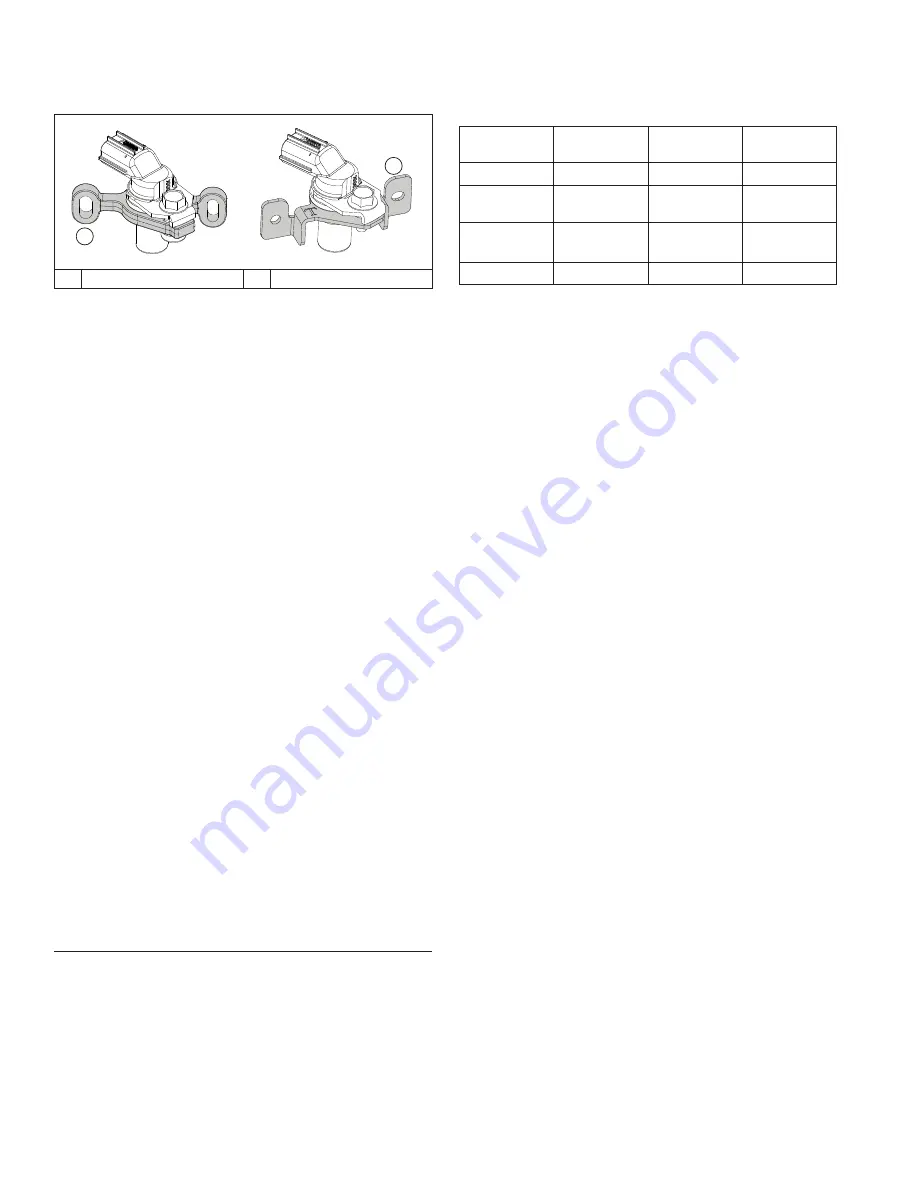
EFI SYSTEM
34
62 690 05 Rev. E
KohlerEngines.com
Crankshaft Position Sensor
B
A
A
Earlier Design Bracket
B
Later Design Bracket
A sealed, non-serviceable assembly. If fault code P0337
is present and engine does not start/run, proceed to step
1. If P0337 is present and engine operates, clear codes
and retest. If Fault Code diagnosis indicates a problem
within this area, test and correct as follows.
1. Check mounting and air gap of crankshaft position
sensor.
Earlier design bracket has slots to set air gap of
0.20-0.70 mm (0.008-0.027 in.).
Later design bracket is not adjustable, but if gap is
greater than 2.794 mm (0.110 in.) check bracket or
sensor for damage.
2. Inspect wiring and connections for damage or
problems.
3. Make sure engine has resistor type spark plugs.
4. Disconnect Black connector from ECU.
5. Connect an ohmmeter between #4 and #13 pin
terminals. A resistance value of 325-395 Ω at room
temperature (20°C, 68°F) should be obtained. If
resistance is correct, check mounting, air gap,
fl ywheel teeth (damage, run-out, etc.), and fl ywheel
key.
6. Disconnect crankshaft position sensor connector
from wiring harness. Test resistance between
terminals. A reading of 325-395 Ω should again be
obtained.
a. If resistance is incorrect, remove screws securing
sensor to mounting bracket and replace sensor.
b. If resistance in step 5 was incorrect, but
resistance of sensor alone was correct, test wire
harness circuits between sensor connector
terminals and corresponding pin terminals (#4
and #13) in main connector. Correct any
observed problem, reconnect sensor, and
perform step 5 again.
7. When fault is corrected and engine starts, clear fault
codes following ECU Reset procedure.
Throttle Position Sensor (TPS)
Earlier engines were built with a contacting (brush) type
TPS. Later engines are built with a contactless (magnet)
type TPS. Both designs have same three wires attached;
a 5 volt supply, a ground, and a signal wire. However,
these designs are not interchangeable. Follow proper
testing information based on sensor type.
Contacting (Brush) Type TPS
Resistance Table
Throttle
Position
Between
Terminal
Resistance
Value (Ω)
Continuity
Closed
A & C
1400-1800
Yes
Full with
Stop Pin
A & C
3200-4100
Yes
Full without
Stop Pin
A & C
4600-5200
Yes
Any
A & B
3000-7000
Yes
TPS is a sealed, non-serviceable assembly. If diagnosis
indicates a bad sensor, complete replacement is
necessary. If a blink code indicates a problem with TPS,
it can be tested as follows:
1. Counting number of turns, back out idle speed
adjusting screw (counterclockwise) until throttle
plates can be closed completely. Write this number
down for reference later.
2. Disconnect Black connector from ECU, but leave
TPS mounted to throttle body.
3. a. Use an ohmmeter and connect red (positive)
ohmmeter lead to Black pin 12 terminal and black
(negative) ohmmeter lead to Black pin 10 terminal
to test.
b. Hold throttle closed and check resistance. It
should be 1400-1800 Ω.
4. Leave leads connected to pin terminals as described
in step 3. Rotate throttle shaft slowly to full throttle
position. Monitor dial during rotation for indication of
any momentary short or open circuits. Note
resistance at full throttle position. It should be
4600-5200 Ω without a stop pin, or 3200-4100 Ω
with a stop pin.
5. Disconnect main wiring harness connector from
TPS, leaving TPS assembled to throttle body. Refer
to Resistance Table and perform resistance checks
indicated between terminals in TPS switch, with
throttle in positions specifi ed.
If resistance values in steps 3, 4, and 5 are within
specifi cations, go to step 6.
If resistance values are not within specifi cations, or a
momentary short or open circuit was detected during
rotation (step 4), TPS needs to be replaced, go to
step 7.
6. Check TPS circuits (input, ground) between TPS
plug and main harness connector for continuity,
damage, etc. Input pin is 12 and ground is pin 10.
a. Repair or replace as required.
b. Turn idle speed screw back in to its original
setting.
c. Reconnect connector plugs, start engine and
retest system operation.
7. Remove two mounting screws from TPS. Save
screws for reuse. Remove and discard faulty TPS.
Install replacement TPS and secure with original
mounting screws.
a. Reconnect Black and TPS connector plugs.
b. Perform TPS Learn Procedure integrating new
sensor to ECU.