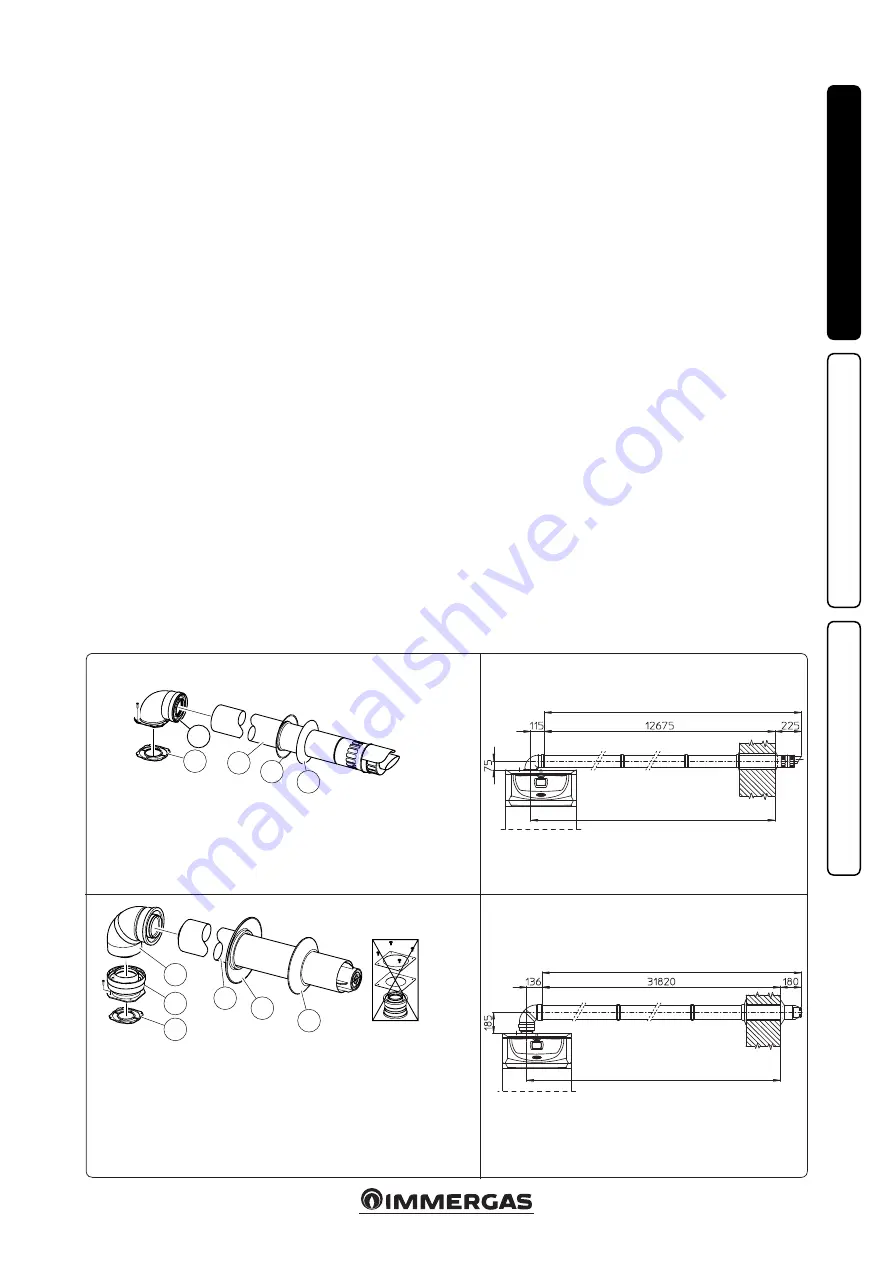
13
C
13
1-11
1-10
C
13
1-12
C
13
C
13
1-13
1
2
3
4
5
6
5
4
3
1
2
INS
TALLER
US
ER
MAINTEN
AN
CE TECHNI
CI
AN
1.11 CONCENTRIC HORIZONTAL KIT
INSTALLATION.
Type C configuration, sealed chamber and
fan assisted.
The position of the terminal (in terms of dis-
tances from openings, overlooking buildings,
floor, etc.) must be in compliance with the
regulations in force.
This terminal is connected directly to the outside
of the building for air intake and flue exhaust. The
horizontal kit can be installed with the rear, right
side, left side or front outlet. For installation with
frontal outlet, one must use the fixing plate and
a concentric bend coupling in order to ensure
sufficient space to carry out the tests required
by law upon commissioning.
• External grid. Both the Ø 60/100 and Ø 80/125
intake/exhaust terminal, if properly installed, is
pleasant to look at on the outside of the build-
ing. Make sure that the external silicone wall
sealing plate is properly inserted in the wall.
N.B.:
for proper system operation the terminal
with grid must be installed correctly ensuring
that, the "high" indication on the terminal is
observed during installation.
Horizontal intake-exhaust kit Ø 60/100
Kit
assembly (Fig. 1-10): install the bend with flange
(2) on the central hole of the boiler, positioning
gasket (1) with the circular projections down-
wards in contact with the boiler flange, and
tighten using the screws supplied with the kit. Fit
the Ø 60/100 (3) concentric terminal pipe with
the male side (smooth) to the female side of the
bend (2) up to the end stop; making sure that the
internal and external wall sealing plate have been
fitted, this will ensure sealing and joining of the
elements making up the kit.
• Extensions for Ø 60/100 horizontal kit (Fig.
1-11). The kit with this configuration can be
extended up to a
max. 12.9 horizontal m
in-
cluding the terminal with grid and excluding
the concentric bend leaving the boiler. This
configuration corresponds to a resistance factor
of 100. In this case the special extensions must
be requested.
Immergas also provides a Ø 60/100 simplified
terminal, which in combination with its exten-
sion kits allows you to reach a maximum exten-
sion of 11.9 metres.
Horizontal intake-exhaust kit Ø 80/125
Kit
assembly (Fig. 1-12): to install the kit Ø 80/125
one must use the flanged adapter kit in order
to install the flue system Ø 80/125. Install the
flanged adaptor (2) on the central hole of the
boiler, positioning gasket (1) with the circular
projections downwards in contact with the boiler
flange and tighten using the screws supplied with
the kit. Engage the bend (3) with the male side
(smooth) to the end stop on the adapter (1). Fit
the Ø 80/125 (5) concentric terminal pipe with
the male side (smooth) to the female side of the
bend (4) (with lip seals) up to the end top; making
sure that the internal (6) and external wall sealing
plate (7) have been fitted, this will ensure sealing
and joining of the elements making up the kit.
• Extensions for horizontal kit Ø 80/125 (Fig.
1-13). The kit with this configuration can be
extended up to a
max. length of 32 m
, includ-
ing the terminal with grid and excluding the
concentric bend leaving the boiler. If addi-
tional components are assembled, the length
equivalent to the maximum allowed must be
subtracted. In this case the special extensions
must be requested.
The adaptor kit includes:
N° 1 - Gasket (1)
N° 1 - Adaptor Ø 80/125 (2)
The Kit Ø 80/125 includes:
N° 1 - Concentric bend Ø 80/125 a 87° (3)
N° 1 - Int./exhaust concentric terminal Ø
80/125 (4)
N° 1 - Internal wall sealing plate (5)
N° 1 - External wall sealing plate (6)
The remaining kit components must not be used
The kit includes:
N° 1 - Gasket (1)
N° 1 - Concentric bend Ø 60/100 (2)
N° 1 - Int./exhaust concentric terminal Ø 60/100 (3)
N° 1 - Internal wall sealing plate (4)
N° 1 - External wall sealing plate (5)
Max 12900 mm
Max 32000 mm
Max 31956 mm
Max 12790 mm