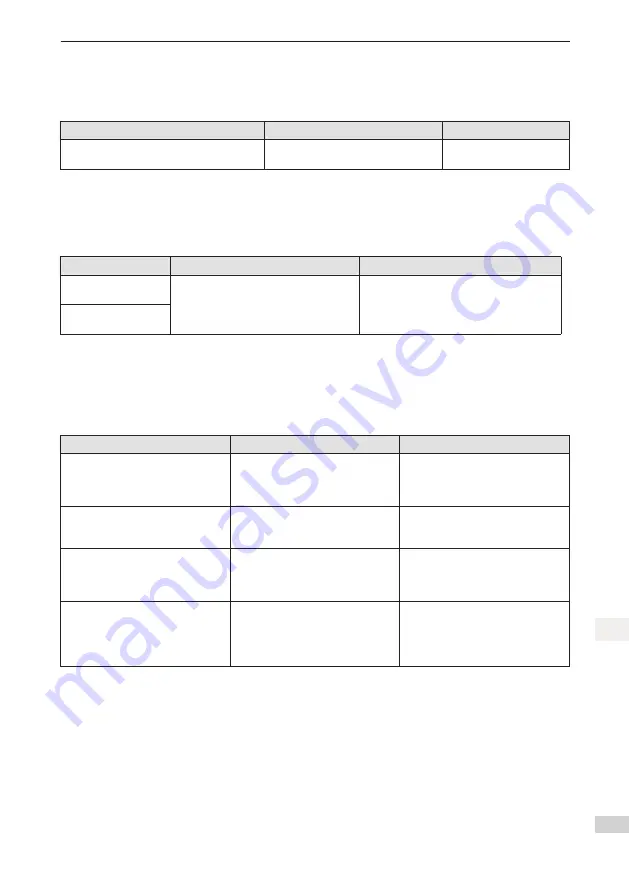
- 95 -
5 Troubleshooting
5
■
E3.107: communication loss of main processor
Cause:
Cyclic handshake communication between main processor and coprocessor is lost.
Probable Cause
Confirming Method
Corrective Action
Internal communication failure
The fault persists after the servo drive
is powered off and on several times.
Replace the servo drive.
■
E3.108: parameter storage fault
Cause:
Parameter values cannot be written to EEPROM.
Parameter values cannot be read from EEPROM.
Probable Cause
Confirming Method
Corrective Action
1. Parameter writing is
abnormal.
Modify a parameter, power on the servo
drive again and check whether the
modification is saved.
If the modification is not saved and the fault
persists after the servo drive is powered
off and on several times, replace the servo
drive.
2. Parameter reading
is abnormal.
■
E3.111: group 2000h/2001h parameter abnormal
Cause:
The total number of parameters changes, which generally occurs after software updates.
The actual parameter values of group 2000 or 2001 exceed the limit, which generally occurs after software
updates.
Probable Cause
Confirming Method
Corrective Action
1. Instantaneous power failure
occurs during parameter storage.
Check whether instantaneous power
failure occurs during parameter
storage.
Set drive model (2001-0Bh)
incorrectly, and power on the system,
then correctly set the drive model
and power on the system again.
2. Instantaneous power failure
occurs during serial encoder
motor parameter writing.
Check whether instantaneous power
failure occurs during serial encoder
motor parameter writing.
Write the parameters of serial
encoder motor by using Inovance
commissioning software.
3. The software is upgraded.
Check whether the software is
upgraded.
Set drive model (2001-0Bh)
incorrectly, and power on the system,
then correctly set the drive model
and power on the system again.
4. The servo drive is faulty.
If the fault persists after the servo
drive is powered off and on again,
and step 1 and 2 are repeated for
several times, it indicates that the
servo drive is faulty.
Replace the servo drive.
Содержание SV820N Series
Страница 127: ...126 6 Trial Running 6 6 5 6 PLC Program 1 Add an FB file that edits the function block in the application...
Страница 128: ...127 6 Trial Running 6 2 The definition part of FB 3 Five function blocks in FB...
Страница 141: ...140 6 Trial Running 6 In section0 call the function block then the axis can be moved by the bus...
Страница 143: ...142 6 Trial Running 6 3 Open Visual studio and create a New Twincat3 Project...
Страница 146: ...145 6 Trial Running 6 Click OK Click OK...
Страница 147: ...146 6 Trial Running 6 Click Yes Click OK...
Страница 149: ...148 6 Trial Running 6 C The default RPDO list is as follows...
Страница 150: ...149 6 Trial Running 6...
Страница 152: ...151 6 Trial Running 6 7 Activate the configuration and switch over to the running mode Click...
Страница 157: ...156 6 Trial Running 6 Add a motion control library making it easy to call the control function block...
Страница 158: ...157 6 Trial Running 6 Create a new POU...
Страница 159: ...158 6 Trial Running 6 Create a new FB add MC_power MC_jog MC_home MC_absolute MC_reset to FB...
Страница 160: ...159 6 Trial Running 6 Call axis_motion in main Call the program in PLCTASK...
Страница 161: ...160 6 Trial Running 6 Compile the program if there is no fault configuration can be activated and then log in to the PLC...
Страница 181: ...Revision History Date Revised Version Revised Details May 2017 A00 First release...