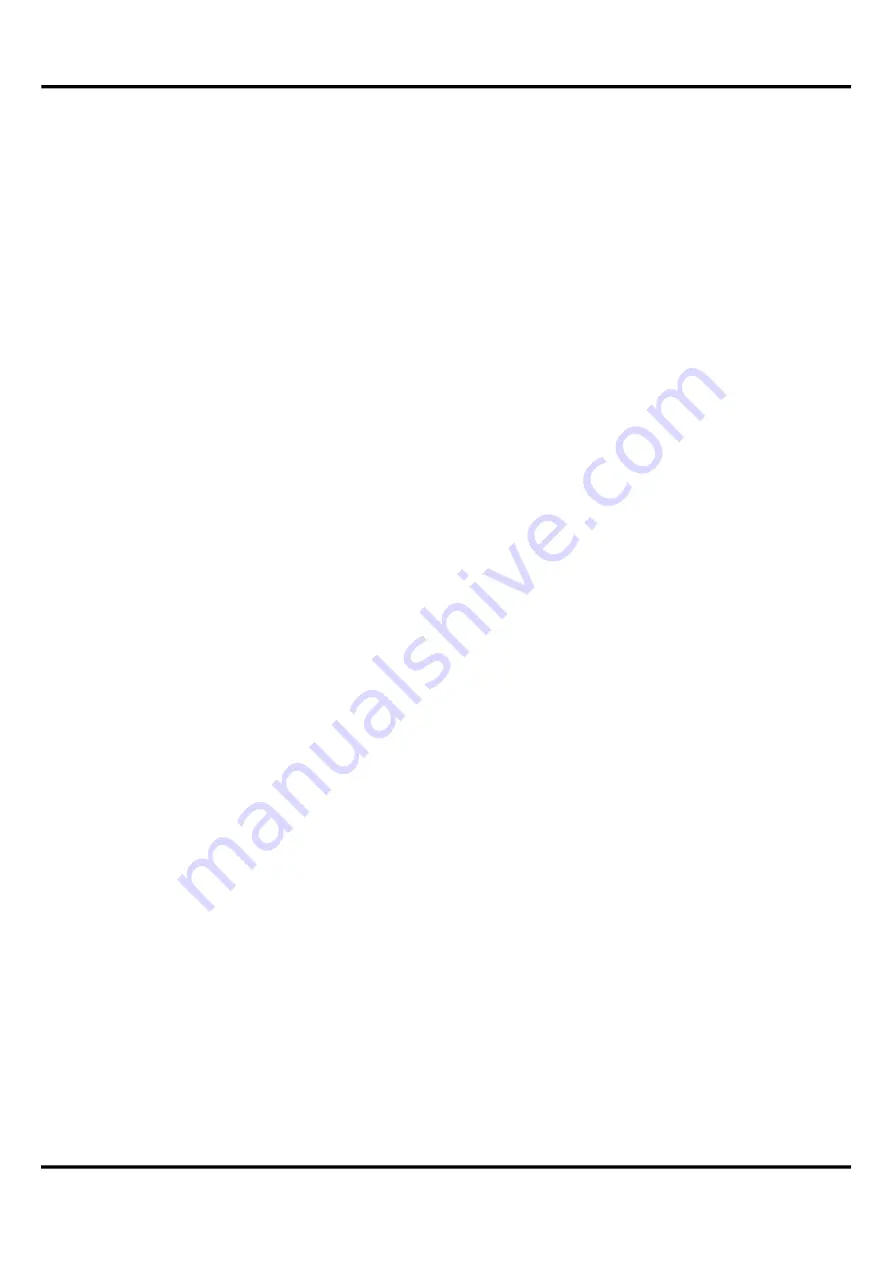
14
6. Operation and function decription
6.4.3
IPM5
calibration of mass pressure sensors
Many
standard
sensors
for
mass
pressure
measurement
have
a
special
CAL
wire.
If
this
is
connected
to
DMS-minus
(Strain
gauge
minus)
,
an
unloaded
bridge
becomes
so
unbalanced
that
the
signal
value
corresponds
to
an
80%
load
(80%
is
a
standard
value
that
can,
however,
be
changed
for
the
display).
In
addition,
the
display
has
its
own
CAL
terminal
on
which
the
signal
wire
can
be
laid.
If
a
calibration
is
triggered,
at
first
the
unit
automatically
performs
a
zero
balance
and
then
a
load
balance.
The
latter
is
achieved
by
the
display
switching
the
CAL
wire
via
a
relay
contact
against
supply,
and
then
evaluating
the
signal
value
as
an
80%
load.
This
measurement
is
used
for
the
linearisation.
6.4.4 Sensitivity recognition
The
units
support
a
sensitivity
recognition,
which
can
automatically
distinguish
between
1mV/V,
2mV/V
and
3.3mV/V
sensors.
For
this,
a
calibration
point
>0.00%
must
be
selected.
With
the
aid
of
the
offset
voltage
and
CAL
voltage,
the
display
can
recognise
whether
it
is
a
1mV/V,
2mV/V
or
3.3mV/V
sensor
and
then
adjusts
the
PN0.
In
the
second
run,
the
calibration
is
carried
out
in
the
relevant
measuring
zone.
The
procedure
is
as
follows:
Sensitivity
recognition
⇒
Display of "SEnS" for the entire process.
⇒
Amplification of the measuring input is set to 1.
⇒
Offset voltage is measured.
⇒
CAL relay is switched.
In semi-automatic mode, the procedure is as follows:
⇒
Display of "Sen2" flashing
⇒
until
[P] key
or release is activated
⇒
CAL voltage is measured.
⇒
The calibration relay is switched off.
⇒
Display of “FInd1” with 1mV/V etc.
⇒
1 second
If the sensor recognition has not identified an overflow and the sensor was able to allocate a
1mV/V-
(=FInd1), 2mV/V- (=FInd2) or 3.3mV/V- (=FInd3) bridge
otherwise
⇒
display of an error message
⇒
2 seconds
Error messages after sensitivity recognition (priority from 1 to 5)
•
"SErr1" if no offset was recognised.
•
"SErr2" when the end value for CAL is outside the permitted range.
•
"SErr3" if the end value has not changed under CAL by min. 1% of measuring range
•
"SErr4" when PN0 is set to 2, 3, 4 and the error is 10% higher than expected.
•
"SErr5" when, in semi-automatic mode, 60 seconds has elapsed.
With an error message, no changeover of PN0 is made, otherwise, if PN0 is preset to 0 or 1, the
value is changed to 2, 3 or 4. If PN0 is preset to 5 or 6, the most suitable amplification setting
(PN0=7, 8 or 9) is set so that a resolution of around 120% of the end value can be ensured.