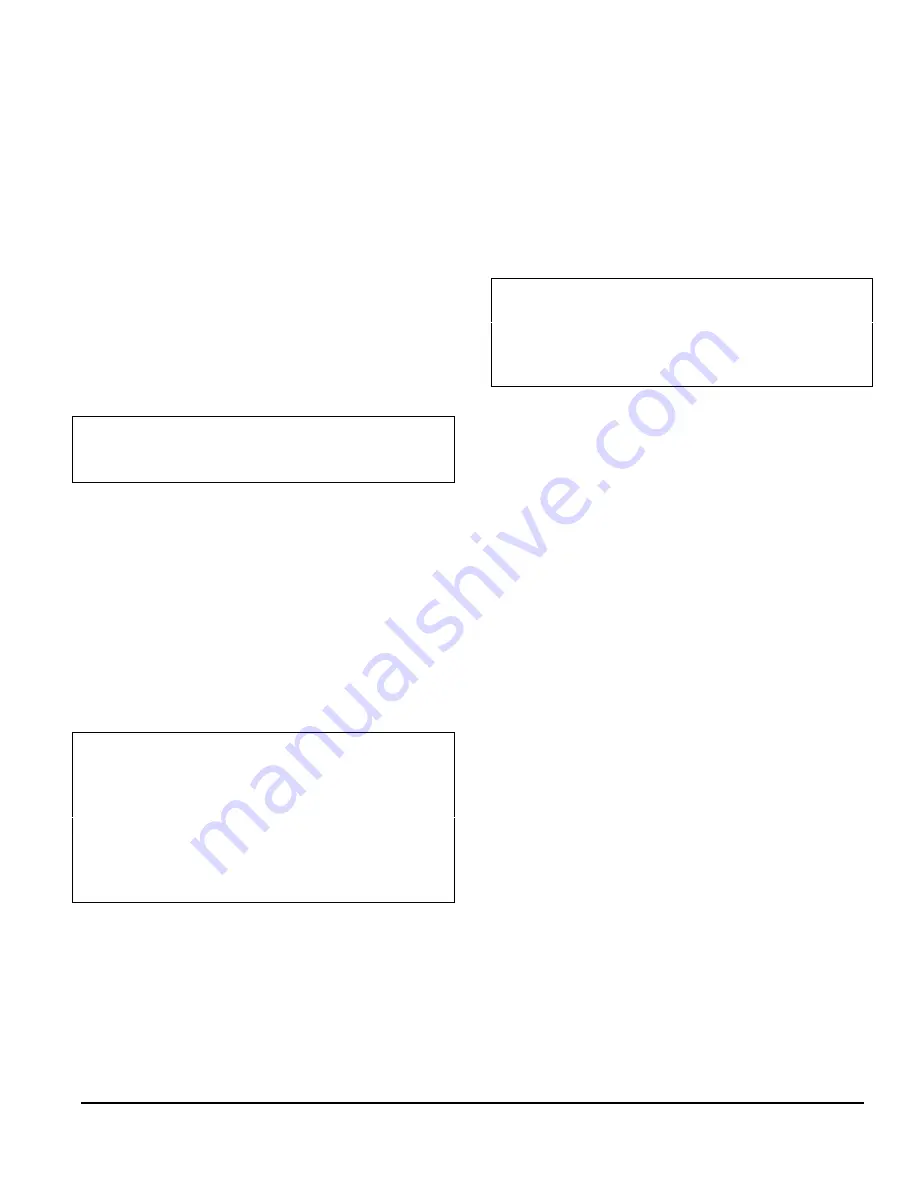
24
find that a 36” long flexible hose attachment will be
helpful to reach into the back of the radiator; a piece of
1/2” flexible gas connector, or a piece of 1/2” liquid-tight
vinyl jacket metallic electrical conduit works well as a
makeshift device.
Cleaning the heat exchanger:
Remove the 4-bolt flange from the front of the furnace
to reveal the clean-out port and check for soot deposits.
If there is very little soot in the radiator section visible
from the clean-out port, you will not need to clean it.
However, if you notice scaling in the radiator, you
should remove the scale.
The wrap-around radiator can now be cleaned entirely
from the front inspection port. Also the new furnace has
external clean-out ports so the soot does not fall into the
fan compartment during the cleaning operation.
IMPORTANT
Do not vacuum the ceramic chambers—they
are easily damaged.
Soot will have collected in the first sections of the heat
exchangers only if the burner was started after the
combustion chamber was flooded with fuel oil, or if the
burner has been operating in a severely fouled
condition.
1.2)
Refractory fire pot:
Remove the burner and check the fire pot.
IMPORTANT
Use extreme care if cleaning of the pot is
required. After firing, the pot becomes very
fragile. Do not use any commercially available
soot remover. This furnace has a fiber type
refractory combustion chamber. Normal
servicing of this unit does not require cleaning
of the combustion chamber.
If the pot is damaged, it must be replaced. A damaged
pot could lead to premature heat exchanger failure.
Cracking of the fire pot is normal, however, replace the
pot if the cracks have propagated more than 2/3 the
way through the wall thickness. The average wall
thickness of the firepot is 3/4”.
Flooding of the fire pot:
Flooding can occur when the oil primary control has
been reset a number of times in a no-heat situation.
Each time oil is fired into the pot and does not ignite, it
is absorbed in the pot. Even if the burner is removed
and the pot is felt for wetness, it is difficult to assess the
degree of oil absorption by the pot.
There is only one way to properly service a flooded fire
pot, and that is to change it.
CAUTION
If you observe the red warning light on the
burner, push once ONLY to try and restart. If
the burner will not start, phone your authorised
service agent. Do not press the button again.
Self-aligning firepot:
a. The appliance primary heat exchanger is comprised
of an upper and lower half. The lower half is
essentially a “can” that houses a self-aligning
firepot. the firepot will fit into the bottom half in one
orientation only.
b. A slot in the front of the firepot acts as a track that
captures a burner tube sleeve that extends into the
bottom heat exchanger half. This provides
automatic rotational alignment, vertical alignment.
c. Five tabs around the bottom and four tabs around
the top provide automatic centering of the firepot.
Removing the firepot:
The firepot is seldom replaced, but when it must be
replaced one must simply :
1. Remove the burner.
2. Remove the burner limit control.
3. Remove the breech plate.
4. Remove the front panel.
5. Remove the brass nuts on the stainless steel heat
exchanger studs.
6. Pry the bottom heat exchanger halves apart using
the designated prying tabs.
7. Remove the bottom heat exchanger half from the
furnace cavity through the front of the furnace.
8. Pull the firepot up and out of the bottom heat
exchanger half.
Содержание OLR Series
Страница 29: ...DNS 0571 Rev B DNS 0573 Rev B 30 FIGURE 5 1 Model OLR105A12B FIGURE 5 2 Model OLR160B20B...
Страница 30: ...31 FIGURE 5 3 Model OUF105A12B FIGURE 5 4 Model OUF160B18 DNS 0568 Rev C DNS 0572 Rev C...
Страница 31: ...FIGURE 5 5 Model OLF105A12B DNS 0570 Rev B FIGURE 5 6 Model NOUF105A12B 32 DNS 0674 Rev C...
Страница 32: ...33 FIGURE 5 7 Model NOUF160B18B FIGURE 5 8 Model NOLF105A12B DNS 0676 Rev C DNS 0675 Rev D...