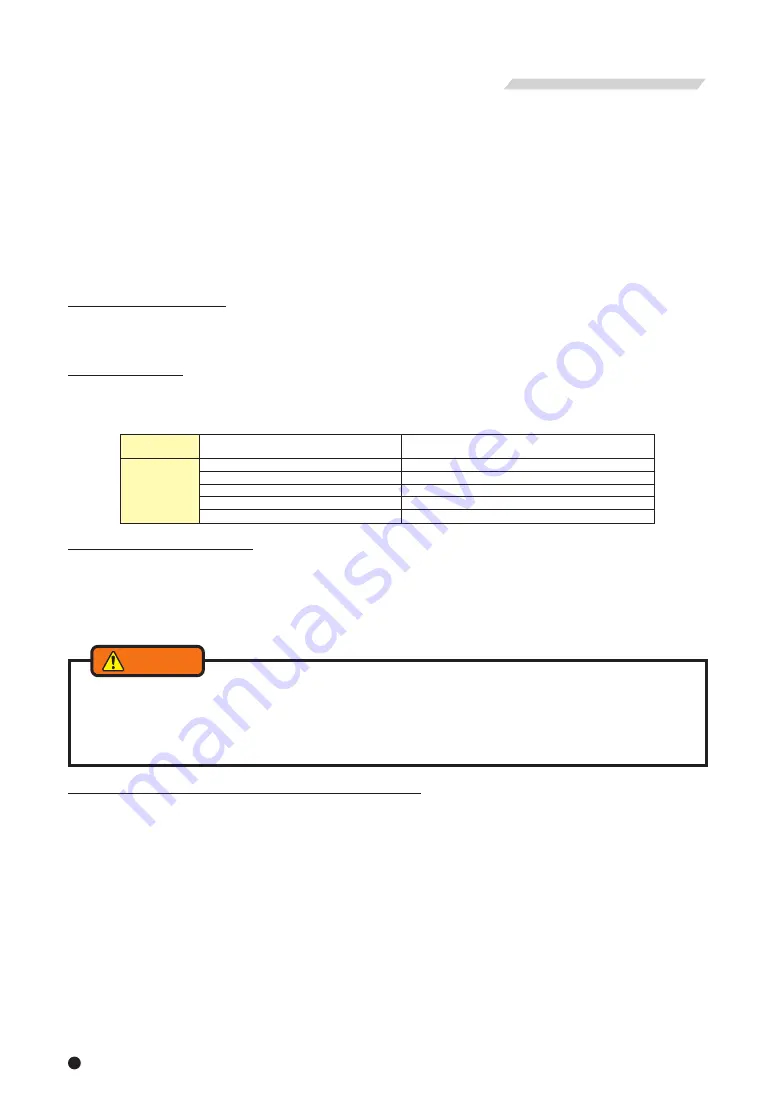
21
22
・Add grease at least once a day.
・Fully stroke the jaw before starting work or upon supplying grease, and check that the jaw is inside the appropriate
stroke area. (Refer to page 17)
・Always clean the chuck body or the sliding surface using an air gun, etc., at the end of work.
・Check that the bolts of each part are not loosened at least once every 3 months.
・Disassemble and clean at least once every 6 months or every 100,000 strokes (once every 2 months or more for
cutting cast metal).
1. Position to lubricate
・Lubricate using a grease gun from the grease nipple on the body periphery part. Supply grease when the jaw is open.
After lubrication, repeat opening and closing the jaw several times without gripping work.
2. Grease to use
・Use the designated grease specified in Table 7. If grease other than the designated grease is used, sufficient effect
may not be obtained.
3. Frequency of lubrication
・Add grease once every day.
・Add approximately 5g up to 8 inches and 10g for 10 inches or larger of grease to the each master jaw. Check the
filling degrees of the grease after removing the cover of the chuck center.
・In the case of high rotation or in the case of using a large amount of water soluble coolant, increase the frequency of
lubrication according to the usage conditions.
4. Safety information about grease and anti-rust oil
Applicable range
・Designated grease
・Antirust agent applied to the product at the delivery.
First aid measures
A f t e r i n h a l a t i o n : Remove victim to fresh air. If symptoms persist, call a physician.
After contact with skin: Wash off with mild cleaners and plenty of water. If symptoms persist, call a physician.
After contact with eyes: Rinse with plenty of water. If symptoms persist, call a physician.
A f t e r i n g e s t i o n : If large amounts are swallowed, do not induce vomiting. Obtain medical attention.
・Please refer to each MSDS about the grease and the anti-rust oil which you prepared.
6-1. Periodic Inspection
6-2. Grease lubrication
6. Maintenance and Inspection
・To keep the chuck running in the best condition for a long time, adequate grease lubrication is necessary.
Insufficient grease lubrication causes a drop in the gripping force, operation failure at low hydraulic pressure,
drop in gripping precision, abnormal wearing, seizing, etc. The work will fly out due to a drop in the gripping force
and this is dangerous.
Type
HW-08
HW-10
HW-12
HW-15
Eyebolt
M10
M12
M12
M12
・Remove the eyebolt or the belt without fail after using. If the chuck is rotated with the eyebolt, etc., attached, they
may fly out and this is dangerous.
・Disassemble and clean the chuck at least once every 6 months or every 100,000 strokes (once every 2 months
or more for cutting cast metal). If cutting powder or other substances stagnate inside the chuck, it will lead to
insufficient stroke and a drop in the gripping force, and this is dangerous as the work will fly out. Check each part
carefully and replace any part that is worn or cracked.
・After inspection, apply sufficient grease in the designated areas and reassemble.
・After assembling, measure the gripping force according to the method on page 13, and check that the specified
gripping force is obtained.
・If you stop the machine for a long period of time, remove the work from the machine. If you don't, the work can
drop due to a drop in the hydraulic pressure or the cylinder can stop or malfunction.
・If you stop the machine or store the chuck for a long period of time, add grease to prevent rust.
6-3. Disassembling
Disassembling procedures
Read the following disassembling procedures with reference to page 5.
1.Turn off the main power of the machine before starting work.
2.Loosen the jaw attaching bolt [19], and remove the soft jaw [6] and the T-nut [10]. (4 place)
3.Loosen the socket head cap screw [21], and remove the cover [11].
4.Loosen the draw screw [14] with the hex key, and remove the plug [12].
5.Loosen the lock nut locking screw [28], and remove the lock nut [13] with the handle [17].
6.Loosen the chuck attaching bolt [18], and remove the chuck from the spindle.
7.Remove the socket head cap screw [20].
8.Loosen the set screw [23][26], and remove the lever pin [8][9].
9.Remove the master jaw [4][5].
10.Remove the lever [7], the plunger [2] and the plunger piston [3].
11.Assemble again while sufficiently coating the recommended grease in the reverse procedures of disassembling
(Refer to page 21). At this time, pay sufficient attention so as not to make a mistake in the numbers of the body,
master jaw, and the plunger piston. Always tighten the bolts at the specified torque (Refer to page 9).
12.Refer to page 28 about the installation procedure. (8-4. Attachment of chuck).
・Use an eyebolt or a hanging belt when attaching and detaching the chuck to and from the machine, as there is a
danger of injury or damage if the chuck drops.
Table 7
Genuine
product
Conventional
product
CHUCK GREASE PRO
Kitagawa chuck grease
Molykote EP Grease
Chuck EEZ grease
MOLYKOTE TP-42
Kluberpaste ME31-52
Kitagawa genuine product
(Kitagawa distributor of each country)
Conventional product
TORAY Dow Corning (only inside Japan)
Kitagawa-Northtech Inc. (North American region)
Dow Corning (Europe, Asian region)
Kluber lubrication (worldwide)
WARNING
WARNING
CAUTION
Содержание HW-08
Страница 31: ......