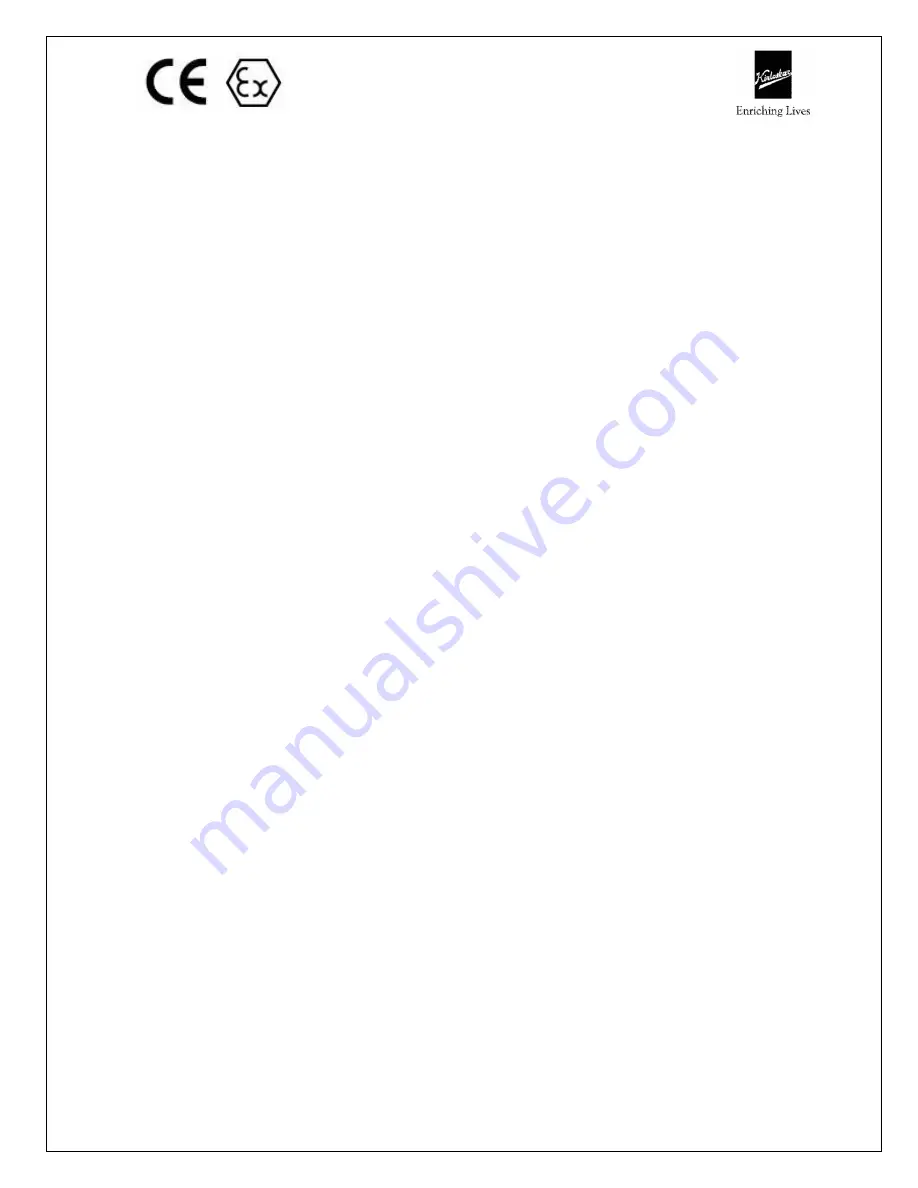
IOM/GK(P)/CONICAL ISSUE DATE: 10.11.2015
Page 9 LAST REV. DATE: 01.08.2019
A. Any auxiliary systems installed must be monitored, if necessary, to ensure they
function correctly.
B. Check for any leaks from gaskets and seals. The condition of the mechanical
seal must be checked regularly to ensure correct functioning.
C. Check that the duty condition is in the safe operating range for the pump.
D. Check that dirt and dust is removed from operational areas of the pump.
E. Inspect the GK(P) pumps at least every 1000 running hours and renew if any
sign of damage is apparent.
A.10 Additional Safety Instructions
A) Pumps and ancillary equipment must be drained, cleaned and decontaminated
prior to any change of duty.
B) Where pumps and ancillary equipment contain non-conductive plastic wetted
components, dismantling for maintenance must take place in a safe area away
from the flammable hazard, or the equipment made safe by purging with
nitrogen.
C) When installing a pump either for the first time or after maintenance, a check
must be made to ensure that the earth connection terminal on the pump and
any external metalwork is at ground potential.
D) Where a counter or count and stop device is fitted, it is for indicating the
number of cycles run only, and not to use as a means of process flow control or
for performing a safety function.
E) Ensure nozzle forces and bending moments should not exceed the maximum
permissible values as specified in technical documents.
PART B:
INSTRUCTIONS ON INSTALLATION, OPERATION AND
MAINTENANCE FOR KIRLOSKAR PUMP TYPE GK(P)
1.
GENERAL:
1.1
‘KIRLOSKAR’
make GK(P) pumps are used for handling various types of
chemical liquids. These pumps are manufactured to close tolerance and are
of rigid construction. However, proper installation, operation and
maintenance are equally important to ensure trouble free service. This
booklet covers important guidelines and instructions for installation,
operation and maintenance. These instructions should be followed carefully
for satisfactory performance of the pumping unit. Only mechanical aspects
are dealt within this booklet.
1.2
Applications:
GK(P) pumps are mainly used in process industries like petrochemicals,
nuclear, refinery, fertilizer, paper, sugar, etc., and power plants. The pump
can handle corrosive acids, alkalies, salt solutions, caustics, hydro-carbons,
oils, liquefied gases, condensates, viscous liquids, etc.