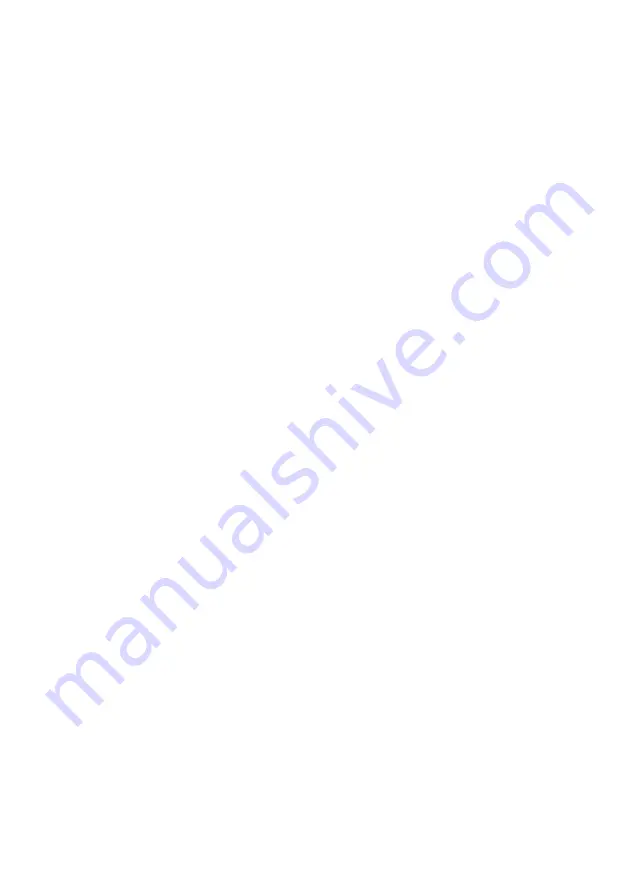
10
1057614-W2-D
Installation
- solid wall recess
The Rada Exact-3 B is suitable for building-in to solid, dry-lined, stud partition or dry
partition wall structures.
To allow for connection of pipework, the recess in the wall (unfinished) should be
approximately the same shape as the building-in shroud. Place the building-in shroud
in the correct position on the wall and draw around it with a pencil.
The depth of concealment is critical, the minimum depth to accept the valve is
50 mm, with another 15 mm maximum on top of this for finishing coat thickness of
plaster and tiles or other material. This last dimension determines how much of the
temperature or flow knobs will be visible through the concealing plate.
Important!
Predetermine the finishing thickness (e.g. tiles, plaster etc.) on top of
the wall surface. If this is to be less than 10 mm then the pre-assembled mounting
bracket must be reversed (refer to Figure 2).
The building-in shroud protects the mixing valve during plastering/finishing and
provides a reference for the building-in depth.
1.
Cut out the wall to the required dimensions.
2.
This mixing valve is supplied with outlet to top, should the installation require
outlet to bottom, then refer to Outlet Position/Reversed Inlets.
3.
Put the valve in the recess and connect inlet and outlet pipework, checking
that the hot and cold supplies have been piped to the correct inlets. Check all
connections are watertight.
4. Important!
Flush through the hot and cold supplies thoroughly before connection
to mixing valve.
5.
Mount the valve in the recess using appropriate wall screws/plugs.
Note!
If the wall screws are unable to be fixed into the wall, fit the building-
in shroud and fill the cavity behind the mounting bracket with an appropriate
material (e.g. expandable foam).
6.
Fit the building-in shroud over mixing valve in recess. Plaster and tile, or finish
as appropriate, up to edge of shroud.
Final wall surface must fall between 2
lines on building-in shroud.
7.
When wall surface is finished, remove the building-in shroud.
11.
Refit the body shrouds and backplates, making sure that the foam seal is tight
around both body shrouds. Refit the concealing plate and knob assemblies so
that the markings will be visible to the user.
12.
The maximum temperature may now need resetting; check, and if necessary
refer to
COMMISSIONING
.
Содержание rada Exact-3 B
Страница 1: ...1 1057614 W2 D These instructions must be left with the user Product Manual Exact 3 B ...
Страница 26: ...26 1057614 W2 D NOTES ...
Страница 27: ...27 1057614 W2 D ...