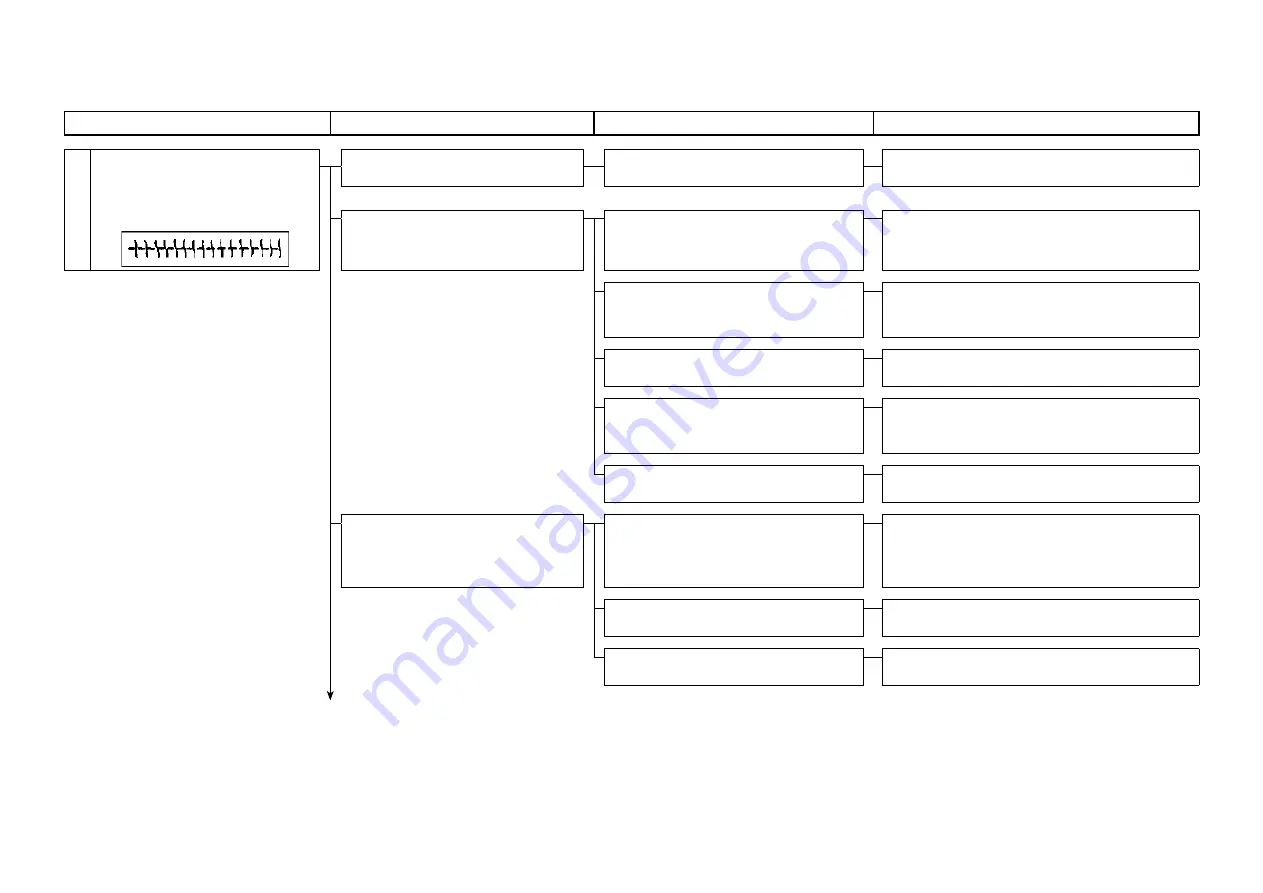
– 140 –
Trouble
Cause (1)
Cause (2)
Check and corrective measures
1. Puckering
Wrinkles developed around
stitches due to stitch shrinkage or
uneven material feed.
1-1) The needle is too thick.
1-A) Deformation of clothes by pene-
trating a needle into cloth
Use a thin needle as much as possible. Use a
KN or SF needle (standard needle).
1-2) Thread tension (top or bot-
tom) is too high.
2-A) The thread path is not smooth.
Finish the thread path appropriately.
2-B) The timing of the hook is too
late.
Hasten the timing of the hook without oc-
currence of stitch skipping to obtain smooth
unthreading.
2-C) The feed timing is too fast.
Delay the feed timing compared to the needle
timing to reduce feeding.
2-D) The stroke of the thread take-
up lever is too long.
Move the arm thread guide rightward to reduce
the thread feeding with the thread take-up
lever.
2-E) The stroke of the thread take-
up spring is too short.
Increase the stroke.
1-3) Pressing is inappropriate.
3-A) The pressure is too high.
Minimize the pressure. For some materials,
sewing with the presser slightly floated with the
adjustable screw of the minute presser lifter is
effective.
3-B)
The finish of the backside of the
presser is rough.
Use a buff or the like to smooth the presser.
3-C)
The material is difficult to feed.
Use a fluorocarbon resin presser or a special
processed presser.
To the next page
(2) Sewing performance
Содержание DDL-8000A
Страница 1: ...40218604 No E440 00 ENGINEER S MANUAL DDL 8000A Direct drive High speed Automatic Thread Trimmer ...
Страница 91: ... 78 ...
Страница 117: ... 104 ...
Страница 170: ... 157 ...