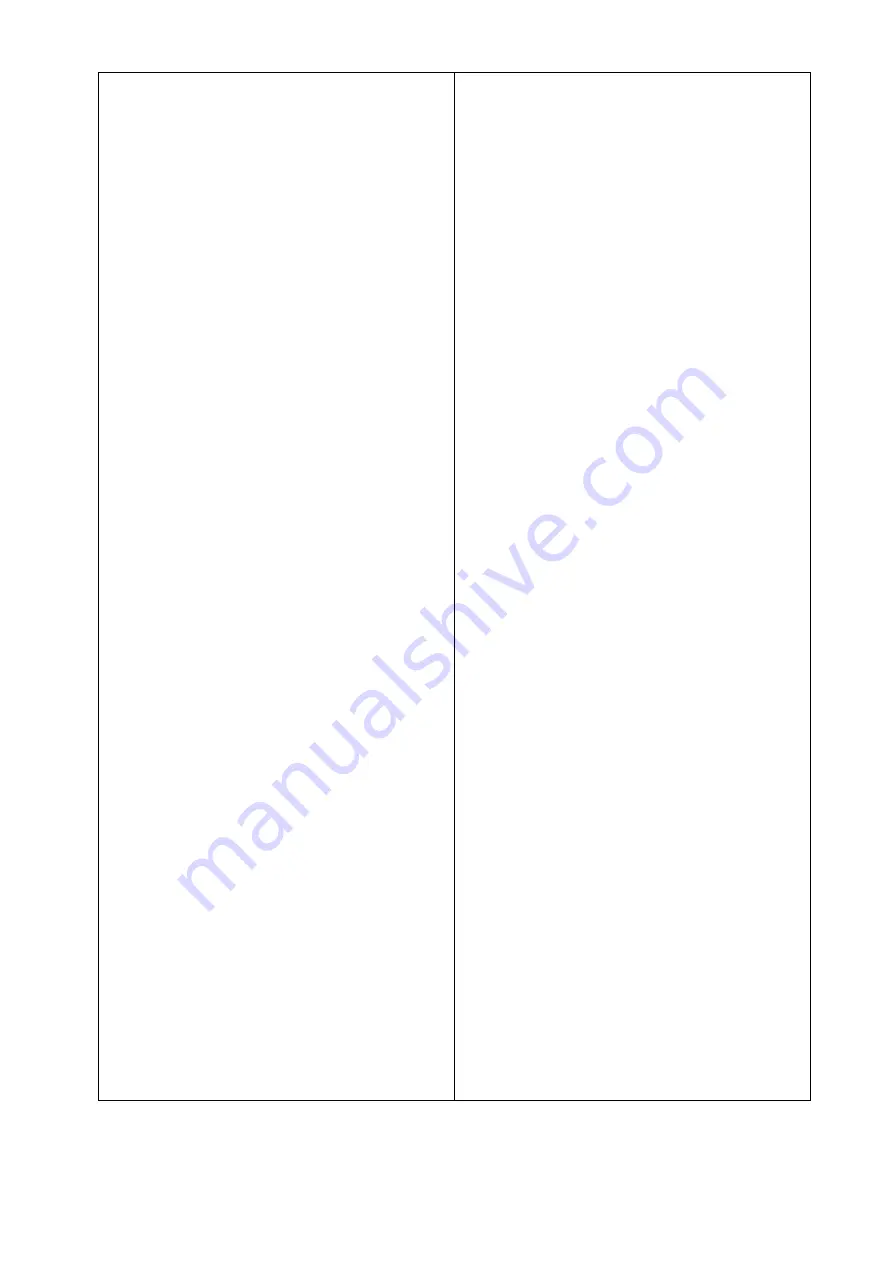
Data ultimo aggiornamento: 04/04/2018
Pag. 18 di 48
OSHA (OCCUPATIONAL SAFETY &HEALTH ACT): Inspectors for OSHA
are responsible for monitoring general air quality indoors where people are
employed.
OUTDOOR AIR QUALITY: The quality of air outside of enclosures. Outdoor
air quality maybe degraded by the presence of smog, exhaust from internal
combustion engines, factory smokestacks, home heating systems, etc.
OXYGEN SENSOR: A sensor placed in the exhaust stream which generates
an output signal from an electrochemical reaction that is dependent on the
concentration of oxygen in the exhaust.
TWA (TIME WEIGHTED AVERAGE): The average exposure over a specified
period. EXAMPLE: OSHA TWA limit for CO is 50 ppm exposure for 8
continuous hours.
TWA is difficult to measure but can be easily calculated from the CO reading
in ambient air using the following formula: TWA = 173.6 x C x D x R x N x T A
x H
Where C = % CO in ambient air; D = engine size in cubic inches; R = engine
RPM while operating; N = number of cylinders; T = operating time in hours;
A = area of store in square feet; H = ceiling height of store in feet.
Example: A store has 25,000 sq. ft. area and 10foot ceilings with the
ventilation turned off and doors closed. A 30.1 cubic inch, 2 cylinder propane
powered buffer is used for 2 hours at 3600 rpm engine speed. The CO
reading is 0.01% (100 ppm) which is the average of the reading taken after
the first hour of operation and that taken after the second hour of operation.
TWA = 3.0 ppm, which is far below the 50 ppm OSHA limit.
APPENDIX
: SUGGESTED GUIDELINES FOR
PROPANE POWERED FLOOR CARE MACHINES
PURPOSE
To ensure the safety of all persons occupying or visiting buildings in which
propane powered floor care machines are being used to maintain floors, the
following guidelines will be followed by all floor care contractors.
TRAINING
1. All operators of propane powered floorcare machines will be properly
trained and certified in the safe operation of propane powered floor care
machines. They are required to have, on their person, a valid certification
card indicating what training they have successfully completed. The employer
(contractor) is responsible for documenting training.
2. Each person engaged in installing, repairing, or servicing an LP-Gas
engine fuel system shall be properly trained and certified for the necessary
procedures. (NFPA 58 8-1.4)
FIRE SAFETY
1. An MSDS (Material Safety Data Sheet) for propane shall be posted in all
buildings where propane will be used.
2. A lockable ventilated metal locker or rack (cage), will be supplied and used
to store fuel cylinders outside in accordance with NFPA 58 5-4.2.1(b).
3. Each fuel cylinder will be checked for “over-fill” before it is taken into the
building. NO overfilled cylinders will be taken into the building.
4. All fuel cylinders will be stored OUTSIDE in the storage locker(cage) when
not in use. Absolutely no fuel cylinders will be stored inside the building. The
propane powered floor care machine may be kept in the building when not
being used but the fuel cylinder MUST be removed from the machine and
stored outside in the cage.
5. No more than two fuel cylinders will be allowed in the building for each
machine being used at any time (one on the machine and one if the crew is
“locked in” and cannot get outside for a refill during their shift).
PROPANE POWERED FLOOR CARE MACHINES
1.Only UL listed propane powered floor care machines will be used. Those
with component listing only will NOT be allowed.
2. Each propane powered floor care machine will be maintained in a “Safe”
condition at all times. To assure compliance, the following is required of each
propane powered floor care machine used.
a
. Each machine will be services monthly or after every 100 hours of use.
b
. A “Machine Maintenance Record” will be kept on each machine showing:
• Serial number
• Service performed
• Hour meter reading
• Condition of the machine and fuel system
• PPM (parts per million) of carbon monoxide as recorded IN the exhaust
muffler or tail pipe at full throttle before any adjustments have been made.
• PPM of carbon monoxide as recorded IN the muffler or tail pipe at full
throttle after any adjustments have been made (CARBON MONOXIDE
READINGS AT THIS POINT WILL NEVER EXCEED 1500 PPM).
3. One copy of the “Machine Maintenance Record” of each machine used in
the building will be filled with the Manager of the Building/Store. Failure to do
this could terminate the contract.
4. Dust and air filters must be inspected and cleaned before each operation of
the machine. At no time is the machine to be operated with a dirty filter or
without the filter in place.