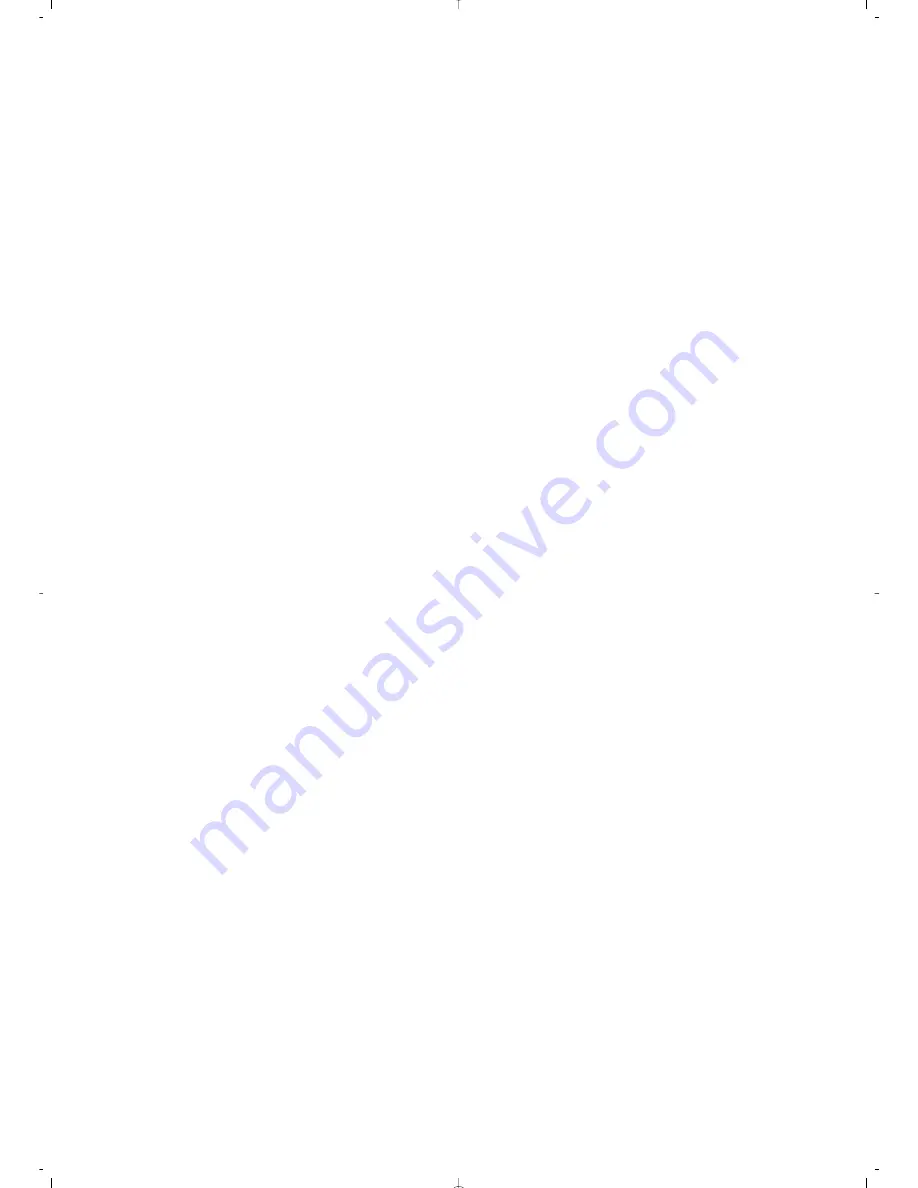
www.johnsonandstarley.co.uk
6
The installation must be tested for gas soundness using suitable methods. The pipework should also be purged of air
in accordance with the above standard.
Additional Plumbing Kit for Top Outlet CH Pipes:
Should the installation require the heating flow and return pipes to exit the appliance upwards, provision has been
made to allow the installation of two pipes (flow & return) to pass up the rear left hand side. These pipes are made
on site. Pre-fabricated pipes (kit number VPK30) are available direct from Johnson & Starley should they be required.
Additional Control Options:
Should an outside temperature compensation system be required, Opentherm kits are available direct from Johnson &
Starley. (Part No.1000-0019720)
2.5 Appliance Location:
The appliance is not suitable for external installation unless it is protected from the elements by a suitable enclosure.
The enclosure must provide the required clearances for installation, servicing and maintenance as well as the correct
level of ventilation. The selected position should allow for a suitable flue system to be installed.
When installed in a timber frame building guidance should be taken from the British Gas publication IGE/UP-7 (Guide
for Gas Installations in Timber Frame Housing).
BS 6798 gives details of the essential features for a compartment or cupboard where a gas appliance is to be
installed. An existing cupboard may require modification.
If the appliance is installed in a room containing a bath or shower it is important to locate the electrical switch in a
position where it cannot be touched by anyone using the bath or shower. The current IEE Wiring Regulations (BS
7671) for England and the electrical provision of the Building Regulations for Scotland gives details.
Room ventilation for the appliance is not necessary as the appliance draws its combustion air from outside of the
building and cupboard or compartment ventilation is not necessary providing that the minimum clearances are main-
tained. However, reference should be made to BS5440 Pt.2
2.6 Heating System Requirements:
This appliance incorporates all the necessary components to allow it to be connected to a sealed central heating sys-
tem. A typical system is shown at fig. 2.2 which incorporates radiators, an automatic by-pass valve and a drain facili-
ty that must be provided at the lowest point in the system to allow complete drain down. The installation should be
designed to operate with a flow temperature of up to 90 deg.C.
Expansion Vessel:
The integral expansion vessel is pre-charged to a pressure of between 0.5 and 1.0 bar. This should
be checked before the water system is filled. Details below show the water system volume that is acceptable for this
vessel. If the system water volume is larger then an additional vessel must be fitted to the system. BS 5449 and BS
6798 give further details regarding expansion vessel sizing and sealed systems. See table 3-2 page 9
Pressure Gauge:
The appliance has two components that monitor pressure. Firstly there is a mechanical pressure
gauge on the plumbing jig, this allows the heating system to be pre-plumbed and filled with a visual check on the
pressure. The second is an electronic device used by the microprocessor control to monitor the system pressure and
block the heat input, should there be a lack of pressure.
LCD Display:
When the electrical supply is connected, the liquid crystal display indicates the system water pressure. This
pressure is also monitored by the microprocessor controls.
Pressure Relief Valve
: The pressure relief valve protects the system from over pressurisation. It is set to be fully open
at 3 bar, however it will start to open at approximately 2.7 bar. It should not be used to flush the system.
Filling:
Provision for filling the CH system must be made and three methods are shown in fig. 2.3 Connections to the
mains supply must not be permanent, even through a non-return valve. Fittings used for connection to potable water
must comply with the water supply (water fittings) regulations 1999 Section G24.1 and G24.2.
Pipework Sizing:
In order to keep the noise of the system to a minimum, the velocity of water should be kept below
1.5 m/s and it should be noted that the appliance is designed to operate with a temperature differential of 20
o
C
between flow and return. The maximum flow rate is 0.3 kg/s which through a 22mm pipe gives a velocity of 1.00
m/s. Therefore, the recommended minimum pipe size for the main carcass is 22mm.
Water Treatment:
It is important that the system is cleansed and flushed thoroughly before the appliance is left to oper-
ate (as recommended in BS 7593) in order to maintain an efficiently operating heating system. Once the system has
been flushed, an inhibitor that is suitable for stainless steel heat exchangers should be added. Appropriate inhibitors are
available from both Sentinel and Fernox.
Note: Failure to carry out the above procedure will invalidate the guarantee!