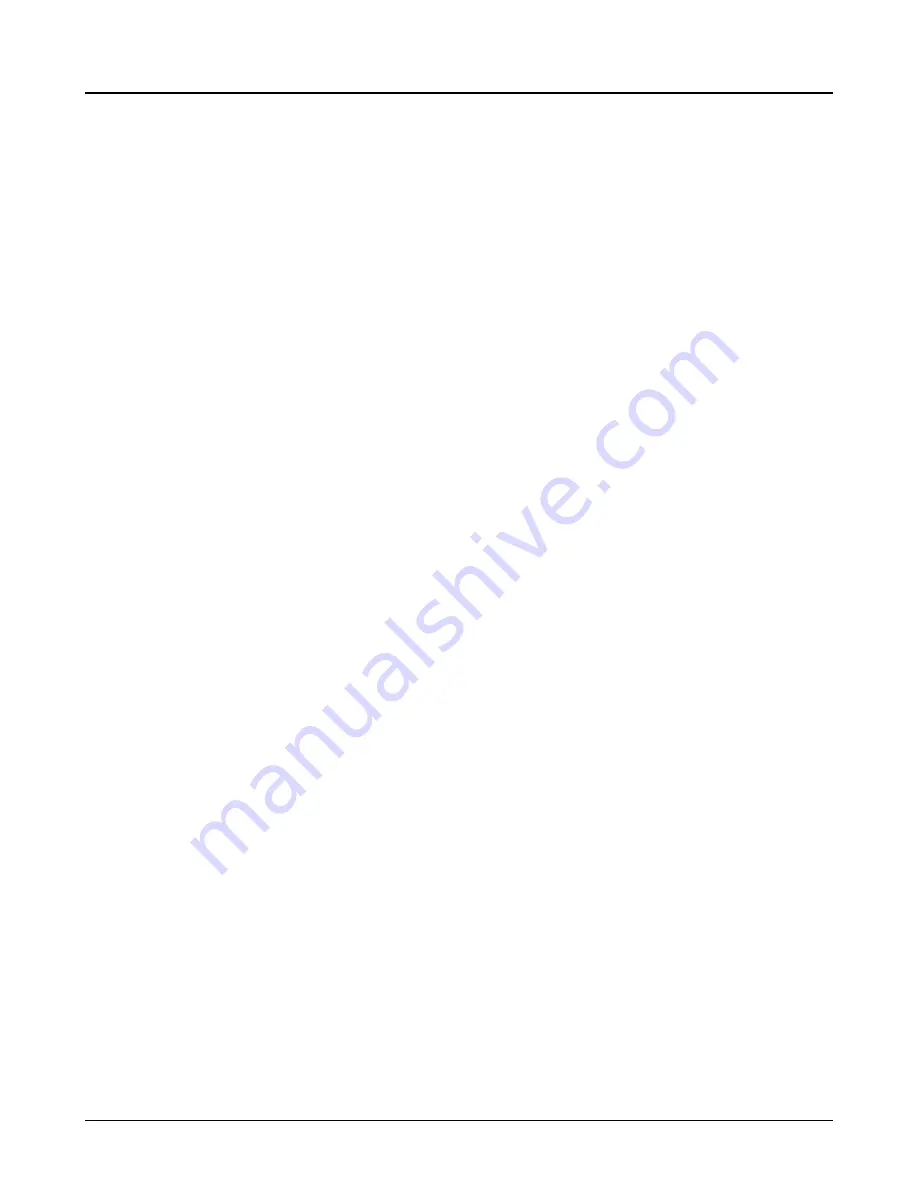
2.
Remove bearing cover (119), spacer sleeve (157) and thrower (248) or heat flinger (123B) if appli-
cable.
3.
Remove shaft sleeve key (401).
4.
Remove seal cover (184). Pre-treat fitting surface between the seal cover and the casing with com-
patible lubricant.
5.
Slide off shaft sleeve (104 and 126) and pull out O-ring (412F).
6.
Press out the seat ring of the mechanical seal (383 and 383S) from the seal cover (184) using even
pressure.
7.
Slide the rotating unit of the mechanical seal off the shaft sleeve (104 & 126). If the mechanical seal
has set screws these must first be removed.
8.
Clean and check all parts for wear. Mechanical seals must always be replaced.
6.5 Preassembly inspections
6.5.1 Replacement guidelines
Inspection
Clean and check the condition of all parts that have been removed. In case of doubt, replace compo-
nents. You must always replace wearing parts, such as ball bearings, and seals.
Mechanical seal location
Mechanical seals are located on the suction side for the (RS configuration and the discharge side for the
RS and ES configurations.
Shaft sleeve location
Shaft sleeves (104 and 126) and the mechanical seals (383S and 383) are separate components. Mark
the position of these parts so that you can mount them in the same position during reassembly.
6.6 Reassembly
6.6.1 Prepare for reassembly
1.
Clean all components and remove any rust.
2.
For the RS configuration, screw in and secure the throttling element (252) on the suction casing
(100F).
3.
For the RS configuration, provide a bore that is 0.16 in. (0.41 cm) in diameter in order to ventilate
the sealing chamber.
This bore must always be located in the top position. Depending on the location of the suction cas-
ing nozzle, use one of the three cast depressions for this drilled hole.
4.
Screw in the stud bolts (356A).
5.
ES? Screw in and secure the throttling element (252) (use correct bore) to the discharge casing
(100D).
6.
Screw in the stud bolts (356A).
7.
Hammer in the pin (445E) of the seal cover (184).
8.
Screw in the stud bolts (356C) on the bearing bracket (228C).
9.
Screw in the lubricating nipple (193B) of the bearing cover (119).
10. For the ES configuration, press in the bearing bushing (197A) of the intermediate bearing housing
(134C).
11. Clamp the shaft in a vertical position (122) using soft protective wedges. Make sure that the cou-
pling end points upwards.
6.5 Preassembly inspections
52
Model 3355 Installation, Operation, and Maintenance Manual
Содержание Goulds Pump 3355
Страница 1: ...Installation Operation and Maintenance Manual Model 3355 ...
Страница 2: ......