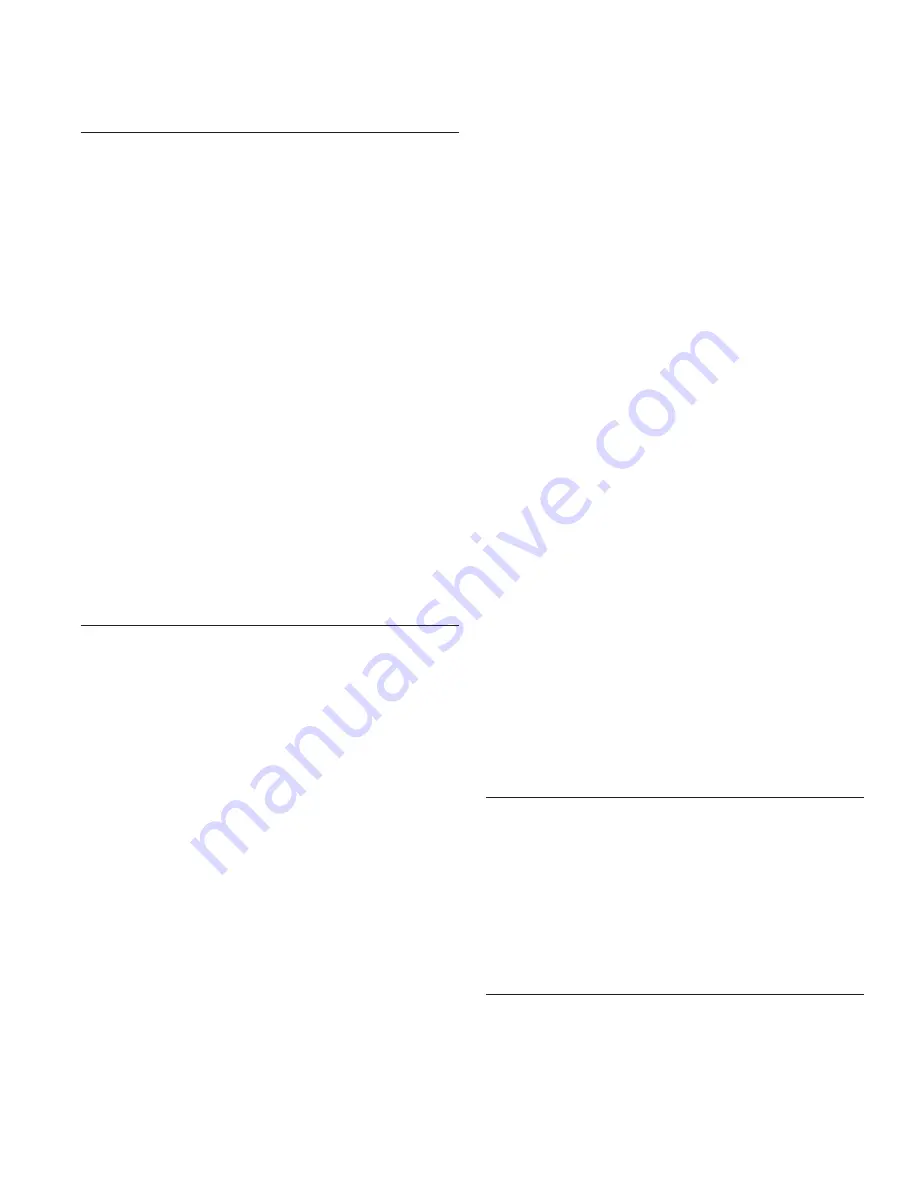
Reassembly
119
62 690 05 Rev. E
KohlerEngines.com
Install Guide Plate, Pivot Studs, Push Rods and
Rocker Arms
NOTE: Install push rod guide plate so fl ange is down
(towards cylinder) on side 1, and up (away from
cylinder) on side 2 (AVT only).
NOTE: Push rods should always be installed in same
position as before in disassembly.
Non-adjustable Valve Train
1. Position rocker arm pivots in sockets of rocker arms.
Insert screws through pivots, rocker arms, and guide
plate. Start screws into cylinder head and fi nger
tighten only at this time.
2. Note mark or tag identifying push rod as either
intake or exhaust and cylinder 1 or 2. Dip ends of
push rods in engine oil and install, making sure each
push rod ball seats in its hydraulic lifter socket. Align
rocker arms over valve stems. Hold rocker arm in
position and torque screws to 15.5 N·m (137 in. lb.).
Adjustable Valve Train
1. Install push rod guide plate and rocker arm pivot
studs onto cylinder heads if removed previously.
Torque studs to 11.3 N·m (100 in. lb.).
2. Note mark or tag identifying push rod as either
intake or exhaust and cylinder 1 or 2. Dip ends of
push rods in engine oil and install, making sure each
push rod ball seats in its hydraulic lifter socket.
3. Apply grease to contact surfaces of rocker arms and
rocker arm pivots. Install rocker arms, rocker arm
pivots, and adjusters on cylinder head 1.
Adjust Valve Clearance (AVT Only)
NOTE: It takes two hands to make lash adjustment. A
clamping device or an assistant to hold lifter
compressed while making adjustment will make
process easier.
1. Turn adjusters in rocker arms by hand clockwise
(down), only enough to capture push rods in
recesses.
2. Rotate crankshaft to establish TDC on compression
stroke for cylinder 1.
Check for:
a. Compression will be felt through spark plug hole.
b. Keyway of crankshaft will be aligned with cylinder
1.
c. No rocker arm/push rod movement if crankshaft
is rotated slightly back and forth. If they are
moving, rotate crankshaft one full revolution.
3. Pre-Bled Lifters:
a. Apply downward pressure to push rod side of
rocker arm to compress lifter and bottom internal
plunger. Several manual compressions may be
necessary. Hold in this position for step 3b.
b. Insert a 0.406/0.483 mm (0.016/0.019 in.) feeler
gauge between end of one valve and rocker arm.
Turn adjuster until a slight drag is felt. Hold
adjuster in this position and tighten locking
setscrew. Torque setscrew to 7.7 N·m (69 in. lb.).
After tightening recheck adjustment. Proper valve
clearance is 0.406/0.483 mm (0.016/0.019 in.).
c. Repeat procedure for other valve on this side.
Non-Bled Lifters (when cylinder heads and lifters are
not removed):
a. Turn 1 rocker arm adjusting nut from side 1 down
until push rod is snug but can be rotated with
drag. This is 0 lash.
b. Mark or note setting of adjustment nut, then turn
(tighten) adjuster nut 3 complete revolutions
clockwise, plus 3/4 turn, or a total of 3-3/4 turns.
c. Hold adjuster nut in this position and tighten
locking setscrew. Torque setscrew to 7.7 N·m (69
in. lb.).
d. Repeat procedure for other valve on this side.
4. Viewed from PTO end, rotate crankshaft 270° (3/4
turn) counterclockwise and align crankshaft keyway
with cylinder 2, which now puts that cylinder at TDC
on compression stroke.
5. Repeat steps 3-5 for setting valve clearance on
cylinder 2.
6. Rotate crankshaft to check for free operation of
valve train. Check for clearance between valve
spring coils at full lift, or bending of push rod(s) can
occur. Minimum allowable clearance is 0.25 mm
(0.010 in.).
Check Assembly
Rotate crankshaft a minimum of two revolutions to check
assembly and overall proper operation.
Check if engine can be turned over completely and
compression is noted. If it cannot (locks up at some
point), return piston to TDC between intake and exhaust
strokes fi rst for one cylinder and then other waiting ten
minutes to allow lifters to bleed down, then check for
compression again.
Install Valve Covers
1. Make sure sealing surfaces are clean and free of
any nicks or burrs.
2. Install and properly seat seal onto each valve cover.
3. Install valve covers on same side as they were
originally installed.
4. Install a new grommet on each valve cover mounting
screw. Start each screw into hole.
5. Check position of each cover and seal, then torque
screws to 13.6 N·m (120 in. lb.).
Install Spark Plugs
1. Check gap using wire feeler gauge. Adjust gap to
0.76 mm (0.030 in.).
2. Install plug into cylinder head.
3. Torque plug to 27 N·m (20 ft. lb.).