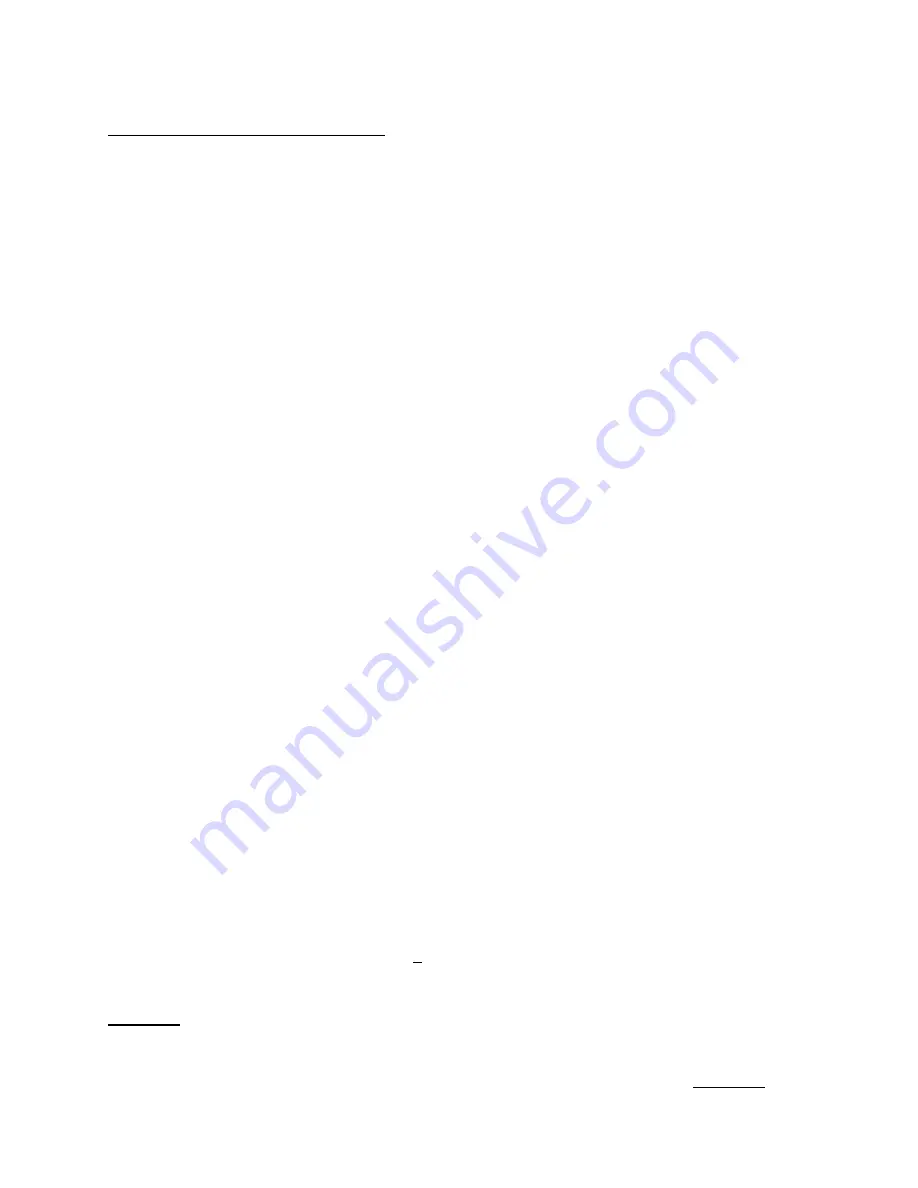
Setting Tolerances - cont.
11
For example, if I set the number to 2, IMPAX would allow 2 errors in a row but the 3rd error in a
row would cause the machine to stop. When tuning the IMPAX unit, it is often helpful to set a
large number of exceptions, say 10 or 15 and watch the force values in the Error/Exceptions
buffer. This can tell you what the values were for the exceptions and can give you information
needed to establish the proper settings for the tolerances.
Backstroke Exception Settings
Backstroke is only used for threadrolling applications. It is used to detect a part not being
properly ejected and remaining in the dies. It is always a high force error. If Backstroke Hi
Limit and Backstroke Exceptions are turned ON in Channel Definition, the display will show
“R1 BKSTR 00/100”. This function is always cumulative. You may put in a number between
1 and 99. Backstroke exceptions are rarely ever allowed but can be when there are problems
with a threadroller which causes nuisance shutdowns in the backstroke cycle, if all other causes
for backstroke noise have been eliminated.
No Feed Settings
No Feeds are cycles of the machines where no material is fed to the machine for processing.
Usually No Feeds are used with piece-fed machines like threadrollers, but under special
circumstances can be used with continuous or bar stock fed headers or other such applications.
No Feeds can be either Consecutive or Cumulative. If this feature is turned on in Channel
Definition, the display will show “R1 CONS NF 0000" or “R1 CUMU NF 0000." You can enter
a number between 1 and 9999. In a threadrolling application, this feature is extremely functional
since it will allow the machine to keep running even though the feed rail is not completely full or
does not feed a part every time
No Feed Exceptions
No Feed Exceptions is a special feature which will divert a certain number of parts immediately
after a No Feed condition. This may be used if, for example, there were several consecutive no
feeds and the dies cooled off. The first ten parts may not be as good quality as those produced
after the dies heated up. No Feed Exceptions could be set to eject these parts if they did not meet
the tolerance parameters. If this feature is activated in Channel Definition, the display will show
“R1 NOFEED EXCP.” You cannot enter anything on this display, it is just informing you that
No Feed Exceptions has been turned on. The next display is “ * 000 AFTER 000.” The number
entered here (0-999) is the number of “Fixed” cycles (when the Feed resumes) that the Special
Exceptions will be allowed. Enter a zero, 0, if you want the number of special exceptions to be
based on the amount of time the machine runs without feed. When the asterisk is in front of the
leftmost number, it means you can change that number. After you enter a number, press the
Enter/Yes key and the asterisk will move to in front of the rightmost number.
The number entered here (0-999) is the number of consecutive nofeeds which must be detected
before the Special Exceptions (for 15 cycles, in this case) will be allowed. Press Enter/Yes after
entering your number.
Содержание 2000
Страница 1: ...2000 Supervisor s Guide ...
Страница 4: ...Specifications Back view of Control Console Satellite Circuit IMPAX Control Console 49 50 51 52 ...
Страница 53: ...DRAWINGS Backview of the Control Console ...
Страница 54: ...Satellite Box Circuitry ...
Страница 55: ...IMPAX 2000 Control Console ...