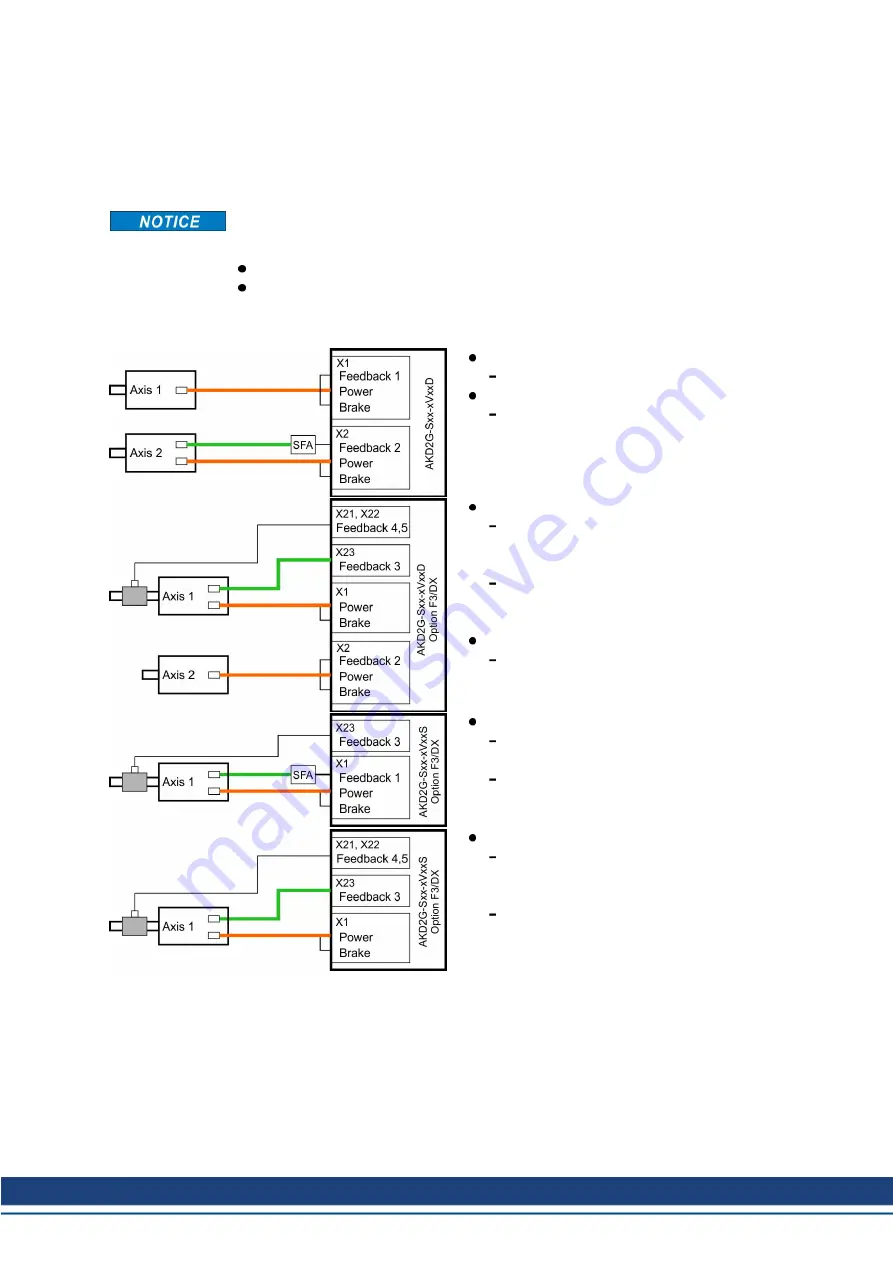
8.9 Motor Power, Brake and Feedback connection
The AKD2G drive is able to protect the connected motor from overloading, if the parameters
are set correctly and the thermal protection sensor is connected and supervised. With Koll-
morgen motors the valid data are automatically set by the internal WorkBench motor data-
base.
The dynamic voltage rise can lead to a reduction in the motor operating life and, on unsuit-
able motors, to flashovers in the motor winding.
Only install motors with insulation class F (acc. to IEC60085) or above.
Only install cables that meet the requirements (
8.9.1 Motor connectivity, some examples
Axis 1: single cable connection (
commutation feedback: SFD3 or DSL
Axis 2: dual cable connection (
commutation feedback: EnDAT, HIPERFACE,
Resolver etc. via SFA
Axis 1: dual cable connection (
commutation feedback: Resolver, SFD, EnDAT,
HIPERFACE, BiSS, SinCos, ComCoder, Hall,
SmartAbs etc. via X23
position feedback:
- X21: Step/Direction
- X22: Step/Direction or incremental encoder
Axis 2: single cable connection (
commutation feedback: SFD3 or DSL
Axis 1: dual cable connection (
commutation feedback: EnDAT, HIPERFACE,
Resolver etc. via SFA
position feedback:Resolver, SFD, EnDAT,
HIPERFACE, BiSS, SinCos, ComCoder, Hall,
SmartAbs etc. via X23
Axis 1: dual cable connection (
commutation feedback: Resolver, SFD, EnDAT,
HIPERFACE, BiSS, SinCos, ComCoder, Hall,
SmartAbs etc. via X23
position feedback:
- X21: Step/Direction
- X22: Step/Direction or incremental encoder
AKD2G-S Installation, Safety 1 | 8 Electrical Installation
Kollmorgen | kdn.kollmorgen.com | Beta, December 2018
77