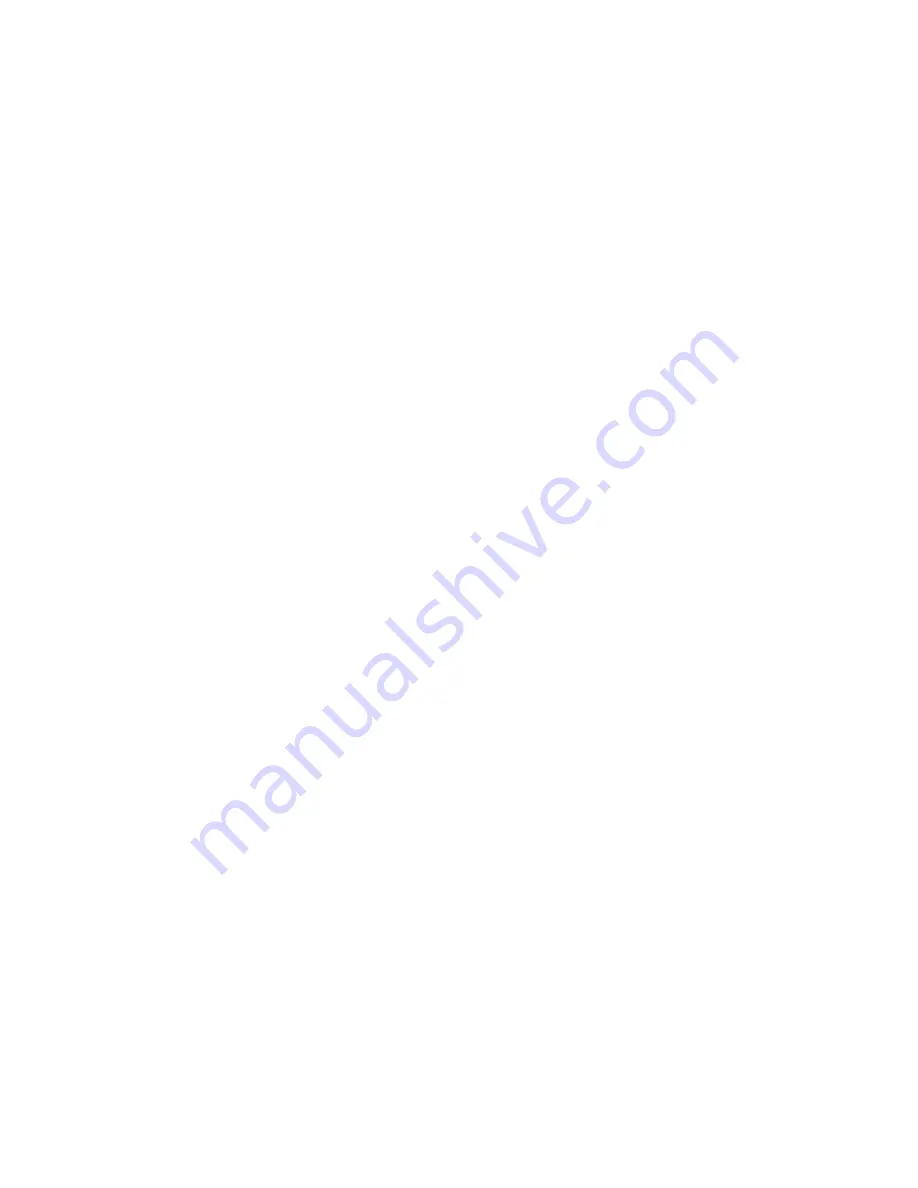
JOHNSON CONTROLS
8
FORM 160.00-O10
ISSUE DATE: 8/24/2020
SECTION 1 - GENERAL INFORMATION
The new power unit consists of a newly designed bus
capacitor, new light weight plastic cooling blocks, new
power module gate driver design, new rectifier mod-
ule, and the cooling system is connected to the front of
the power unit for reduce down time and service cost.
The new bus capacitor is the core of the power unit.
The new capacitor is made of a material that is much
more robust and has a longer lifetime than bus capaci-
tors commonly used in the past. Also, this capacitor
contains all of the hardware required to mount all of
the other parts of the power unit.
The harmonic filtering is now part of the input to the
OSCD. This feature is no longer an option when this
OSCD is used.
New special plastic cooling blocks were designed for
this OSCD. These plastic cooling blocks provide a light
weight solution by replacing heavy copper or alumi-
num cooling blocks, while providing direct liquid cool-
ing for the rectifier and inverter power modules. They
also provide a method for mounting the power module
assemblies to the bus capacitor within the power unit.
The power unit contains all of the items needed for the
output of the OSCD in a highly integrated, but modular
design. On top of the bus capacitor is the laminated
bus structure and the gate driver board. One gate board
per power assembly controls the rectifier and inverter
power devices. The gate driver board isolates the turn-
on and turn off commands from the drive logic board.
The gate driver board also conditions the commands
so that the power devices are properly turn on and off.
The rectifier and inverter assemblies are attached to
each side of the bus capacitor. The rectifier or inverter
assemblies can be replaced in the field. A bus bleeder
resistor is mounted on top of each power unit to dis-
charge the energy store in the bus capacitor when the
chiller is placed into the stop condition.
Ease of maintenance is provided by using the commu-
nications link between the OptiView™ panel and the
OSCD. The cooling pumps and fans can be turned on
from the OptiView™ panel. This provides for a safer
annual coolant change. The programmed chiller full
load amps is now programmed from the OptiView
panel.
OPTISPEED COMPRESSOR DRIVE DETAILS
The 1300 HP drive contains 3 power assemblies. Each
power assembly contains 2 capacitors with the rectifier
of the left side of the power assembly, and the inverter
on the right side of the power assembly. Due to the size
of the power assemblies, the enclosure has 3 doors. See
. The center and right doors can-
not be opened unless the circuit breaker is placed in the
off position, and the left door is open.
An electronic circuit breaker connects the three phase
input power to input fuses and then onto the AC line
inductor, and input filter. See
Three phase power continues onto the rectifier power
modules to the bus capacitor to the inverter, then onto
the output filter and to the compressor motor.
The AC line inductor provides isolation between the 3
phase power source and the input to the drive. The AC
line inductor improves the input current waveform so
that it appears more like a sine wave. The input filter
reduces the effects of the high frequency switching of
the rectifier and provides the inductance for boosting
the bus voltage above the peak of the line voltage.
The higher bus voltage is required for harmonic current
correction at the input of the OSCD, and to provide the
correct output voltage to the motor when the line volt-
age is less than the voltage required for the compressor
motor.
As with all drives, the bus capacitors need to be pre-
charged. This is a process that limits the amount of cur-
rent flowing into the bus capacitors. If this limit was
not provided, then the input fuses and or the circuit
breaker may open.
The precharge operation functions in the following
manner. A precharge contactor and resistors limit the
inrush current during the precharge time. The pre-
charge contactor is directly controlled by the drive log-
ic board. During the precharge period the drive logic
board will command the precharge contactor to close
for 12 seconds. During this time, the voltage will in-
crease across the bus capacitors, and the current will
be limited by the precharge resistors. This 12 second
period is called the precharge time. After 12 seconds
has passed, a small pilot relay directly controlled by
the drive logic board will close, and cause the supply
contactor to close. Shortly, after this time the precharge
contactor will open. The drive is now precharged and is
ready to run. The supply contactor will remain closed
until the chiller is placed into the stop condition.