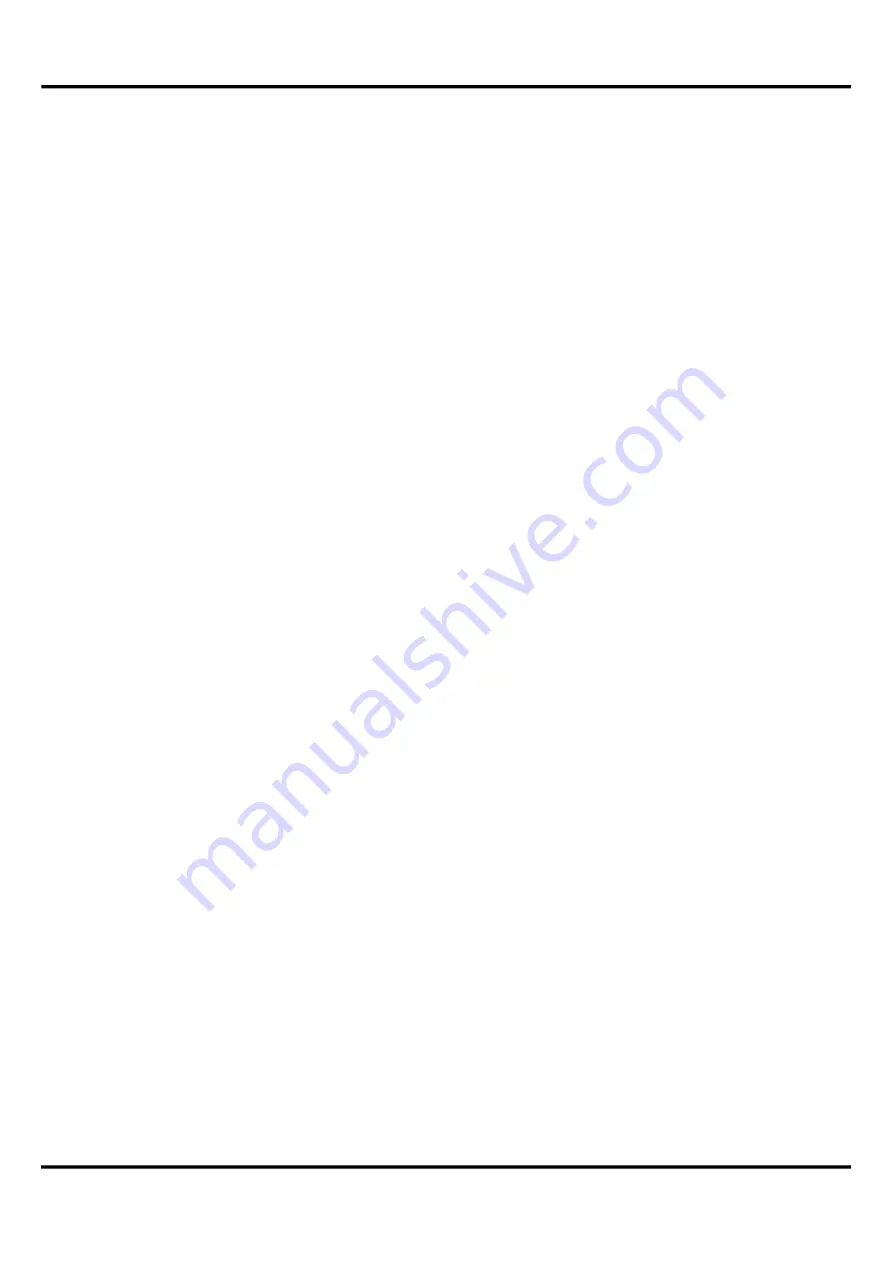
8. Program number description
The
IPM5
and
IPW5
devices are parameterised or preset via program numbers because of the
many different settings.
Strain gauges PN0
With this program number, the sensitivity
of the strain gauge can be selected.
PN0
=
0,
1,
5,
6
With
these
settings,
the
maximum
amplification
(as
with
PN0=10)
is
preselected
so
that
the
output
ranges
of
all
possible
sensor
types
can
be
recorded
and
evaluated.
PN0
=
2,
3,
4
This
setting
is
based
on
pre-calibrated
sensors,
so
that
the
start
and
end
value
are
generally
fixed.
With
a
change
to
PN1
or
PN2,
the
relevant
binary
calibration
point
is
set
to
the
factory
setting.
Should
a
calibration
be
subsequently
performed,
the
calibration
points
will
be
checked
for
plausibility.
PN0
=
7,
8,
9,
10
With
this
setting,
the
calibration
points
are
not
fixed.
When
programming
PN1
and
PN2,
the
momentary
measurement
is
taken
from
the
input.
PN1
and
PN2
must
be
at
least
1%
of
the
measuring
range
apart.
When
programming
PN1,
the
CAL
wire
(calibration
point)
is
switched
2
seconds
before
taking
over
the
measurement,
and
the
set
calibration
point
offset
against
the
momentary
binary
value.
Setting
of
final
value
PN1
The
end
value
for
the
display
value
and
measurement
may
be
larger
or
smaller
than
the
offset
setting
PN2.
It
must
differ
from
its
measured
value
by
at
least
1%
of
the
measuring
range
of
the
programmed
offset
value
in
PN2.
If
a
standard
sensor
has
been
selected
(PN0
=
2,
3
or
4),
the
measuring
value
determined
ex
works,
1mV/V,
2mV/V
or
3.3mV/V,
is
entered.
If
PN0
is
set
at
7,
8,
9
or
10,
the
display
switches
–
if
available
–
its
CAL
wire,
waits
for
2
seconds
and
then
takes
over
the
preset
calibration
points
based
on
the
set
calibration
point
PN10.
Offset
setting
PN2
With
the
offset
setting
PN2,
the
measured
value
must
differ
by
at
least
1%
from
the
end
value
of
PN1
calculated
on
the
measuring
range.
If
PN0
is
selected
at
=
2,
3
or
4,
the
0mV/V
valued
determined
ex
works
is
taken
as
the
measurement
in
PN2.
If
PN0
is
selected
at
=
7,
8,
9
or
10,
the
currently
set
measurement
is
taken
as
the
calibration
point.
Setting
of
decimal
point
PN3
With
this
program
number,
the
desired
number
of
places
after
the
decimal
point
can
be
defined.
The
displayed
decimal
point
moves
from
left
to
right
or
vice
versa,
with
the
value
0
being
taken
as
a
basis.
Offset
displacement
PN4
In
this
program
number,
the
currently
effective
offset
value
can
be
checked.
It
can
also
be
changed
in
this
program
number.
With
a
transient
taring
operation
(PN6
=
2,
3
or
5),
the
tare
value
is
lost
when
restarting
the
unit,
otherwise
the
value
can
be
found
in
the
provided
configuration
memory
for
the
program
number.
22
8. Program number description