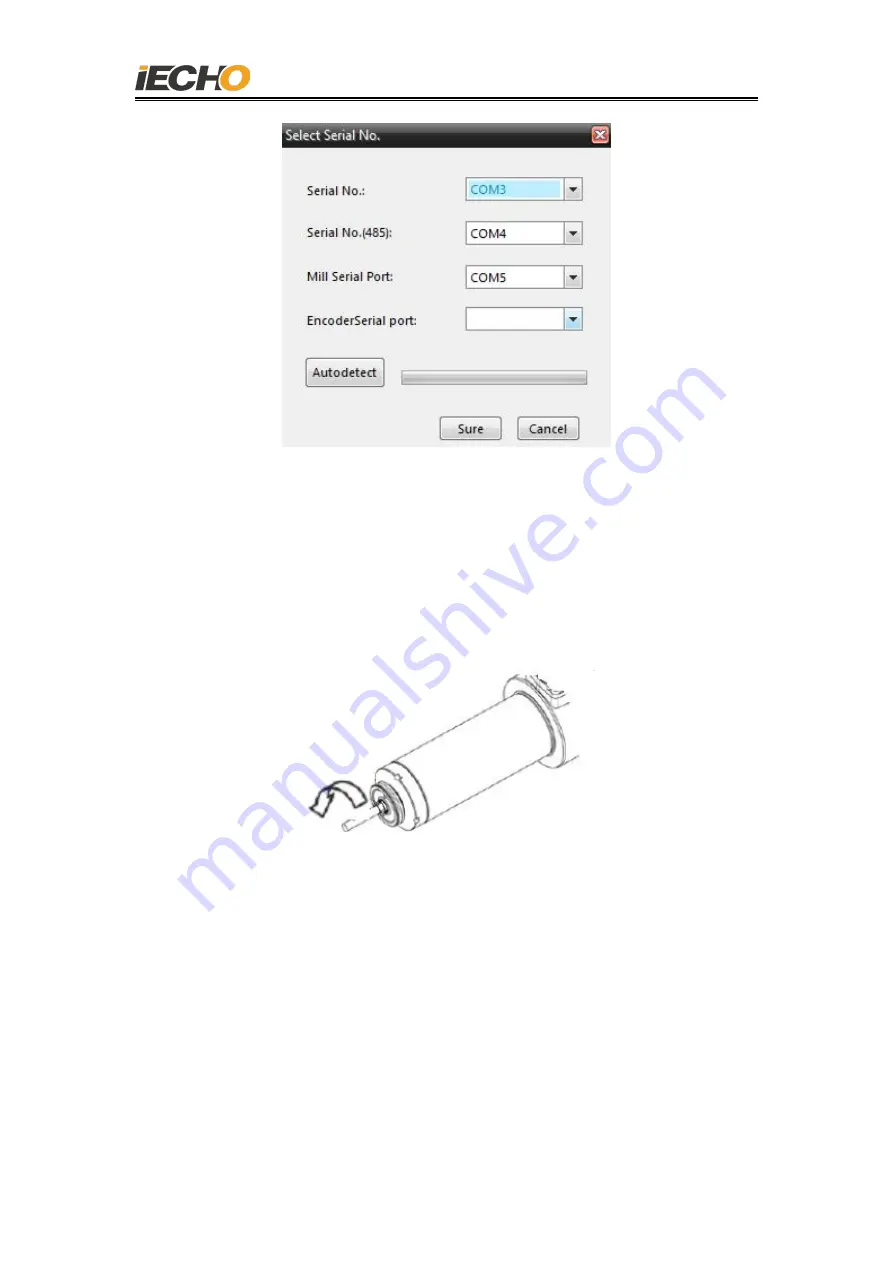
Hangzhou IECHO Science & Technology Co., Ltd.
13
(
Figure. 18
)
6.4. Confirm spindle rotation direction
When first time using, please make sure whether the spindle direction is correct
(as shown in the figure). If it is not correct, please check if the cable connected
properly. The software can not change the rotation direction setting.
(
Figure. 19
)
7.The use of router
450W Router software version requirements:
DSP program version: DSP2.2.8-6A180903M and above
CutterServer software version: V4 (2019.9.4.511) and above
iBrightCut software version: V4 (2020.4.3.2373) and above
Router rotation direction