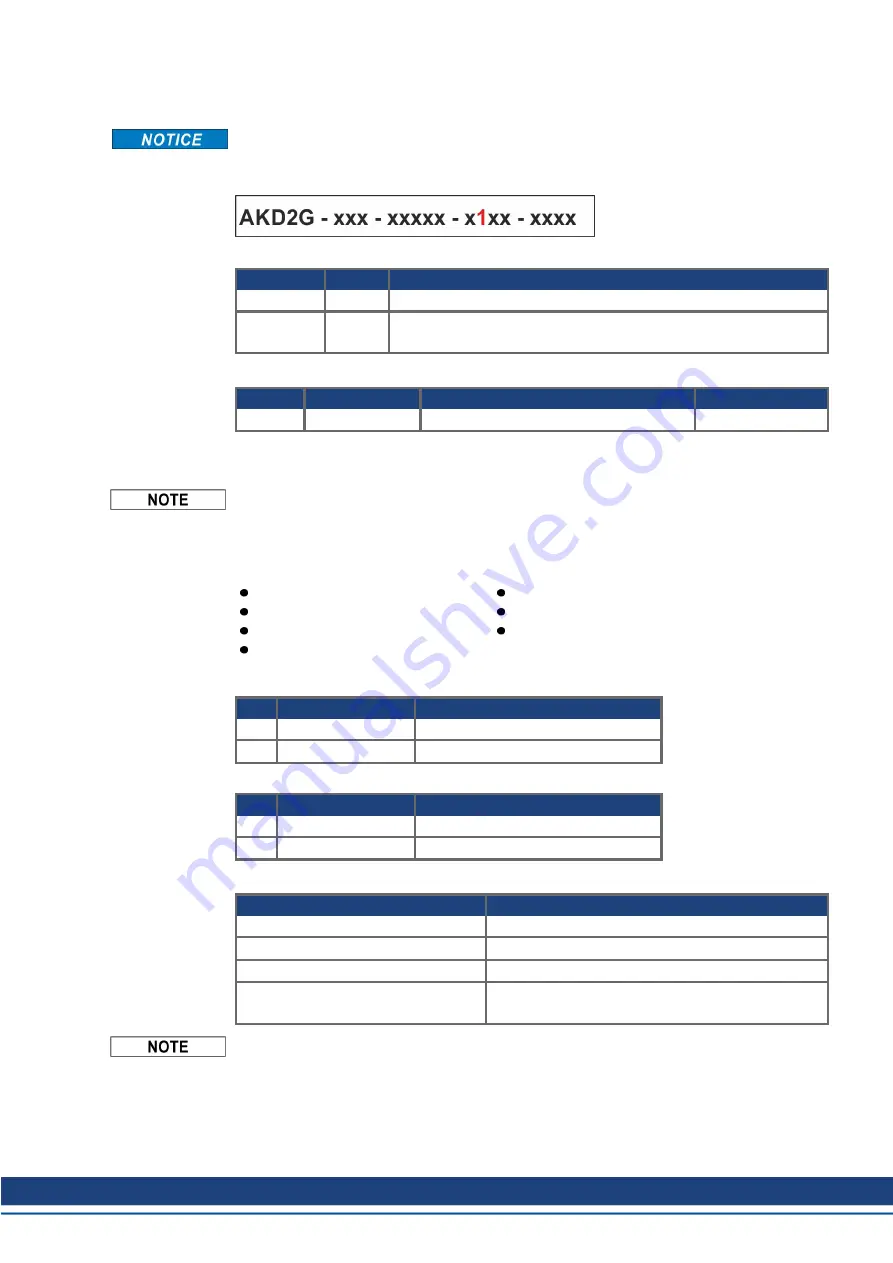
10.6 Functional Safety Option 1 (I/O, SIL2 PLd)
Beta Drives: STO function of AKD2G is neither approved nor certified. Do not use this func-
tionality in applications with functional safety request.
Valid for AKD2G devices with Functional Safety Option 1:
Standards
Standard
Edition Content
ISO 13849
2015
Safety of machinery: Safety-related parts of control systems
IEC 62061
2015
Functional safety of electrical/electronic/programmable electronic
safety-related systems
Available Safety Functions
Abbr.
Function
Activation
Refer to
STO
Safe Torque Off Safe digital inputs for one or for both axis
10.6.1 Technical Data
Safe inputs are fixed to the STO function.
When STO function (Safe Torque Off) is not needed, then all STO inputs must be connected
directly with +24 V. The STO function is then bypassed and cannot be used.
I/O data
Reference ground is DGND
Galvanic isolation for 60 VDC
Activation delay about 5 µs
De-activation delay about 500 µs
Use 24 VDC ±15% PELV power supply
High level 17 VDC to 30 VDC, 5 mA to 6 mA
Low level 0 VDC to 5 VDC, max.1 mA
Pinout
X21 Signal
Description
A11 STO-A-A1
STO channel A (for axis 1)
B11 STO-B-A1
STO channel B (for axis 1)
Drives with two axes, or option IO or DX:
X22 Signal
Description
A12 STO-A-A2
STO channel A (for axis 2)
B12 STO-B-A2
STO channel B (for axis 2)
Keywords
Keyword
Description
AXIS#.SAFE.STO.A
Reads the status of STO input channel A for axis #.
AXIS#.SAFE.STO.B
Reads the STO input channel B for axis #.
AXIS#.SAFE.STO.ACTIVE
Reads the STO status of axis#.
AXIS#.SAFE.STO.REPORTFAULT F9000 and W9000 are triggered for axis # only, if set
to 1 (default).
For full keyword description refer to the
Functional Safety Parameter Reference Guide
Factory Default Settings
AXIS#.SAFE.STO.REPORTFAULT is set to 1.
AKD2G-S Installation, Safety 1 | 10 Functional Safety
Kollmorgen | kdn.kollmorgen.com | S101, December 2018
127