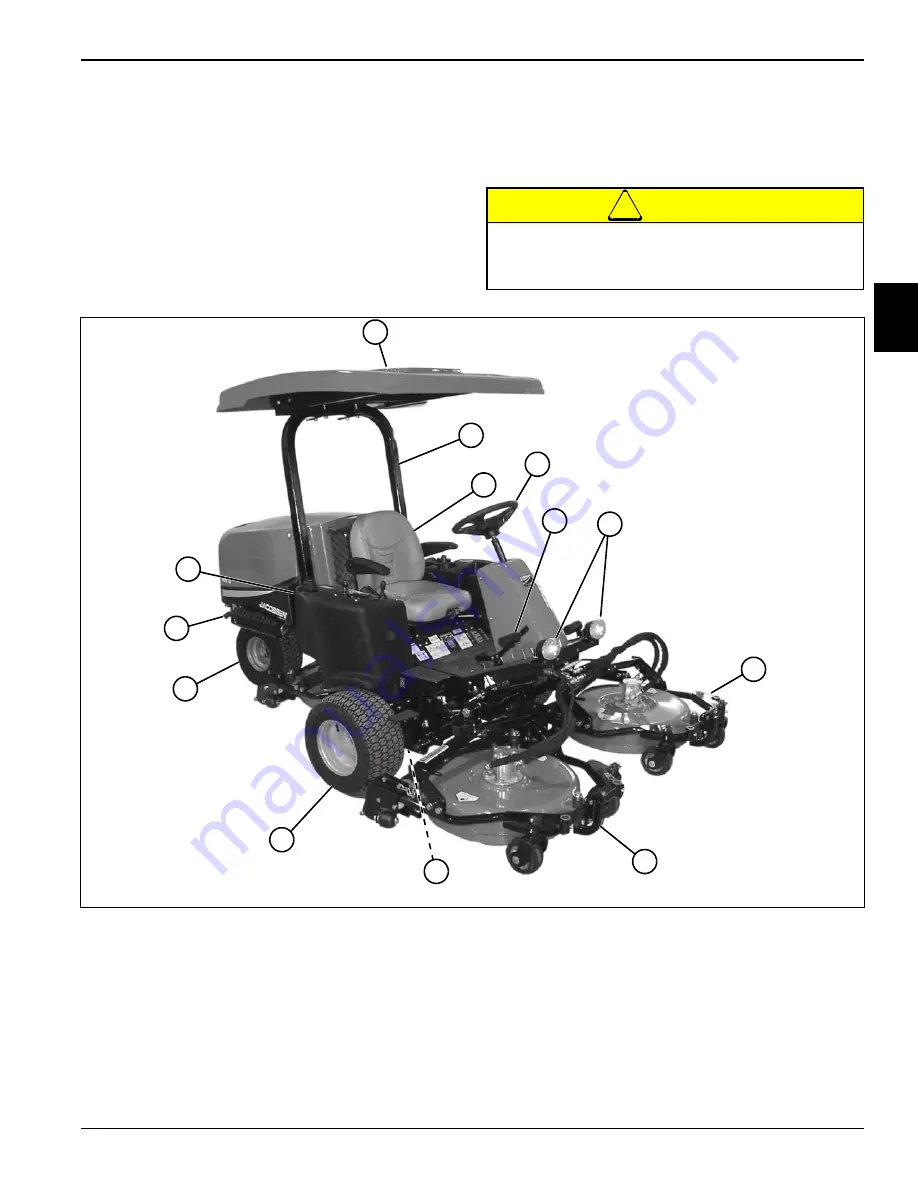
SPECIFICATIONS AND GENERAL INFORMATION
4181384 First Edition
2-3
2
If the machine requiring service is equipped with an
accessory kit, see Section 9, “Accessories and
Miscellaneous Repair” for removal, repair, and
installation procedures.
Component Location
AR-3
See Figures 2-3 and 2-4.
!
CAUTION
Figure 2-3: Component Location—Right Side
Become familiar with operator controls, machine
components, and correct operating procedures
before beginning repair procedures.
1
Canopy (Optional)
8
Right Front Cutting Unit
2
OPS (Optional)
9
Right Front Wheel Motor
3
Seat
10
Front Wheel (2)
4
Steering Wheel and Tower
11
Rear Wheel
5
Traction Pedal
12
Muffler
6
Work Lights (Optional)
13
Hydraulic Oil Tank
7
Left Front Cutting Unit
2
13
7
TN0991
1
8
11
6
3
5
10
4
12
9
Содержание AR3
Страница 1: ...AR 3 TR 3 Trim Mowers Technical Repair Manual AR30001 AR30002 TR30001 TR30002...
Страница 3: ......
Страница 7: ......
Страница 9: ...1 2 4181384 First Edition SAFETY 1 Page Intentionally Blank...
Страница 19: ...1 12 4181384 First Edition SAFETY 1...
Страница 33: ...2 14 4181384 First Edition SPECIFICATIONS AND GENERAL INFORMATION 2 Page Intentionally Blank...
Страница 73: ...4 16 4181384 First Edition ELECTRICAL 4 Page Intentionally Blank...
Страница 85: ...4 28 4181384 First Edition ELECTRICAL 4 Page Intentionally Blank...
Страница 147: ...4 90 4181384 First Edition ELECTRICAL 4 Page Intentionally Blank...
Страница 200: ...HYDRAULICS 4181384 First Edition 6 9 6 Page Intentionally Blank...
Страница 249: ...6 58 4181384 First Edition HYDRAULICS 6 Page Intentionally Blank...
Страница 251: ...7 2 4181384 First Edition STEERING 7 Page Intentionally Blank...
Страница 264: ...STEERING 4181384 First Edition 7 15 7 Page Intentionally Blank...
Страница 265: ...7 16 4181384 First Edition STEERING 7...
Страница 311: ...8 46 4181384 First Edition CUTTING UNITS 8 Page Intentionally Blank...
Страница 331: ...9 20 4181384 First Edition ACCESSORIES AND MISCELLANEOUS REPAIR 9 Page Intentionally Blank...
Страница 340: ......
Страница 342: ......