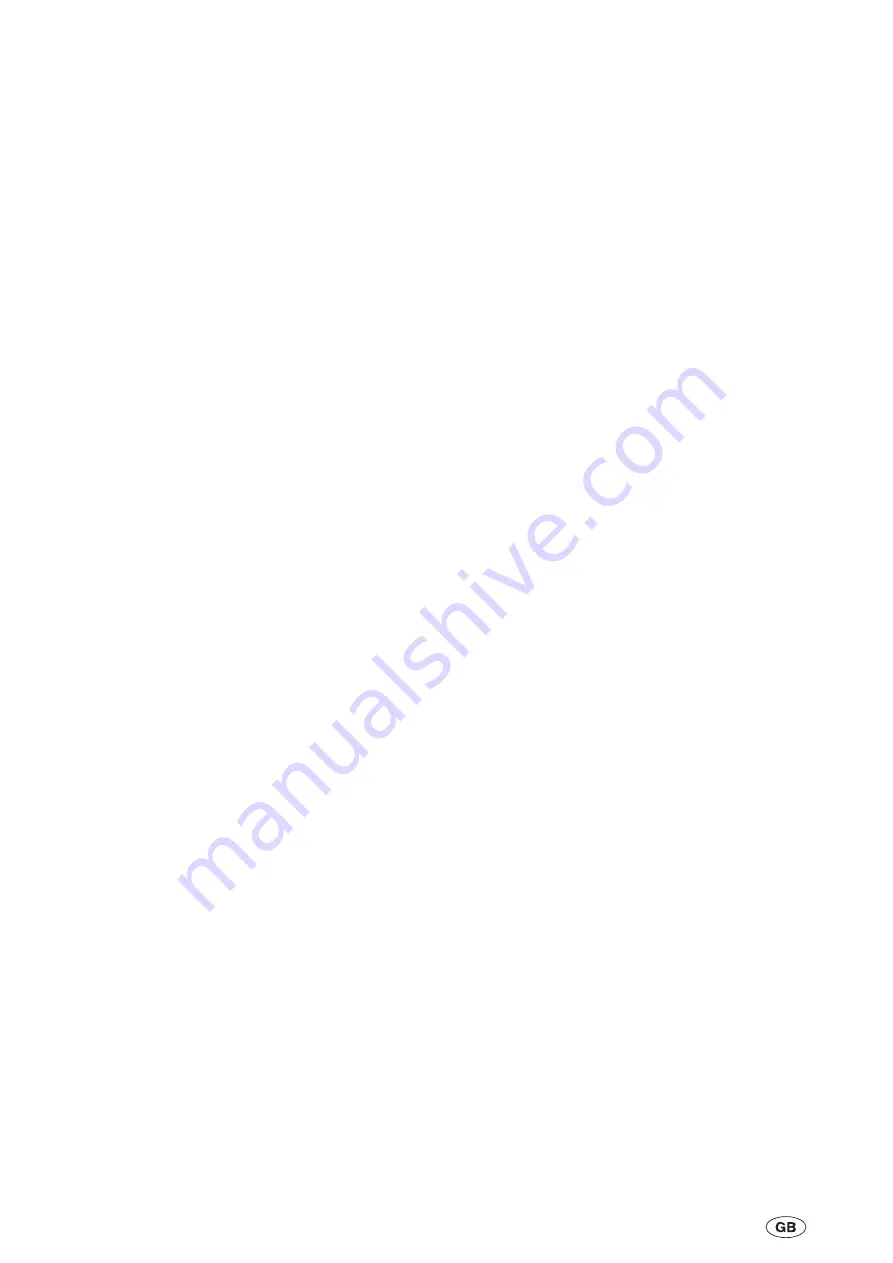
The lag compressors in a system, are not controlled by
the anti-recycle timer. They have no start to start timer
other than the effect of system lead/lag rotation and the
load/unload timers. For a given compressor this gives a
minimum start to start time of 140 seconds on systems
with 2 compressors or 210 seconds on systems with 3
compressors. Their minimum stop to start time for a
given compressor is 60 seconds, the 60 second load
timer.
When the leaving chilled liquid temperature is above the
Setpoint High Limit, the lead compressor on the lead
system will be energised along with the liquid line
solenoid.
After 60 seconds of run-time if the leaving chilled liquid
temperature is still above the Setpoint High Limit and the
leaving chilled liquid temperature is not falling faster
than the programmed RATE SENSITIVITY within the
programmed RATE CONTROL TEMPERATURE
R A N G E
o r
a b o v e
t h e
R A T E
C O N T R O L
TEMPERATURE RANGE at 1.7°C per minute, the next
compressor in sequence will be energised.
Additional loading stages are energised at a rate of one
every 60 seconds if the chilled liquid temperature
remains above the Setpoint High Limit and the same
criteria on leaving chilled liquid temperature rate of
change as above are met.
The strategy for loading/unloading is design to meet the
following criteria:
1. Minimise system starting and stopping;
2. The lag system is not available to start until the lead
system cannot load further and has been running for
5 minutes;
3. When both systems are running, balance loading /
unloading between them.
With both systems running the next system to load is
determined by the following rules;
1. The system must not be fully loaded or pumping
down;
2. Remote load limit, suction limiting or discharge
limiting must not be in effect on the system.
If both systems are available to load the system with the
lowest number of compressors running will load. If both
systems have the same number of compressors
running the lead system will load.
On units without soft start the strategy for compressor
loading within a system is to maximize individual
compressor run time and ensure that the same
compressor does not start twice in a row. This is
achieved by rotating the lead/lag sequence of the
compressors in a system when a compressor other than
the lag most compressor in that system stops. In
achieving this objective no attempt will be made to
equalize each compressors individual total run hours
within a system.
On units with soft start the compressor in each system
with soft start is always the last to start. Compressors
are always started in the same order, No1 compressor
first.
If the chilled liquid temperature falls below the Setpoint
High Limit but is greater than the Setpoint Low Limit,
loading and unloading do not occur. This area of control
is called the 'CONTROL RANGE'.
If the chilled liquid temperature drops to less than
0.28°C below the Setpoint Low Limit, unloading occurs
at a rate of 30 seconds. If the chilled liquid temperature
falls to a value greater than 0.28°C below the Setpoint
Low Limit but not greater than 0.83°C below the Setpoint
Low Limit, unloading occurs at a rate of 15 seconds. If
the chilled liquid temperature falls to a value greater
than 0.83°C below the Setpoint Low Limit, unloading
occurs at a rate of 10 seconds. If the leaving chilled
liquid temperature falls to 0.6 °C above the leaving liquid
temperature cutout, unloading occurs at a rate of 10
seconds.
If more than one compressor is running in a system then
on unloading the compressor to be stopped is not the
same compressor stopped during the last unload
sequence. This is achieved by rotating the lead lag
sequence of the compressors in a system when a
compressor in that system stops.
The leaving chilled liquid 'SETPOINT' is programmable
from 4.4°C to 21.1°C in the chilled liquid water mode and
from -7°C to 21.1°C in chilled liquid glycol mode. In both
modes, the 'RANGE' can be from +/-0.8°C to 1.4°C. A
low temperature glycol unit is available which will go
down to -13°C.
1
-
6
Form 201.26.OI1(11/09)