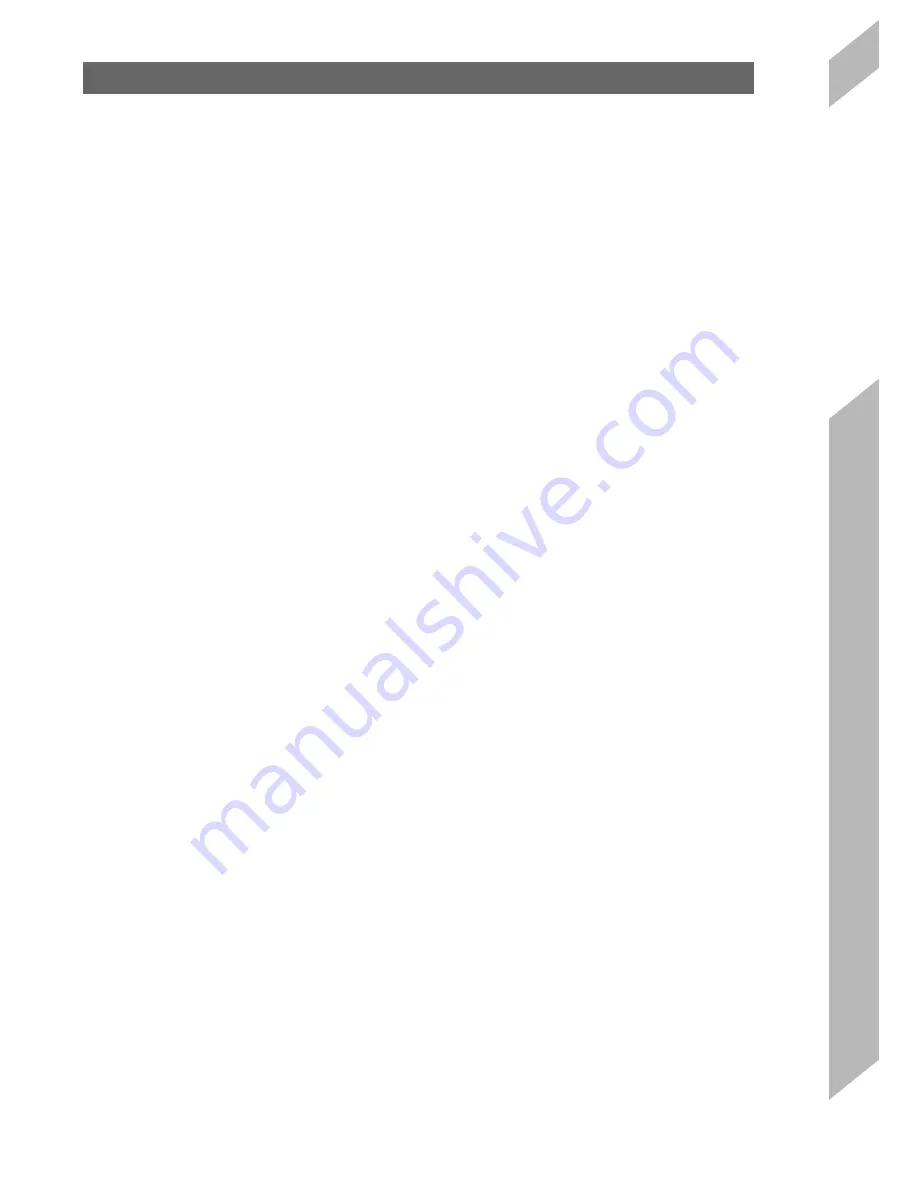
11
Sales/Spares & Replacement Help Line 01604 762881
8. HEATING
SYSTEM
8.1
The installation must comply with all relevant national and local regulations.
All components of the system must be suitable for a working pressure of 3 bar and temperature of 110°C. Extra
care should be taken in making all connections so that the risk of leakage is minimised.
NOTE:
a. The method of filling, refilling, topping up or flushing sealed primary hot water circuits from the
mains via a temporary hose connection is only allowed if acceptable to the local water authority.
b. Antifreeze fluid, corrosion and scale inhibitor fluids suitable for use with boilers having stainless
steel heat exchangers may be used in the central heating system.
8.2 EXPANSION
VESSEL:
The integral expansion vessel is pre-charged to a pressure of between 0.5 and 1.0 bar.
This should be checked before the water system is filled. Table 3 show the water system volume that is acceptable
for this vessel. If the system water volume is larger then an additional vessel must be fitted to the system. BS 5449
and BS 6798 gives further details regarding expansion vessel sizing and sealed systems. See Table 3.
8.3 PRESSURE
GAUGE:
The appliance has two components that monitor pressure. Firstly there is a mechanical
pressure gauge on the CH flow outlet, this allows the heating system to be pre-plumbed and filled with a visual
check on the pressure. The second is an electronic device used by the microprocessor control to monitor the
system pressure and block the heat input, should there be a lack of pressure.
8.4 PRESSURE
RELIEF
VALVE:
The pressure relief valve protects the system from over pressurisation. It is set to be
fully open at 3 bar, however it will start to open at approximately 2.7 bar. It should not be used to flush the system.
Using no less than 15mm diameter copper pipe, the discharge pipe must be extended to a safe place outside the
building. The discharge position must be visible, not onto a public access area or above any window or entrance.
The pipe must have a continuous fall and discharge to a safe place. It is possible that boiling water and/or steam
could be discharged if the safety valve operates.
8.5 FILLING
LOOP:
The g
roup set incorporates a filling loop that temporarily connects the DHW supply to the CH
system. This is used to fill the CH system on installation and whenever the water pressure has been removed for
system modifications, etc. The filling loop complies with the water supply (water fittings) regulations 1999 Section
G24.1 and G24.2. After filling the system the hose should be disconnected and stored in a safe place for future use.
8.6 PIPEWORK
SIZING:
In order to keep the noise of the system to a minimum, the velocity of water should be kept
below 1.5m/s and it should be noted that the appliance is designed to operate with a temperature differential of
20
˚
C between flow and return. The maximum flow rates are 0.3 kg/s which, through a 22mm pipe, gives velocities
of 1.00m/s. Therefore, the recommended minimum pipe size for the main carcass is 22mm.
8.7
DOMESTIC HOT WATER SYSTEM REQUIREMENTS
The DHW service must be in accordance with BS 5546 & BS 6700.
8.7.1
Domestic hot water circuits and their components, must be in accordance with the relevant standards
and water supply regulations. Further guidance/recommendations can be found in building regulations
G17 to 24 and R17 to 24.
8.7.2
The maximum domestic cold water supply pressure allowable for this appliance is 5 bar. If the supply
pressure exceeds this, a pressure-reducing valve must be installed in the supply to the appliance.
8.7.3
If the water to the property is “hard”, more than 200ppm of salts, then a scale inhibitor should be fitted.
Such products are available from Salamander.
NOTE:
The system must not be filled with ‘softened’ water. The cold water filling position should be before
any softening product.
8.7.4
In areas of low mains water pressures the domestic hot water regulator may be removed from the DHW
flow turbine cartridge. The boiler will require the flow rate to be set to obtain a temperature rise of 35°C at
the tap furthest from the boiler.
8.7.5
The boilers are suitable for connection to most types of washing machine and dishwasher appliances.
8.7.6. When connecting to suitable showers, ensure that:
a.
The cold inlet to the boiler is fitted with an approved anti-vacuum or syphon non-return valve.
b.
Hot and cold water supplies to the shower are of equal pressure.
IMPORTANT:
Provision must be made to accommodate the expansion of DHW contained within the
appliance. If the DHW inlet contains a back flow prevention device or non-return valve, e.g. A water
meter, then a mini expansion vessel should be fitted between the device and the boiler in the cold inlet
pipe.