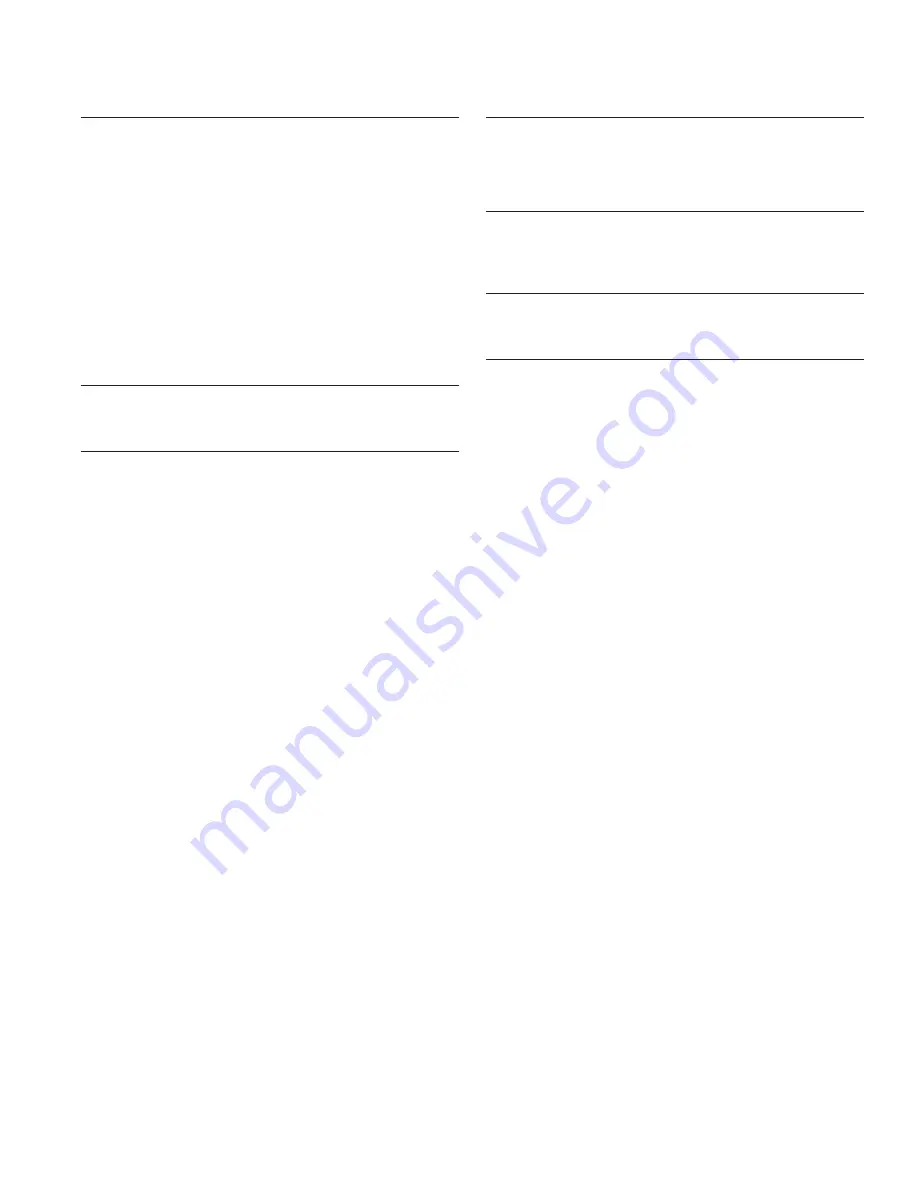
Reassembly
125
62 690 05 Rev. E
KohlerEngines.com
Install Electric Starter
1. Install electric starter motor using screws.
2. Torque screws to 16 N·m (142 in. lb.).
3. Connect main power lead and solenoid lead.
Install Blower Housing/Guard Assembly
Align and install blower housing with fi xed guard. Secure
with screws. Torque screws to 2.5 N·m (22 in. lb.) into
new holes, or 2.0 N·m (18 in. lb.) into used holes.
Install Fuel Pump
Install fuel pump to blower housing and secure with
screws. Torque screws to 2.8 N·m (25 in. lb.).
Install Cylinder Shrouds
Install cylinder shrouds and secure with screws. Torque
screws to 2.5 N·m (22 in. lb.) into new holes, or 2.0 N·m
(18 in. lb.) into used holes.
Install Valley and Cylinder Barrel Baffl
es
1. Install #1 side valley baffl e and secure with 3
screws. Reinstall clip securing harness to baffl e.
Install #2 side valley baffl e and secure with 3
screws. Torque M6 screws going into cylinder head
and crankcase to 10.7 N·m (95 in. lb.) for new holes,
or 7.3 N·m (65 in. lb.) for used holes.
2. Install cylinder barrel baffl es. Make sure spark plug
lead is routed through corresponding opening in
each baffl e. Start each screw. Torque M6 shoulder
screws going through backing shroud assembly into
extruded holes in baffl es to 2.5 N·m (22 in. lb.) into
new holes, or 2.0 N·m (18 in. lb.) into used holes.
Torque M6 screws going into cylinder head and
crankcase to 10.7 N·m (95 in. lb.) for new holes, or
7.3 N·m (65 in. lb.) for used holes.
Torque Oil Cooler Screws
1. Align oil cooler with bosses in backing shroud
assembly. Torque screws to 2.3 N·m (21 in. lb.).
Install Fuel Pump Module/Fuel Pump Assembly
NOTE: Ensure all parts are clean, undamaged, and free
of debris; make sure electrical connector has
seal in place.
NOTE: Fuel pump module pins should be coated with a
thin layer of electrical grease to prevent fretting
and corrosion and may be reapplied if fuel pump
module is being reused.
1. Orient fuel pump module baffl e so pulse fi tting in
crankcase extends through cutout in baffl e.
2. Connect pulse line (from fuel pump) to crankcase
fi tting.
3. Install screws to secure fuel pump module/baffl e
assembly to crankcase. Torque screws to 11.9 N·m
(105 in. lb.). If fuel pump module was removed from
baffl e, after installing baffl e, install fuel pump module
to baffl e and torque screws to 9.2 N·m (81 in. lb.).
4. Connect electrical connector to top of fuel pump
module. Ensure grey locking tab is pulled out before
connecting. Push connector onto terminal until a
click us heard, then push in grey locking tab to lock
connector.
5. Push high pressure fuel line connector onto fuel
pump module fi tting.
6. If Oetiker clamp was cut to remove inlet fuel line,
slide a new Oetiker clamp onto fuel line and connect
fuel line to fuel pump module. Only use an Oetiker
clamp pliers to crimp Oetiker clamps. Oetiker clamp
crimp must point up and away from top of fuel pump
module and anti-abrasion sleeve must be positioned
over Oetiker clamp.
7. Install connectors to #1 and #2 side ignition coils.
8. Orient/push line clamps into baffl es. Push evap line
into clips on high pressure fuel line. Connect evap
line to vent fi tting on fuel pump module.