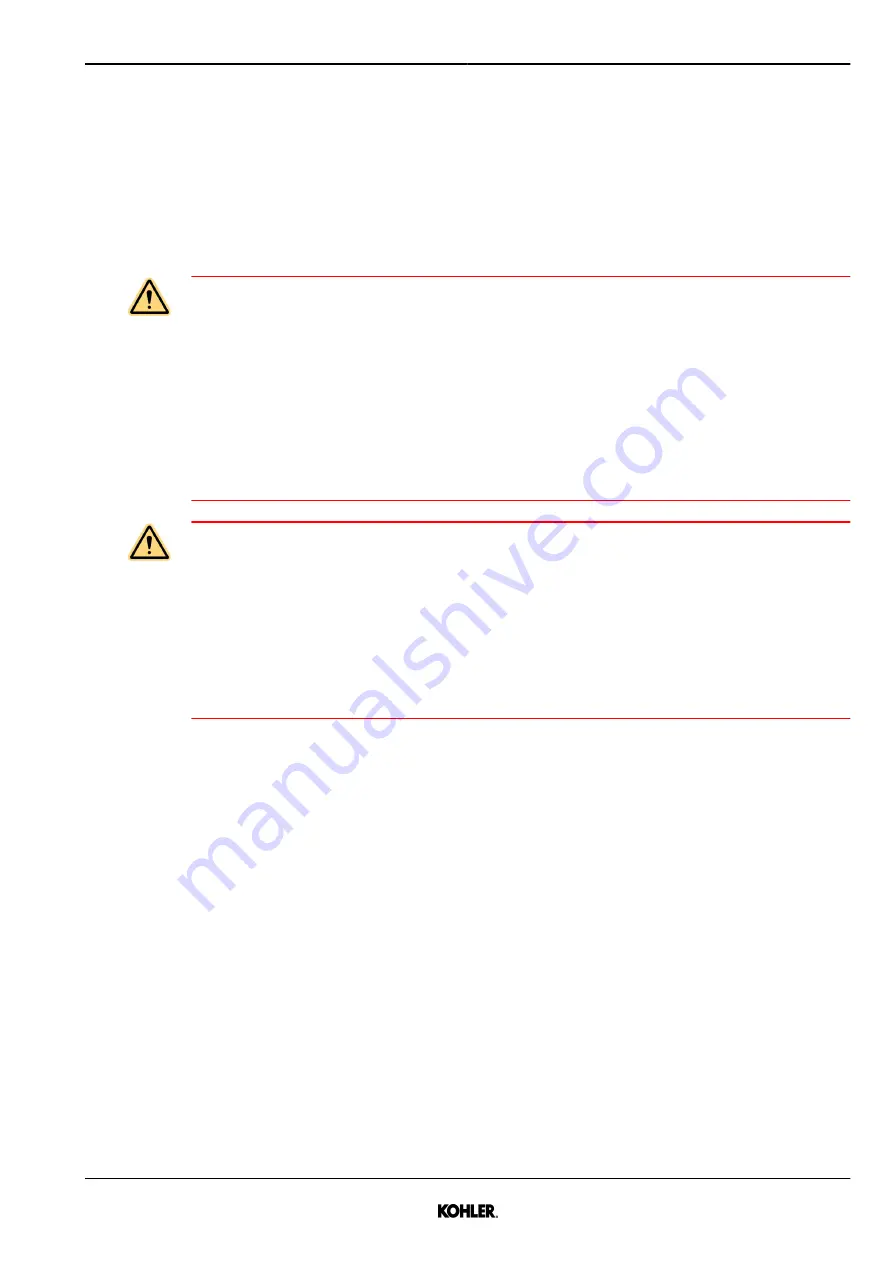
Service and Repair Manual
Repair
Covers
3.2.2 Battery charging alternator & PTO cover removal and installation
Previous tasks
Not applicable.
Specific safety instructions
DANGER
Hazards by entanglement, trapping, ejection of parts or impact.
On starting and while operation, hazards by entanglement, trapping, impact by ejection of parts will
result in death or serious injury.
u
The engine shall not be started until the drive train has been connected to the flywheel.
u
Ensure the integrity of the machine and the engine before starting.
u
All openings must be closed and the safe conditions established by the manufacturer of the
machinery must be fulfilled.
u
Standing in the vicinity of the engine while starting or operating the manufacturer’s machinery is
forbidden.
WARNING
Hazards by electrical shocks.
Contact with live conductor could result in death or serious injury.
u
Access to live parts shall only be possible with voluntary action.
u
Proceed to lock out and tag out prior to accessing to the engine.
u
Respect the voltage indication of the engine’s technical data sheet.
u
Check the grounding connection to avoid any risk of electrical arc.
u
Observe the local safety regulations that apply to the machinery.
Special tools
Not applicable.
Consumables and equipment
– Rags
– Cleaner
KD83V16 33525088901_2_1 EN_US
2021-07
© 2021 by Kohler Co. All rights reserved.
61