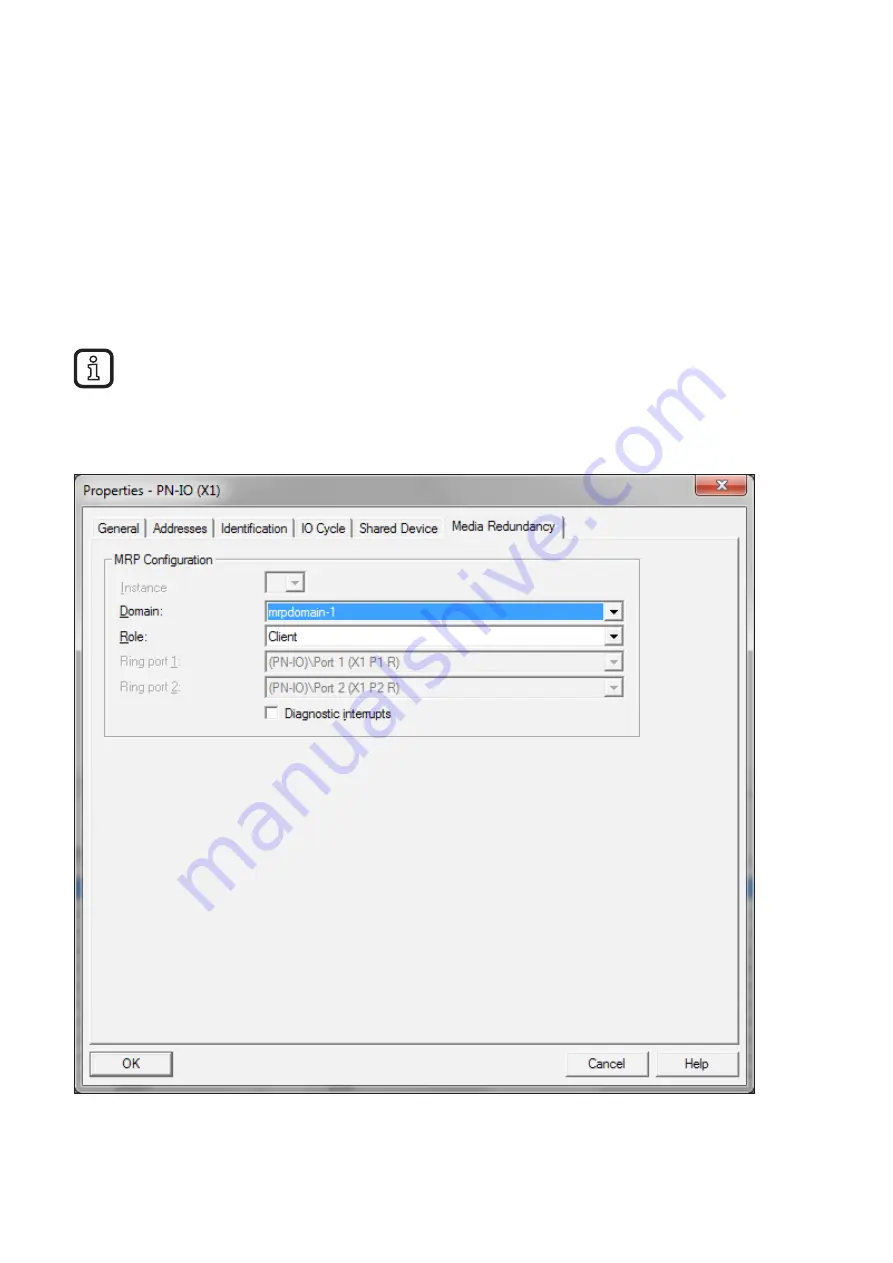
IO-Link master
56
35.7 Media Redundancy Protocol
In order to configure the Media Redundancy Protocol (MRP), the ring must be set
for the corresponding dialogue boxes of the Profinet interfaces�
The following steps must be carried out
Right-click on [Profinet IO Interface (PN-IO)], then select [Object Properties]�
► In the [Media Redundancy] tab, select the value [Client] under [Role]�
► Close the dialogue with [OK]�
► The corresponding settings must be made for the MRP manager�
► If an S7 controller with two Ethernet ports is used and auto negotiation is also deactivated, the
second port must be set exactly like the first port� A crossed patch cable must therefore be used
to establish a connection from the second port of the controller to the second port of a Profinet
device�
Содержание ECOMAT 300 AL1000
Страница 1: ...Device manual IO Link master ProfiNet AL1000 7391030 00 02 2016 UK ...
Страница 59: ...UK IO Link master 59 ...
Страница 61: ...UK IO Link master 61 ...