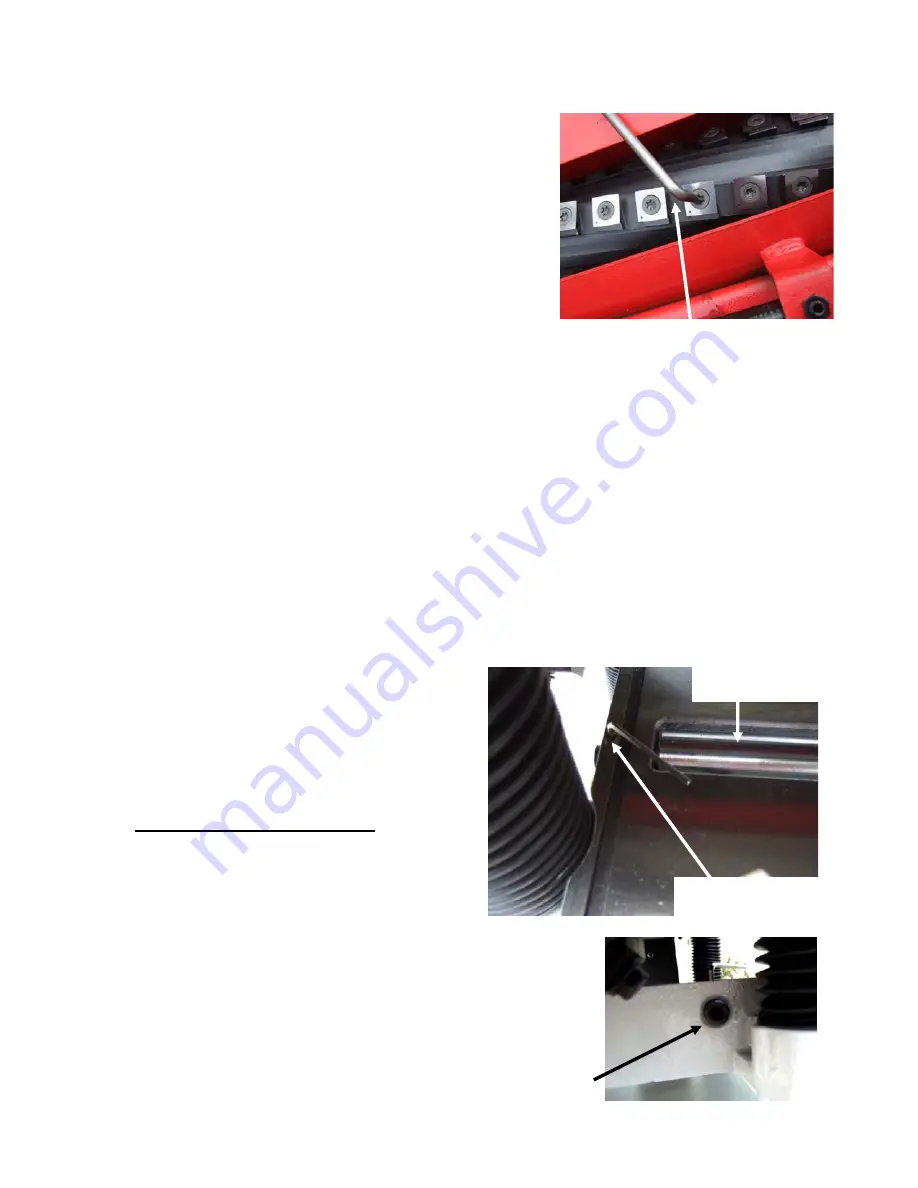
1.
With the power disconnected from the
machine, Remove the cutter head guard and
the dust chute.
2
Loosen the tooth with the special allen key
2.
Lift the tooth and rotate to the new cutting
face.
Special allen key
Note.
Take special care to clean the tooth and
its mating surface. Any dirt or sawdust that is
trapped under the tooth will cause it to be at a
different height to the other teeth and degrade the surface
finish when you start machining. This will result in you
having to take all the teeth out and clean the teeth and the mating surfaces
again. This is very frustrating and a waste of time, take your time and ensure
that you are very thorough with cleaning.
3.
Lower the tooth into the cutter head and clamp with the allen key.
Note.
Only move all the teeth to a new cutting edge. Do not move less than all
the teeth.
Note.
The carbide cutter head has several advantages over the parallel blade
type cutter head.
1.
The teeth are carbide and will last longer than high speed steel parallel
blades.
2
. There is less chance of tear out.
The disadvantage is that they are
initially more expensive and that the
surface finish is slightly wavy. This is
caused because the teeth have a very
slight radius. This waviness is easily
removed by a light sanding.
Table roller
Clamp screw
Adjusting the table rollers.
The table rollers come factory set.
Adjustment is provided should it be
needed.
1.
Checking the height of the rollers is achieved by
placing a straight edge across both rollers and
checking the distance between the rollers and the
table with feeler gauges. The rollers should be 0.002
Side adjustment screw
23