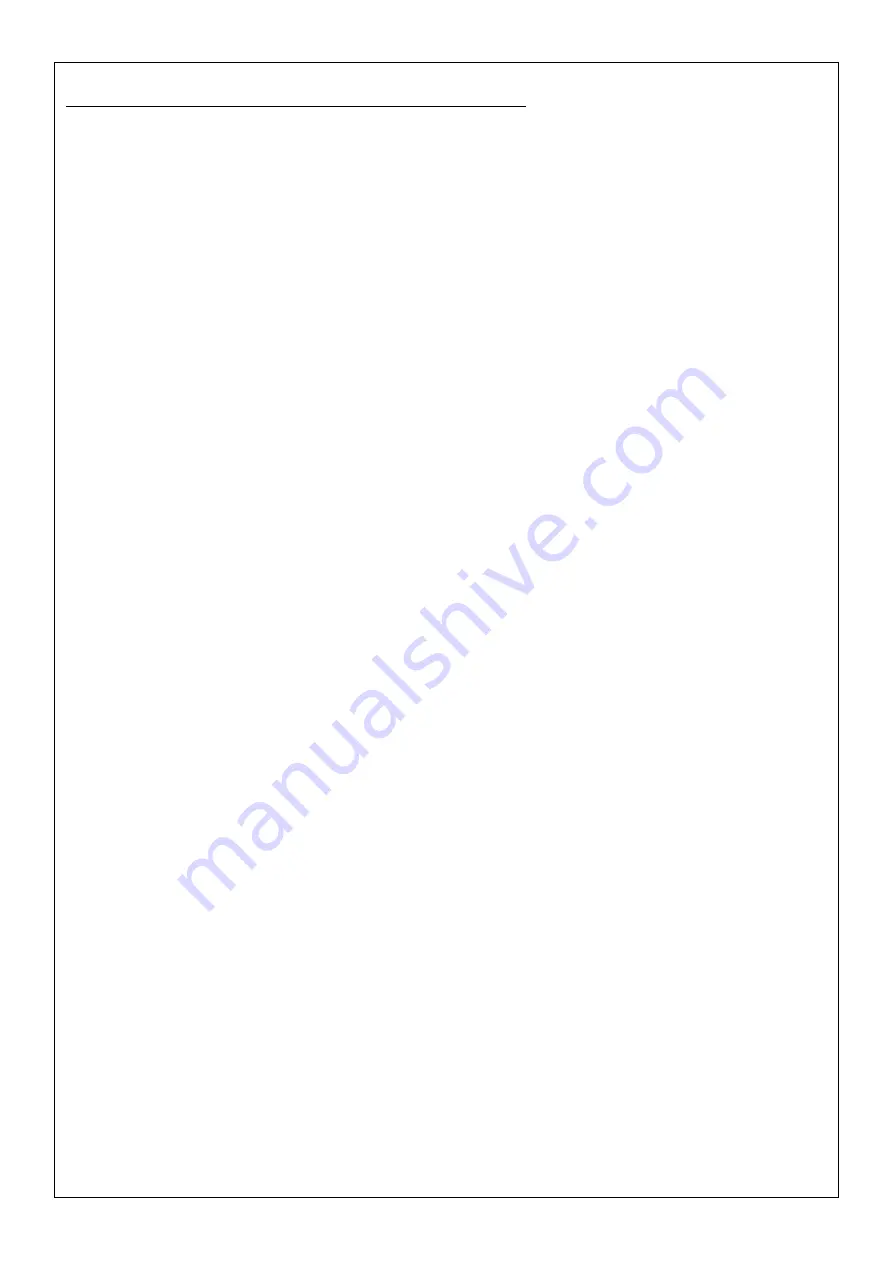
14
Installation and Servicing
Section 1 - General
3. Pressure Gauge
A pressure gauge covering at least the range 0-4 bar
must be fitted to the system. The gauge should be
easily seen from the filling point and should preferably be
connected at the same point as the expansion vessel.
4. Expansion Vessel
a. A diaphragm type expansion vessel must be
connected to a point close to the inlet side of the
pump, the connecting pipe being not less than 15 mm
size and not incorporating valves of any sort.
b. The vessel capacity must be adequate to accept the
expansion of the system water when heated to 110
o
C.
c. The charge pressure must not be less than the static
water head above the vessel. The pressure attained
in the system when heated to 110
o
C should be at
least 0.35 bar less than the lift pressure of the safety
valve.
For guidance on vessel sizing refer to the table in
this section.
For further details refer to BS. 5449, BS. 7074:1 and
the British Gas Corporation publication ‘Material
and Installation Specifications for Domestic Central
Heating and Hot Water’. For IE refer to the current
edition of I.S.813.
5. Cylinder
The cylinder must be either of the indirect coil type or a
direct cylinder fitted with an immersion calorifier which is
suitable for operating on a gauge pressure of 0.35 bar
in excess of the PRV setting. Single feed indirect
cylinders are not suitable for sealed systems.
6. Make-up Water
Provision must be made for replacing water loss from the
system, either:
a. From a manually filled make-up vessel with a readily
visible water level. The vessel should be mounted at
least 150 mm above the highest point of the system,
and be connected through a non-return valve to the
system, fitted at least 300 mm below the make-up
vessel on the return side of the domestic hot water
cylinder or radiators.
or
b. Where access to a make-up vessel would be difficult
by pre-pressurisation of the system. Refer to ‘Filling’.
7. Mains Connection
There must be no direct connection to the mains water
supply or to the water storage tank supplying domestic
water, even through a non-return valve, without the
approval of the local water authority.
1.19 SEALED SYSTEM REQUIREMENTS - CONT.
8. Filling
The system may be filled by one of the following
methods:
a. Through a cistern, used for no other purposes, via a
ball valve permanently connected directly to a service
pipe and/or a cold water distributing pipe.
The static head available from the cistern should be
adequate to provide the desired initial system design
pressure.
The cold feed pipe from the cistern should include a
non-return valve and a stop valve with an automatic
air vent connected between them, the stop valve
being located between the system and the automatic
air vent. The stop valve may remain open during
normal operation of the system if automatic water
make-up is required.
b. Through a self-contained unit comprising a cistern,
pressure booster pump (if required) and, if necessary,
an automatic pressure reducing valve and flow
restrictor. The cistern should be supplied through a
temporary connection from a service pipe or cold
water distributing pipe.
This unit may remain permanently connected to
the heating system to provide limited automatic
water make-up. Where the temporary connection is
supplied from a service pipe or distributing pipe which
also supplies other draw-off points at a lower level
then a double check valve shall be installed upstream
of the draw-off point.
c. Through a temporary hose connection from a draw-
off tap supplied from a service pipe under mains
pressure. Where the mains pressure is excessive a
pressure reducing valve shall be used to facilitate
filling.
The following fittings shall form a permanent part of
the system and shall be fitted in the order stated:
A stop valve complying with the requirements of
BS. 1010, Part 2 (the hose from the draw-off tap shall
be connected to this fitting).
A test cock.
A double check valve of an approved type.
• Thoroughly flush out the whole of the system with
cold water, without the pump in position.
• With the pump fitted, fill and vent the system until
the pressure gauge registers 1.5 bar. Examine for
leaks.
• Check the operation of the PRV by manually
raising the water pressure until the valve lifts.
This should occur within ± 0.3 bar of the preset lift
pressure.
• Release water from the system until the initial
system design pressure is reached.
• Light the boiler and heat the system to the
maximum working temperature. Examine for leaks.
• Turn off the boiler and drain the system while still
hot.
• Refill and vent the system.
• Adjust the initial pressure to the required value.
Содержание LOGIC HEAT2 H12
Страница 56: ...56 Installation and Servicing Section 6 Benchmark to Commissioning ...
Страница 62: ...62 Notes Installation and Servicing ...
Страница 63: ...63 Notes Installation and Servicing ...