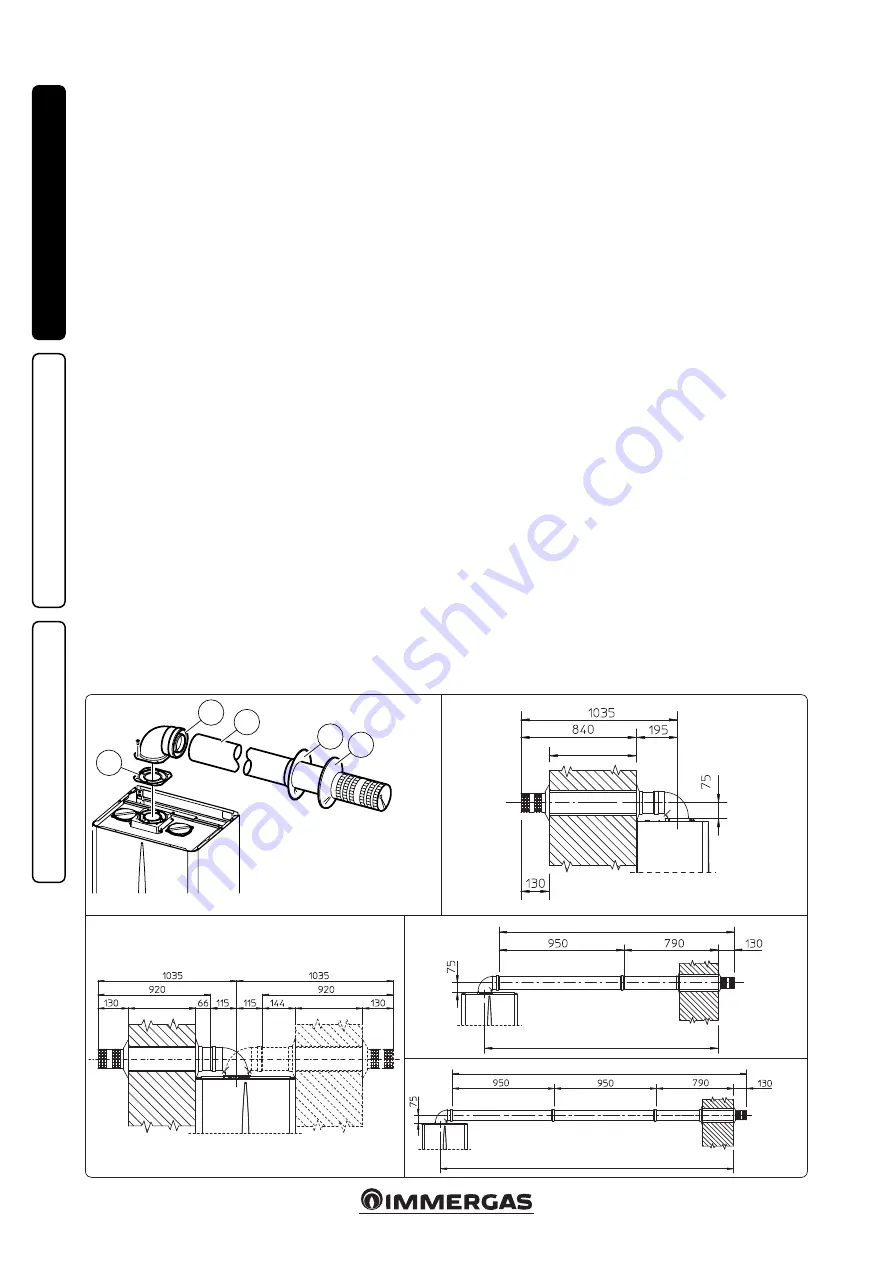
12
C
12
1-13
C
12
C
12
C
12
C
12
1-14
1-16
1-15
1
3
2
4 5
1-17
INS
TALLER
US
ER
MAINTEN
AN
CE TECHNI
CI
AN
1.11 INDOOR INSTALLATION.
• Type C configuration, sealed chamber and
fan assisted.
Horizontal intake-exhaust kit Ø 60/100
Kit
assembly (Fig. 1-13): install the bend with flange
(2) onto the central hole of the boiler inserting
the gasket (1) and tighten using the screws in-
cluded in the kit. Couple the terminal pipe (3)
with the male end (smooth) into the female end
of the bend (with lip seals) up to the stop; mak-
ing sure that the internal wall sealing plate and
external wall sealing plate have been fitted, this
will ensure sealing and joining of the elements
making up the kit.
• Coupling extension pipes and concentric
elbows Ø 60/100 To install any push-fit exten-
sions with other flue extraction elements, it
is necessary to do the following: install the
concentric pipe or elbow with the male side
(smooth) on the female section (with lip seal)
to the end stop on the previously installed ele-
ment. This will ensure the sealing and joining
of the elements correctly.
The Ø 60/100 horizontal intake/exhaust kit can
be installed with the outlet at the rear, right side,
left side and front.
• Application with rear outlet (Fig. 1-14). The
970 mm pipe length enables routing through
a maximum thickness of 710 mm. Normally
the terminal must be shortened. Calculate the
distance by adding the following values: Part
thi internal proj external
projection. The minimum indispensable pro-
jection values are given in the figure.
• Application with side outlet (Fig. 1-15); Using
the horizontal intake-exhaust kit, without the
special extensions, enables routing through
a wall thickness of 724 mm with the left side
outlet and 646 with the right side outlet.
NOTE:
when the boiler is installed in areas where
very cold temperatures can be reached, a special
anti-freeze kit is available that can be installed as
an alternative to the standard kit.
• Extensions for horizontal kit. The horizontal
intake-exhaust kit Ø 60/100 can be extended
up to a
max. horizontal distance of 3000 mm
including the terminal with grid and excluding
the concentric bend leaving the boiler. This
configuration corresponds to a resistance factor
of 100. In this case the special extensions must
be requested.
Connection with N°1 extension (Fig. 1-16).
Max. distance between vertical boiler axis and
external wall is 1855mm.
Connection with N°2 extensions (Fig. 1-17).
Max. distance between vertical boiler axis and
external wall is 2805mm.
Horizontal intake-exhaust kit Ø 80/125
Kit
assembly (Fig. 1-18): install the bend with flange
(2) onto the central hole of the boiler inserting
the gasket (1) and tighten using the screws in-
cluded in the kit. Fit the male end (smooth) of
the adapter (3) up to the end stop on the female
side of the bend (2) (with lip seal). Fit the Ø
80/125 (4) concentric terminal pipe with the male
end (smooth) to the female end of the adapter
(3) (with lip gasket) up to the end stop; making
sure that the internal and external wall sealing
plates have been fitted; this will ensure sealing
and joining of the elements making up the kit.
• Extension pipes and concentric elbows Ø
80/125 push-fitting gasket. To install any
push-fit extensions with other flue extraction
elements, it is necessary to do the following:
install the concentric pipe or elbow with the
male side (smooth) on the female section
(with lip seal) to the end stop on the previously
installed element. This will ensure the sealing
and joining of the elements correctly.
Attention:
if the exhaust terminal and/or con-
centric extension pipe needs shortening, consider
that the internal duct must always protrude by 5
mm with respect to the external duct.
Normally the Ø 80/125 horizontal intake-exhaust
kit is used if particularly long extensions are
required, the Ø 80/125 kit can be installed with
the outlet at the rear, right side, left side or front.
• Extensions for horizontal kit. The Ø 80/125
horizontal intake-exhaust kit can be extended
up to a
max. horizontal distance of 7,300 mm
including the terminal with grid and excluding
the concentric bend leaving the boiler and the
adapter Ø 60/100 in Ø 80/125 (Fig. . 1-19). This
configuration corresponds to a resistance factor
of 100. In this case the special extensions must
be requested.
N.B.:
when installing the pipes, a section clamp
with pin must be installed every 3 metres.
• External grid.
N.B.:
for safety purposes, do not
obstruct the boiler intake/exhaust terminal,
even temporarily.
Vertical kit with aluminium tile Ø 80/125.
Kit
assembly (Fig. 1-20): install the concentric flange
(2) on the central hole of the boiler inserting the
gasket (1) and tighten using the screws in the
kit. Fit the male end (smooth) of the adapter (3)
into the female end of the concentric flange (2).
Imitation aluminium tile installation. Replace the
tile with the aluminium sheet (5), shaping it to
ensure that rainwater runs off. Position the fixed
half-shell (7) and insert the intake-exhaust pipe
(6). Fit the Ø 80/125 concentric terminal pipe
with the male end (6) (smooth) to the female
The kit includes:
N°1 - Gasket (1)
N°1 - 90° concentric bend (2)
N°1 - Int./exhaust concentric pipe Ø 60/100
(3)
N°1 - Internal white wall sealing plate (4)
N°1 - External grey wall sealing plate (5)
Max 1870
Max 1855
Max 2820
Max 2805
MAX 724
MAX 646
MAX 710
Содержание 3.020928
Страница 1: ...MAIOR EOLO X 28 Instruction and recommendation booklet 1 038769ENG...
Страница 2: ......
Страница 30: ...30 3 5 6 6 7 8 8 f f e INSTALLER USER MAINTENANCE TECHNICIAN...
Страница 34: ......
Страница 35: ......