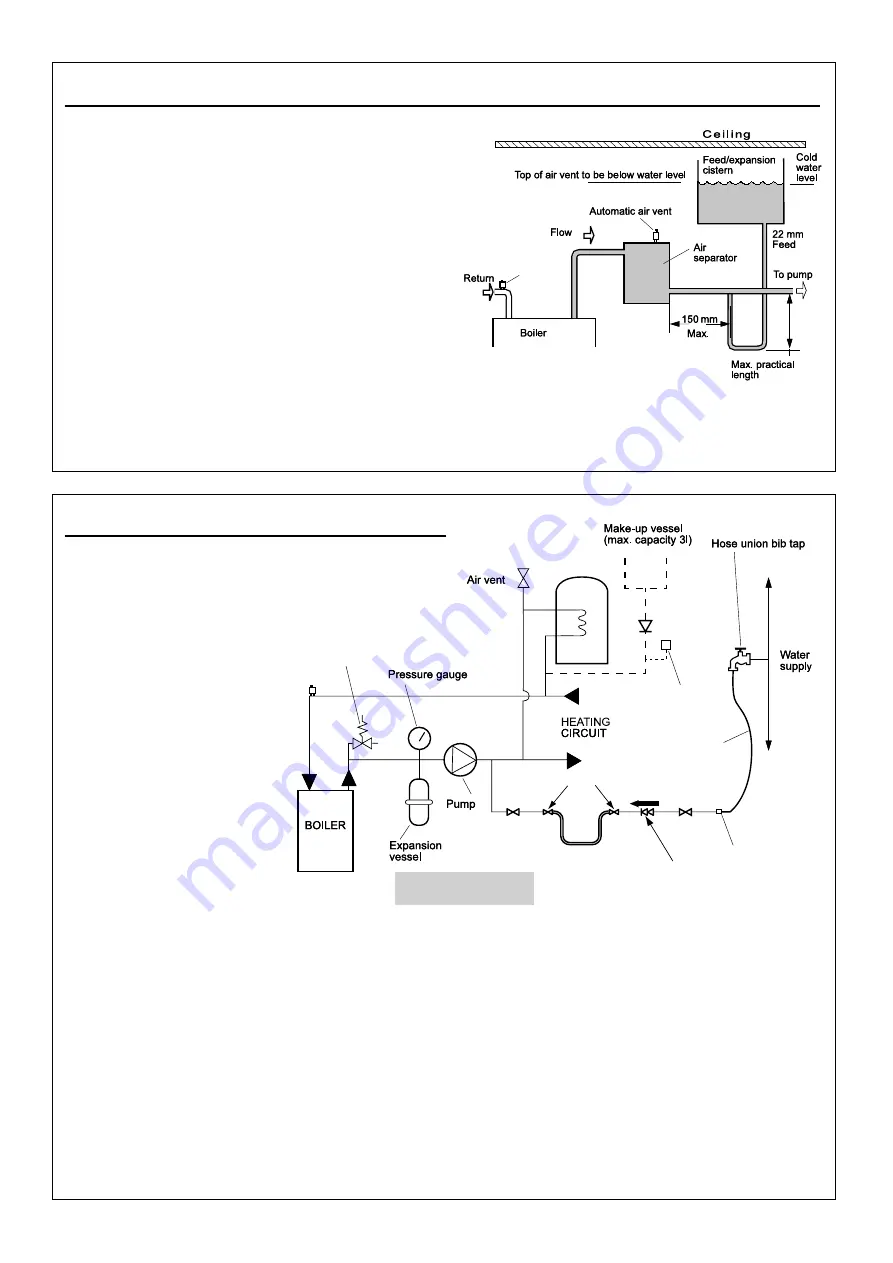
13
Installation and Servicing
Section 1 - General
1.17 LOW HEAD AND LARGE SYSTEMS WITH EXTENSIVE PIPE RUNS - OPEN VENT
Note.
The pump manufacturers’ minimum requirements
must be complied with.
All dimensions in mm
205862-10060
Auto
Air
Vent
This arrangement is useful for large systems where
radiators at the extremities are difficult to vent. This can
lead to pumping over with conventional feed and vent
arrangements.
The following conditions MUST be observed:
1. The top of the automatic air vent must be below the cold
water level.
2. The static water level (cold) must be at least 200mm
above the top of the horizontal flow pipe, fitted as shown.
The vent connection MUST NOT be made immediately
off the top of the boiler as venting is made less efficient.
3. The maximum practical length of 22mm cold feed pipe
should be used in order to reduce the effective volume
of hot system water expanding into the feed/expansion
cistern to a minimum.
1.18
SEALED
SYSTEM REQUIREMENTS
Non-return
valve
Automatic
air vent
Hose unions
Additional
stop valve
Hose connector
Hosepipe
(disconnect
after filling)
Double check valve
assembly
(
note direction of flow)
Temporary hose
(disconnect
after filling)
Auto
Air
Vent
Note.
A drain cock is
provided within the boiler
PRV
2. PRV
A pressure relief valve (PRV) complying with the relevant
requirements of BS.6759 must be fitted in the flow pipe
as close to the boiler as possible and with no intervening
valve or restriction. The valve should have the following
features:
a. A non-adjustable preset lift pressure not exceeding
3bar.
b. A manual testing device.
c. Provision for connection of a discharge pipe.
The valve or discharge pipe should be positioned
so that the discharge of water or steam cannot
create a hazard to the occupants of the premises or
cause damage to electrical components and wiring.
Notes.
a. The method of filling, refilling, topping up or flushing
sealed primary hot water circuit from the mains via a
temporary hose connection is only allowed
if acceptable to the local
water authority.
b. When installing the filling
device, it must be connected
as shown to fully comply
with the water regulations.
This may involve the fitting of
an additional WRAS approval
isolator valve to the mains
supply.
1. General
a. The installation must comply with the requirements
of BS. 6798, BS. EN 12831 and BS. EN 14336.
b. The installation should be designed to work with flow
temperatures of up to 80
o
C.
c. All components of the system, including the heat
exchanger of the indirect cylinder, must be suitable
for a working pressure of 3 bar and a maximum
temperature of 110
o
C. Care should be taken in
making all connections so that the risk of leakage is
minimised.
Содержание LOGIC HEAT2 H12
Страница 56: ...56 Installation and Servicing Section 6 Benchmark to Commissioning ...
Страница 62: ...62 Notes Installation and Servicing ...
Страница 63: ...63 Notes Installation and Servicing ...