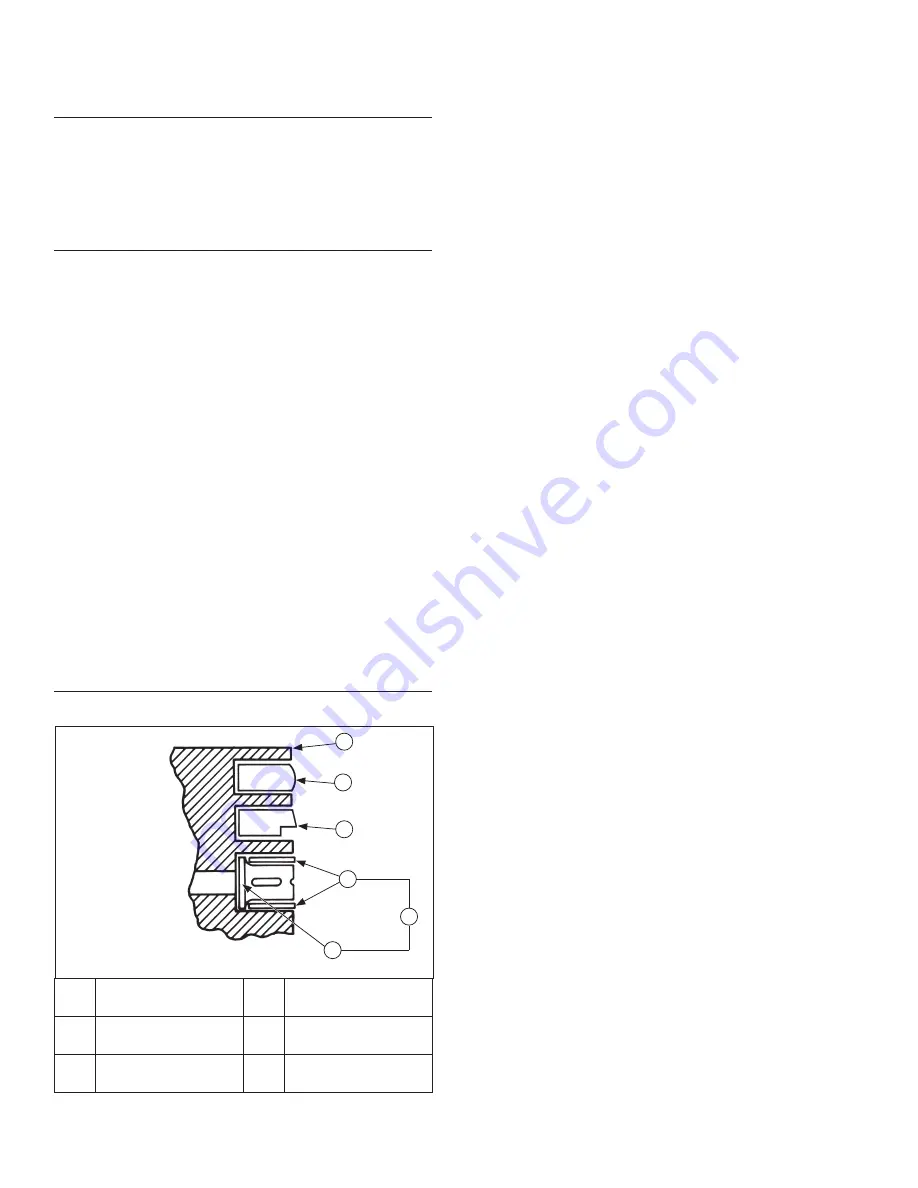
Disassembly/Inspection and Service
102
62 690 05 Rev. E
KohlerEngines.com
Remove Camshaft
Remove camshaft and shim (if used).
Inspection
Check lobes of camshaft for wear or damage. Inspect
cam gear for badly worn, chipped, or missing teeth.
Replacement of camshaft will be necessary if any of
these conditions exist.
Remove Connecting Rods with Pistons and Rings
NOTE: If a carbon ridge is present at top of either
cylinder bore, use a ridge reamer tool to remove
ridge before attempting to remove piston.
NOTE: Cylinders are numbered on crankcase. Use
numbers to mark each end cap, connecting rod
and piston for reassembly. Do not mix end caps
and connecting rods.
1. Remove screws securing closest connecting rod end
cap. Remove end cap.
2. Carefully remove connecting rod and piston
assembly from cylinder bore.
3. Repeat above procedures for other connecting rod
and piston assembly.
Connecting Rods
Off set, stepped-cap connecting rods are used in these
engines.
Inspection and Service
Check bearing area (big end) for excessive wear, score
marks, running and side clearances. Replace rod and
cap if scored or excessively worn.
Service replacement connecting rods are available in
STD crankpin size and 0.25 mm (0.010 in.) undersize.
Always refer to appropriate parts information to ensure
that correct replacements are used.
Piston and Rings
Inspection
Piston and Rings Components and Details
A
Piston
B
Top Compression
Ring
C
Middle Compression
Ring
D
Rails
E
Expander
F
Oil Control Ring
(3 Piece)
A
B
C
D
F
E
Scuffi ng and scoring of pistons and cylinder walls occurs
when internal engine temperatures approach welding
point of piston. Temperatures high enough to do this are
created by friction, which is usually attributed to improper
lubrication and/or overheating of engine.
Normally, very little wear takes place in piston boss-
piston pin area. If original piston and connecting rod can
be reused after new rings are installed, original pin can
also be reused but new piston pin retainers are required.
Piston pin is included as part of piston assembly – if pin
boss in piston or pin are worn or damaged, a new piston
assembly is required.
Ring failure is usually indicated by excessive oil
consumption and blue exhaust smoke. When rings fail,
oil is allowed to enter combustion chamber where it is
burned along with fuel. High oil consumption can also
occur when piston ring end gap is incorrect because
ring cannot properly conform to cylinder wall under this
condition. Oil control is also lost when ring gaps are not
staggered during installation.
When cylinder temperatures get too high, lacquer and
varnish collect on pistons causing rings to stick, which
results in rapid wear. A worn ring usually takes on a
shiny or bright appearance.
Scratches on rings and pistons are caused by abrasive
material such as carbon, dirt, or pieces of hard metal.
Detonation damage occurs when a portion of fuel charge
ignites spontaneously from heat and pressure shortly
after ignition. This creates 2 fl ame fronts which meet and
explode to create extreme hammering pressures on a
specifi c area of piston. Detonation generally occurs from
using low octane fuels.
Preignition or ignition of fuel charge before timed spark
can cause damage similar to detonation. Preignition
damage is often more severe than detonation damage.
Preignition is caused by a hot spot in combustion
chamber from sources such as glowing carbon deposits,
blocked cooling fi ns, an improperly seated valve, or
wrong spark plug(s).
Replacement pistons are available in STD bore size, and
in 0.25 mm (0.010 in.), and 0.50 mm (0.020 in.) oversize.
Replacement pistons include new piston ring sets and
new piston pins.
Replacement ring sets are also available separately
for STD, 0.25 mm (0.010 in.), and 0.50 mm (0.020 in.)
oversize pistons. Always use new piston rings when
installing pistons. Never reuse old rings.
Some important points to remember when servicing
piston rings:
1. Cylinder bore must be deglazed before service ring
sets are used.
2. If cylinder bore does not need reboring and if old
piston is within wear limits and free of score or scuff
marks, old piston may be reused.
3. Remove old rings and clean up grooves. Never
reuse old rings.
4. Before installing new rings on piston, place top 2
rings, each in turn, in its running area in cylinder
bore and check end gap. Top and center
compression ring end gap clearance is 0.30/0.55
mm (0.011/0.021 in.) with maximum wear limit of
0.94 mm (0.037 in.).