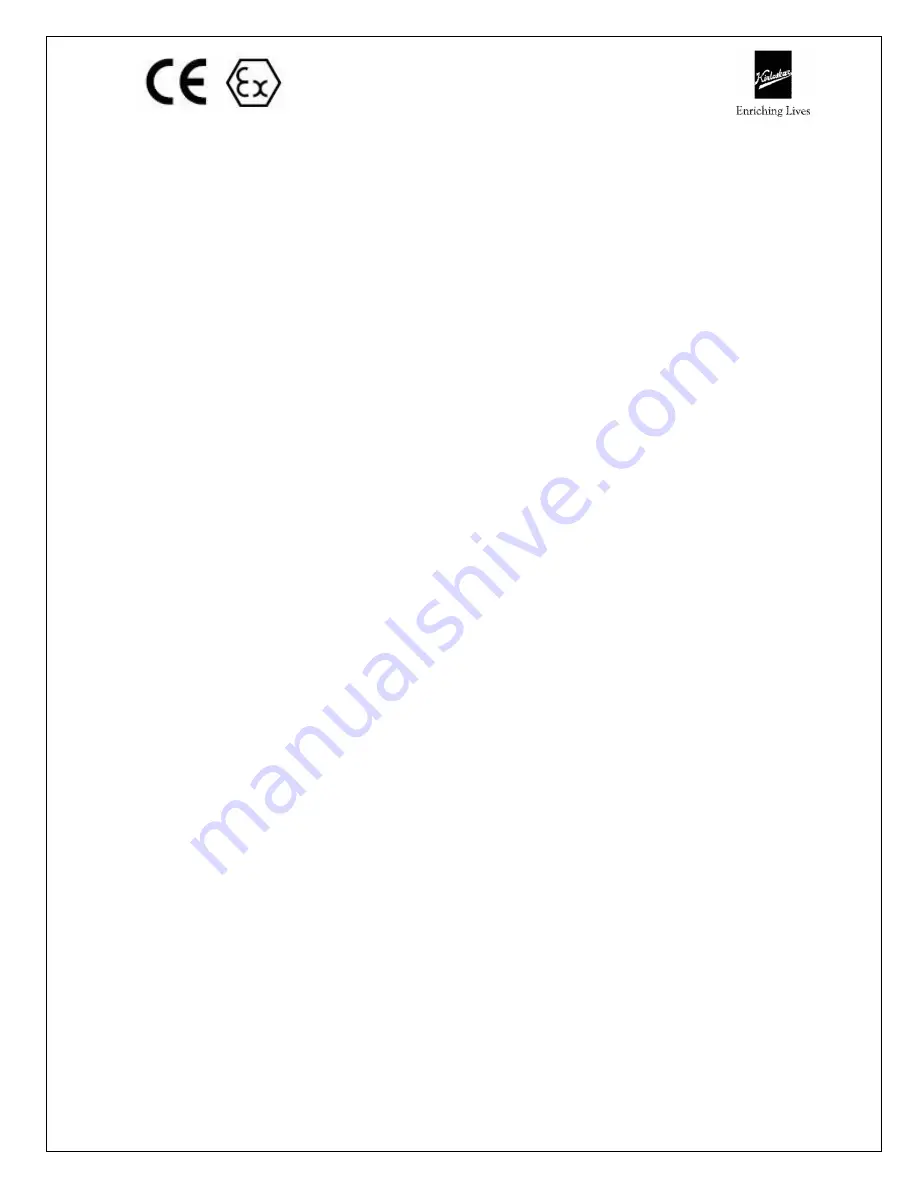
IOM/GK(P)/CONICAL ISSUE DATE: 10.11.2015
Page 38 LAST REV. DATE: 01.08.2019
5.3.3.2 The effects of liquid handled on pump components should be checked. If
abnormal corrosion, erosion is observed, the component should be
replaced with that of suitable material.
5.3.3.3 The auxiliary pipelines and functioning of the auxiliary system should be
checked. The main pipe also should be checked for scaling, leakage, etc.
5.3.3.4 The measuring instruments, gauges etc., should be recalibrated.
5.3.3.5 Full running test may be carried out to check whether there is any fault in
the performance, in comparison with original performance.
5.3.3.6 Piping supports should be checked so that the pipes do not induce
unwanted stresses on the pump.
In case failure to check above points & maintain proper records/precautions of
checks by customer / user, KBL warranty gets void.
5.3.4 Mechanical seal in pump:
The mechanical seal is a precision product having been subjected to quality
control throughout all stages of manufacture. The seals are designed to
accommodate reasonable tolerances in the equipment, however in order to
obtain the maximum life with trouble free performance, the equipment
should be adequately maintained.
When mechanical seal is functioning satisfactorily without any leakage, the
preventive maintenance is not advocated. If leakage occurs, a thorough
check up is needed. While fitting the mechanical seals in the pump initially
by KBL, due care is taken for its proper fitment.
Like other parts in the equipment the mechanical seals are subject to wear at
the mating faces of the rotating and stationary ring. The rate of wear will
differ with the operating conditions and various other factors such as
lubricating property of the liquid pumped, the presence of impurities in liquid
and other operating conditions. In view of this no firm recommendations can
be given for renewal of seal rings / complete seals.
GK(P) pumps are supplied with cartridge type factory assembled mechanical
seals and no further operating length adjustments are required.
Flushing
: Flushing at the mechanical seal faces is necessary to provide
lubrication, cooling of the seal faces and hence pump should not be run
without flushing at the seal faces. Please refer mechanical seal assembly
drawing for flushing liquid pressure and temperature.
Throttle bush:
Throttle bush is pressed in mechanical seal cover. This bush
gives protection in case of seal’s failure. Due to close clearance between
bush and the shaft sleeve, if the seal fails, the pressure of the product is
reduced before it escapes. This bush also minimizes the quench leakage
along the shaft. To avoid possibility of the sparking, the bush is made of
non-ferrous materials as per API specifications.