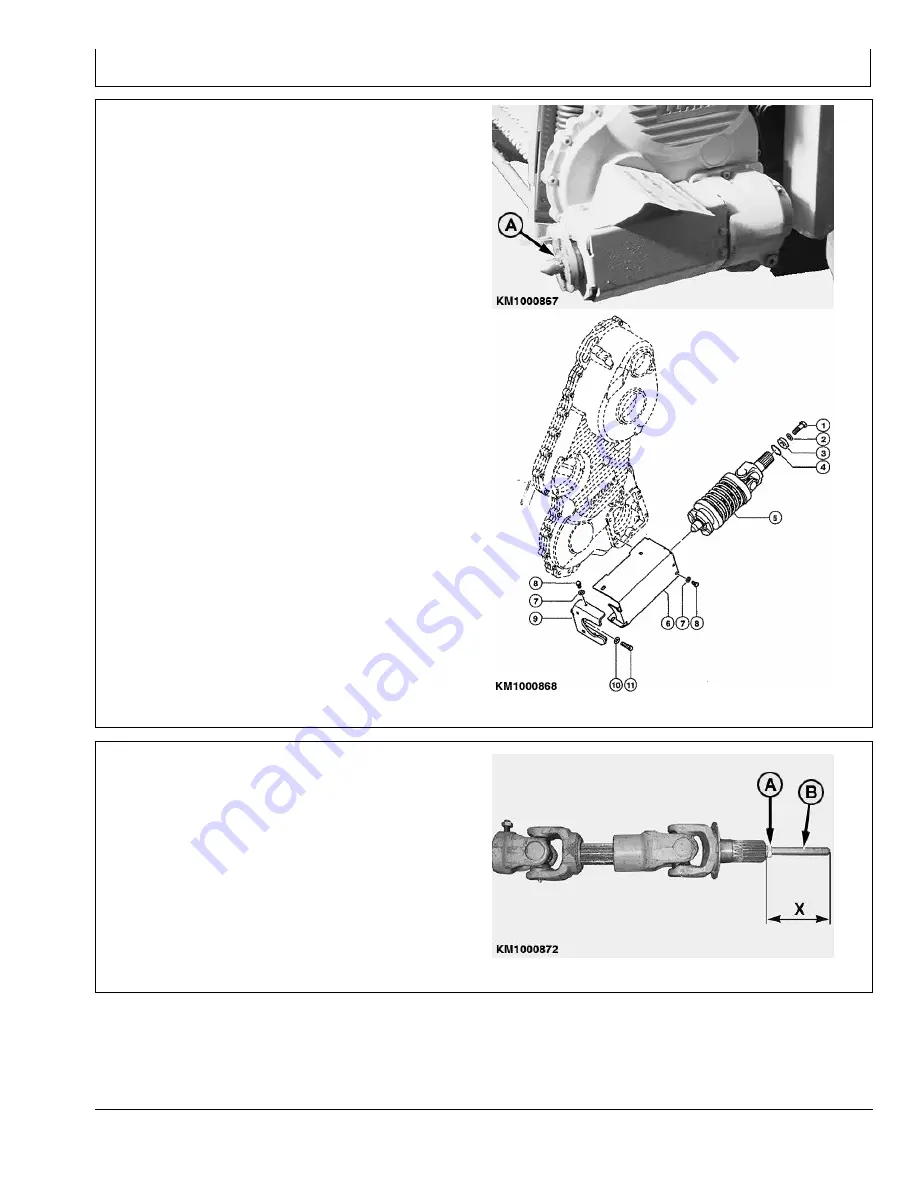
Attaching to a Claas forage harvester
KM00321,0000880 -19-18DEC18-1/9
Continued on next page
KM00321,0000880 -19-18DEC18-2/9
Connecting the Drive (Forage Harvester
Types 493, 494, 497, and 498)
1. Completely remove claw clutch (A) from rotary
harvesting unit drive.
To do this, disassemble items 1 to 11.
A—Claw clutch
KM1000867
—UN—26MA
Y09
KM1000868
—UN—26MA
Y09
2. Screw threaded rod (B) into the universal-jointed shaft,
adjust to 167 mm (6.57 in.) (X) and counterlock with
hex nut (A).
A—Hex nut
B—Threaded rod
X—167 mm (6.57 in.)
KM1000872
—UN—26MA
Y09
20-16
031519
PN=43
Содержание 345plus
Страница 6: ...Contents iv 031519 PN 4 ...
Страница 126: ...Index Index 4 031519 PN 4 ...