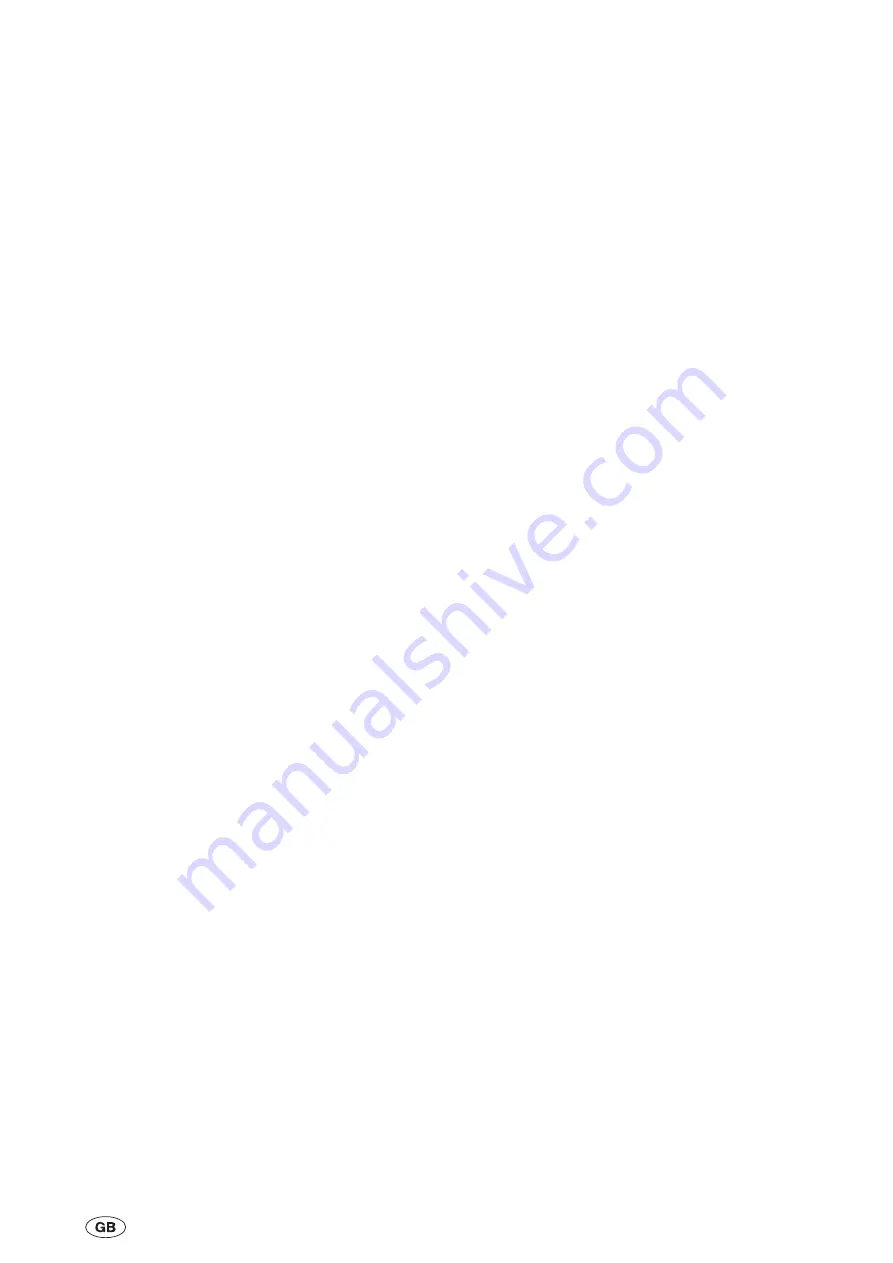
1
GENERAL
The units are designed to work independently, or in
conjunction with other equipment via ISN, Bacnet or
Modbus building management systems or other
automated control systems. When operating, the unit
controls monitor the chilled liquid system temperatures
at the unit and take the appropriate action to maintain
the temperatures within desired limits. This action will
involve running one or more compressors to match the
cooling effect of the refrigerating systems to the heat
load on the liquid system. The heat removed from the
chilled liquid is then rejected to the air or water cooled
condenser.
1.1
Control Panel
A microprocessor based control system is fitted to the
units. It is capable of dual refrigerant system (circuit)
control to maintain chilled liquid temperature within
programmed limits, as well as sequencing, system
safeties, displaying status, and daily schedules.
Remote cycling, demand limiting and chilled liquid
temperature reset can be accomplished by field
supplied contacts.
Compressor starting/stopping and loading/unloading
decisions are performed by the microprocessor to
maintain leaving liquid temperature. These decisions
are a function of temperature deviation from
‘SETPOINT’.
A master (UNIT) ON/OFF switch is provided on the
chiller control panel to activate or deactivate the
complete chiller.
On YLAA and YLAE units with the optional Hydro kit the
control of the single or duty/standby pumps are integral
to the control system.
1.1.1
AMB (IPU II and I/O Boards)
The IPU and I/O boards are assembled to function as a
single microprocessor controller. The IPU II board
contains a 'Coldfire' microprocessor and is the controller
and decision maker in the control panel. The I/O board
handles all of the unit I/O (Inputs and Outputs). System
inputs from pressure transducers and temperature
sensors are connected to the I/O board.
The I/O board contains a processor capable of reading
the inputs and controlling the outputs. It communicates
through the transition header with the IPU II
microprocessor. The I/O board circuitry multiplexes the
analog inputs, digitizes them, and constantly scans
them to keep watch on the unit operating conditions.
The input values are transmitted serially to the IPU II
microprocessor board.
From this information, the IPU II then issues commands
to the I/O board relay outputs to control contactors,
solenoids, etc. for Leaving Liquid Temperature Control
and to react to safety conditions. The I/O board converts
logic signals to operate relay outputs to 115 VAC levels
used by motor contactors, solenoid valves, etc. to
control system operation. The low voltage side of all
relay coils on the I/O board are powered by +12V.
Keypad commands are actuated upon by the
microprocessor to change setpoints, cutouts,
scheduling, operating requirements, and to provide
displays. The keypad and display are connected to the
I/O board.
The on-board power supply converts 24 Vac from T1
(120/24 VAC transformer), to +12 Vdc, +5 Vdc and +3.3
Vdc using switching and linear voltage regulators
located on the I/O and IPU II boards. These voltages are
used to operate integrated circuitry on the board. The
power supply for the 40 Character Display and unit
sensors (transducers and temperature sensors) is also
derived from the +5 V. supply. The 24 Vac is also
rectified, but not regulated, to provide unreg30
Vdc to supply all of the digital inputs.
The IPU II board contains one green 'Power' LED to
indicate that the board is powered up and one red
'Status' LED (flashing) to indicate that the processor is
operating.
The I/O board contains one green 'Power' LED to
indicate that the board is powered up and one red
'Status' LED (flashing) to indicate that the processor is
operating. The I/O board also contains two sets of
Receiver/Transmit LED’s, one for each available serial
communication port. The receive LED’s are green, and
the Transmit LED’s are red.
A jumper on the I/O board selects 20 mA or 10 Vdc as
the input type on the remote temperature reset analog
input.
1.1.2
Internal Clock & Memory Backup Battery
The AMB board contains a real time clock (RTC)
integrated circuit chip with an internal battery backup.
The battery backup assures that any programmed
values (setpoints, clock, cut-outs, etc.) are not lost
during a power failure or shutdown period regardless of
the time involved.
1
-
1
Form 201.26.OI1(11/09)