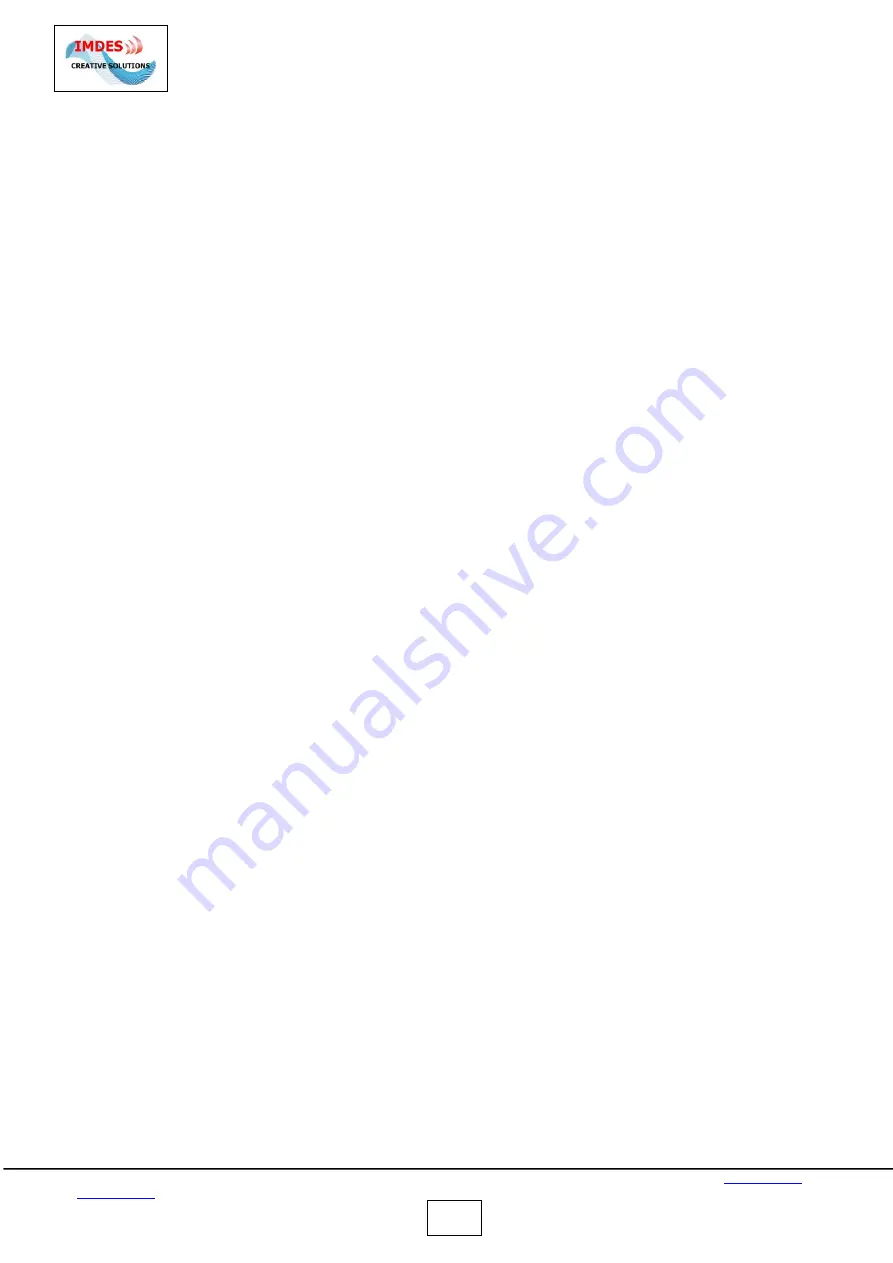
IMDES CREATIVE SOLUTIONS Schulstrasse 21 D-48455 Bad Bentheim /Gildehaus Germany T:+49(0)5924-997337 E:
© 2019
IMDES CREATIVE SOLUTIONS
24
3.1 Lead-free soldering
With conventional soldering technologies there are substantial problems when using lead-free solder alloys in the
production for lead-free SMD products. Although neither the handling nor the use of lead-free pastes is the actual
problem. Any bad wetting behavior may be counteracted by installing suitable inert gas equipment and by using
suitable fluxes. However, the components, potting compounds, printed circuit boards, plastics, etc., simply do not
meet any more the required conditions for a lead-free soldering process. All boundary parameters are infringed
upon, i.e. maximum temperature, time above liquids, maximum dwell times in the oven, etc. With convection
machines all the process limits have been reached. The air temperatures may not be increased further because this
would exceed the maximum temperatures and the temperature differences on the printed circuit board. Neither
may the machines be lengthened further as this would increase the times above flow point temperature and the
maximum dwell times. Even an increase in the speed of the air-flow is out of question as this will displace the
components. Thus, in mass production one may be forced – if one maintains the present soldering technology, to
tailor any critical materials to the process. However, from today’s point of view this results in enormous
complications and overhead. Contrary to the costs of the pastes, which represent only a fraction of the costs of the
assembly – a doubling of the costs of the components increases the actual production costs enormously. This,
consequently, will create a substantial problem in earning capacity. It is here where the vapor-phase - as the only
soldering system - offers the inestimable advantage to continue using all hereto known and processed materials.
The costs of the machines are comparable and in some cases even lower than those of well-known convection
systems. Therefore, the vapor-phase offers enormous competitive advantages in the production of lead-free
products.
Profile of paste containing lead. 200 °C end temperature
Profile of paste without lead. 230 °C end temperatur
e
3.2 Void-free soldering
A critical property of solder-joints - from certain sizes onwards, is to form voids, which may lead to functional
problems and questions as to their durability. E.g. the solder-joints of high-capacity processors may not dissipate
their waste-heat correctly any more. Often only a fraction of the capacity of high capacity thyristors may be used.
Yet, the trend continues towards even higher integrated circuits with power components on the printed circuit
boards. All this requires furthering reducing the formation of voids. The vapor-phase process offers inestimable
possibilities to reduce drastically the formation of voids. Studies have verified that assemblies, which have been
processed in a vapor-phase system, produce only a fraction of voids -compared to infrared or convection processed
boards. The reason for the small amount of voids is the absolutely oxygen-free vapor-phase soldering process. As
soon as there is an oxide film on the molten alloy, it is like a skin which inhibits the escape of the voids out of to
the solder-joint. This void behavior is problematic and particularly so with lead-free soldering. Due to the bad
wetting of the pastes the voids are not able to escape the soldering alloy. However, when soldering in a vapor-
phase system voids the behavior that corresponds to that of convection soldering with lead containing pastes.
Generally, lead-free pastes are inclined to produce very high amounts of voids in standard convection machines.