pressure is lower than 75 PSI flowing, use a water
booster system.
If the water flowing pressure is lower than 75 PSI at the plain water inlet and a
water booster is not installed, water products will not hold a proper flow rate or
water/syrup ratio. Flow conditions at the nozzle can also be affected, causing
poor nozzle coning and mixing.
NOTE:
The Lancer Water Booster/Tank (PN MC-163172) is offered as a kit. The
water booster must be installed as close as possible to the plain water circuit
inlet.
E. For the soda water supply line, do not exceed 50 PSI for the inlet water static
pressure going into the carbonator pump. If the static water pressure exceeds
50 PSI, install a water regulator before the carbonator water inlet.
NOTE:
Install the water regulator (Lancer PN 18-0306) included with unit as
close as possible to the water carbonator pump inlet. The recommended water
pressure value feeding the carbonator is a minimum of 25 PSI. If the normal
water pressure does not exceed 50 PSI, but fluctuates over this value (for
example, when water usage on other equipment connected to the same water
supply causes pressure spikes), use a water regulator.
WARNING!
Do not connect to a hot water or soft water source. This causes
excessive foaming.
WARNING!
Do not operate the carbonator pump with the water supply off.
Doing so can damage components and void the warranty.
Содержание FLAVOR SELECT 22
Страница 11: ...11 P N 28 0580 02 1 3 FS22 INSTALLATION OVERVIEW 1...
Страница 12: ...12 P N 28 0580 02 1 4 FS22 INSTALLATION OVERVIEW 2...
Страница 39: ...39 P N 28 0580 02 NOTES...