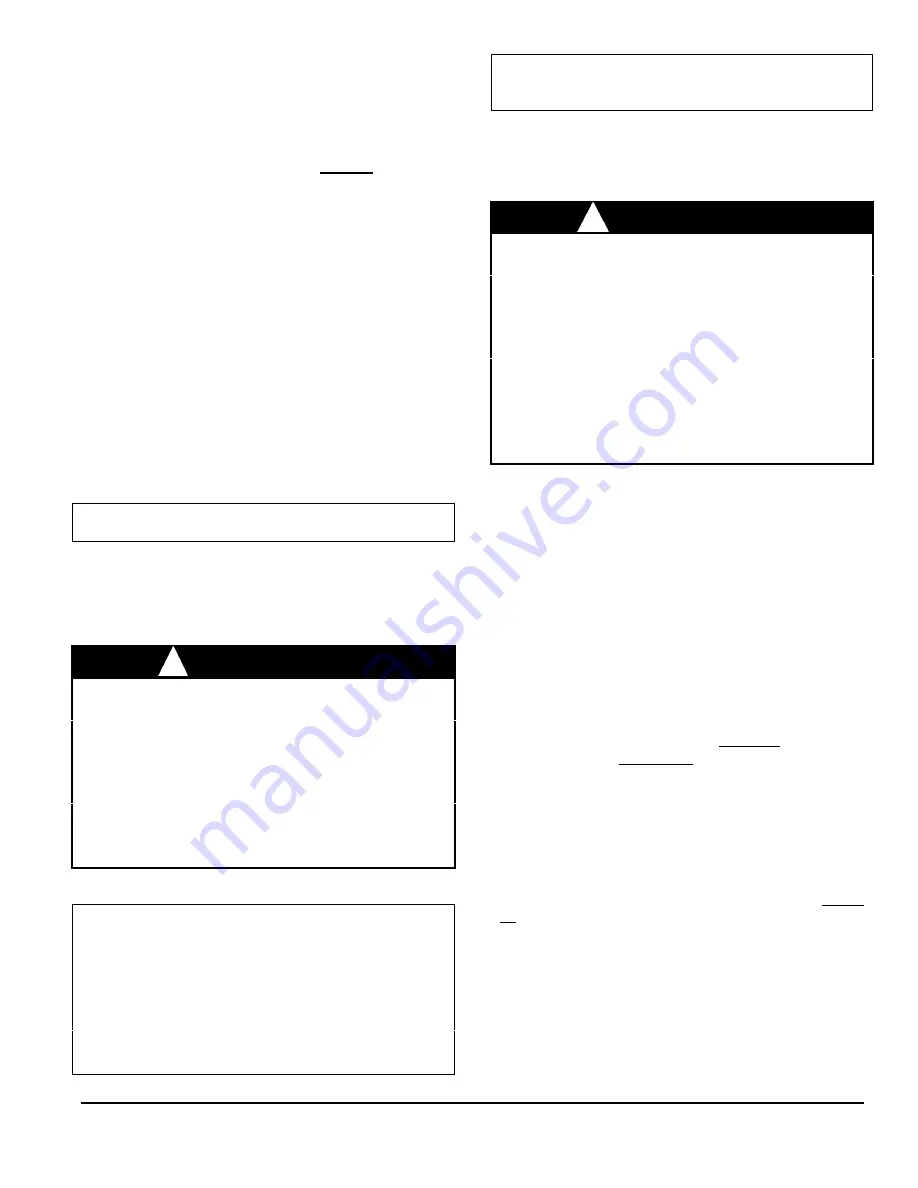
17
Nozzles:
The burners are provided with the highest capacity
USGPH nozzle installed. If another size nozzle, or
replacement nozzle is required, use the nozzle spray
angle, type and manufacturer recommended in Table
#4.1 to 4.3. Note that all nozzle-marked sizes are
based on a pump pressure of 100 psi.
Always select nozzle sizes by working back from the
actual desired flow rate at operating pressure, and not
by the nozzle marking.
Air and turbulator settings:
Before starting the burner for the first time, adjust the air
and turbulator settings to those listed in the Table #4.1
to #4.3. Once the burner becomes operational, final
adjustment will be necessary.
Fuel supply system:
Fuel Specifications
NOTE
: Use No.1 or No.2 Heating Oil (ASTM D396) or
in Canada, use No.1 or No.2 Furnace Oil.
Before starting the burner be sure the fuel tank is
adequately filled with clean oil.
WARNING
WARNING
Fire and explosion hazard.
Use only approved heating type oil in this
furnace. DO NOT USE waste oil, used
motor oil, gasoline or kerosene.
Use of these will result in death, personal
injury and/or property damage.
IMPORTANT
When using nozzle sizes of less than .75
USGPH, the Installation Code for oil burning
equipment requires the installation of a 10
micron (or less) filter in the fuel oil line. ICP
requires that this practice be followed in order
to keep the lifetime heat exchanger warranty
intact.
NOTE
: You may notice a slight odor the first time your
furnace is operated. This will soon disappear. It is only
the oil used on the parts during manufacturing.
8)
INSTALLING ACCESSORIES
WARNING
WARNING
Electrical shock hazard.
Turn OFF electric power at fuse box or
service panel before making any electrical
connections and ensure a proper ground
connection is made before connecting line
voltage.
Failure to do so could result in property
damage, bodily injury or death.
8.1)
Electronic air cleaner:
Wire leads are provided to direct 115 volts @ 0.5 Amp
maximum to an electronic air cleaner (EAC). Power will
be available to the EAC at all times, so it must
incorporate a flow proving switch if it is to be wired into
the furnace control box. Most modern EACs have the
required integral airflow-proving switch. Wire the
electronic air cleaner as indicated in figure #6.
8.2)
Humidifier:
Terminals are provided to direct 115 volts @ 1.0 Amp
maximum to the transformer powering the humidifier.
The humidifier will be energised anytime the blower is
operating on the “Heating Speed”. Wire the 115-volt
power as indicated in figure #6.
8.3)
Air conditioning:
An air conditioning coil may be installed on the supply
airside only. Also, notwithstanding the evaporator coil
manufacturer’s instructions, a minimum of 6 inches
clearance must be allowed between the bottom of the
coil drain pan, and the top of the heat exchanger. Wire
the thermostat and condensing unit contactor as
indicated in figure #6
.
!
!
Содержание OLR Series
Страница 29: ...DNS 0571 Rev B DNS 0573 Rev B 30 FIGURE 5 1 Model OLR105A12B FIGURE 5 2 Model OLR160B20B...
Страница 30: ...31 FIGURE 5 3 Model OUF105A12B FIGURE 5 4 Model OUF160B18 DNS 0568 Rev C DNS 0572 Rev C...
Страница 31: ...FIGURE 5 5 Model OLF105A12B DNS 0570 Rev B FIGURE 5 6 Model NOUF105A12B 32 DNS 0674 Rev C...
Страница 32: ...33 FIGURE 5 7 Model NOUF160B18B FIGURE 5 8 Model NOLF105A12B DNS 0676 Rev C DNS 0675 Rev D...