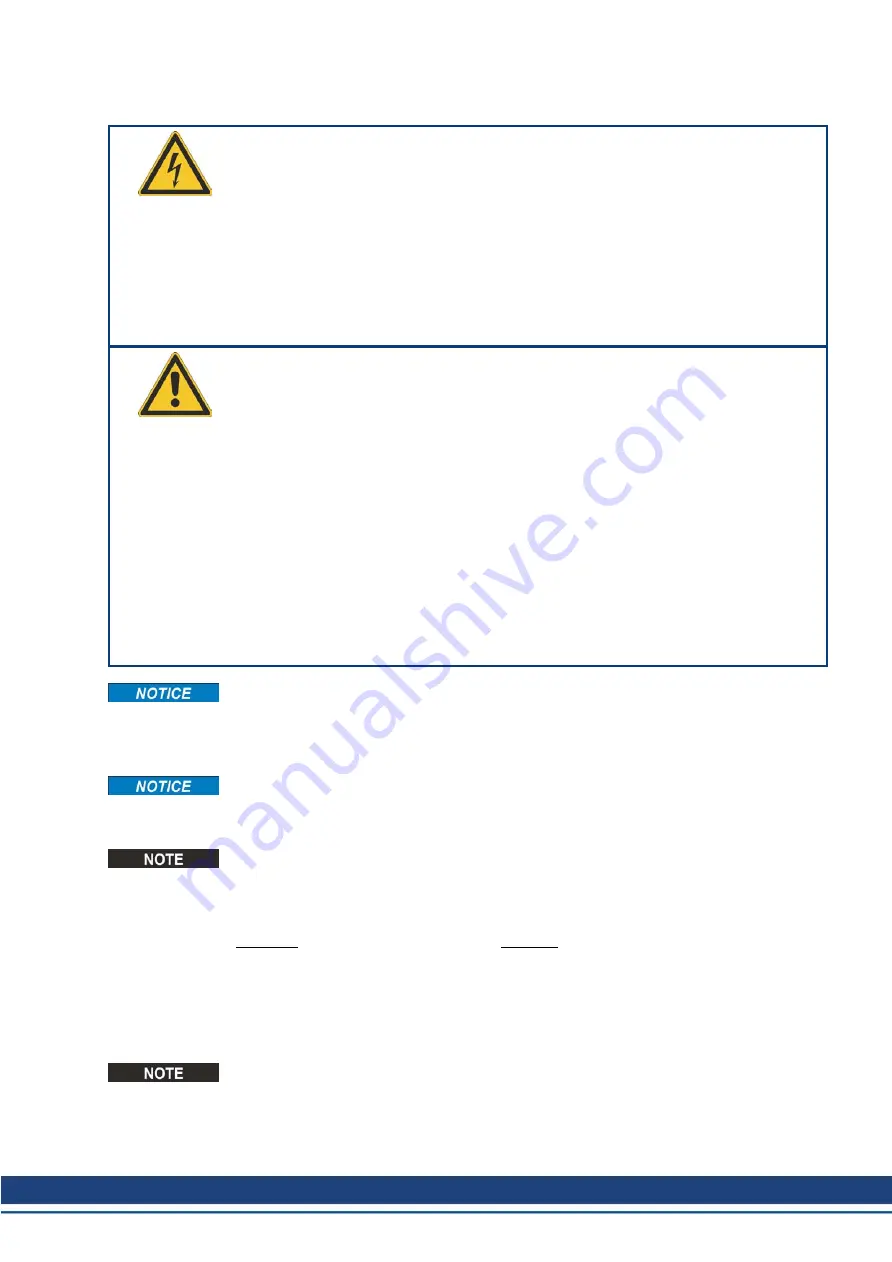
4.1 Important Instructions
DANGER
Never undo any electrical connections to the drive while it is live. There is
a danger of electrical arcing with damage to contacts and serious per-
sonal injury.
Wait at least seven minutes after disconnecting the drive from the main
supply power before touching potentially live sections of the equipment
(e.g. contacts) or undoing any connections.
To be sure, measure the voltage in the DC Bus link and wait until it has
fallen below 60 V.
WARNING
Electronic equipment is basically not failure-proof. The user is respons-
ible for ensuring that, in the event of a failure of the drive, the drive is set
to a state that is safe for both machinery and personnel, for instance with
the aid of a mechanical brake.
Drives with PROFINET are remote-controlled machines. They can start to
move at any time without previous warning. Take appropriate measures
to ensure that the operating and service personnel is aware of this
danger.
Implement appropriate protective measures to ensure that any unin-
tended start-up of the machines cannot result in dangerous situations for
personnel or machinery. Software limit-switches are not a substitute for
the hardware limit-switches in the machine.
Install the drive as described in the
Installation Manual
. The wiring for the analog setpoint
input and the positioning interface, as shown in the wiring diagram in the
Installation Manual
,
is not required. Never break any of the electrical connections to the drive while it is live. This
action can result in destruction of the electronics.
The drive's status must be monitored by the PLC to acknowledge critical situations. Wire the
FAULT contact in series into the emergency stop circuit of the installation. The emergency
stop circuit must operate the supply contactor.
It is permissible to use the setup software to alter the settings of the drive. Any other alter-
ations will invalidate the warranty. Because of the internal representation of the position-con-
trol parameters, the position controller can only be operated if the final limit speed of the drive
does not exceed:
rotary
linear
at sinusoidal² commutation:
7500 rpm
at sinusoidal² commutation: 4 m/s
at trapezoidal commutation:
12000 rpm.
at trapezoidal commutation: 6.25
m/s
All the data on resolution, step size, positioning accuracy etc. refer to calculatory values.
Non-linearities in the mechanism (backlash, flexing, etc.) are not taken into account. If the
final limit speed of the motor must be altered, then all the parameters that were previously
entered for position control and motion blocks must be adapted.
AKD PROFINET | 4 Installation and Setup
Kollmorgen | December 2014
13
Содержание AKD PROFINET RT Communication
Страница 8: ...AKD PROFINET 2 General 8 Kollmorgen December 2014...
Страница 30: ...AKD PROFINET 6 PROFIDRIVE over PROFINET IO 6 3 General State Machine 30 Kollmorgen December 2014...
Страница 46: ...AKD PROFINET 7 Sample Projects 7 Sample Projects 7 1 Sample S7 Project 47 46 Kollmorgen December 2014...
Страница 52: ...This page intentionally left blank AKD PROFINET 9 Index 52 Kollmorgen December 2014...