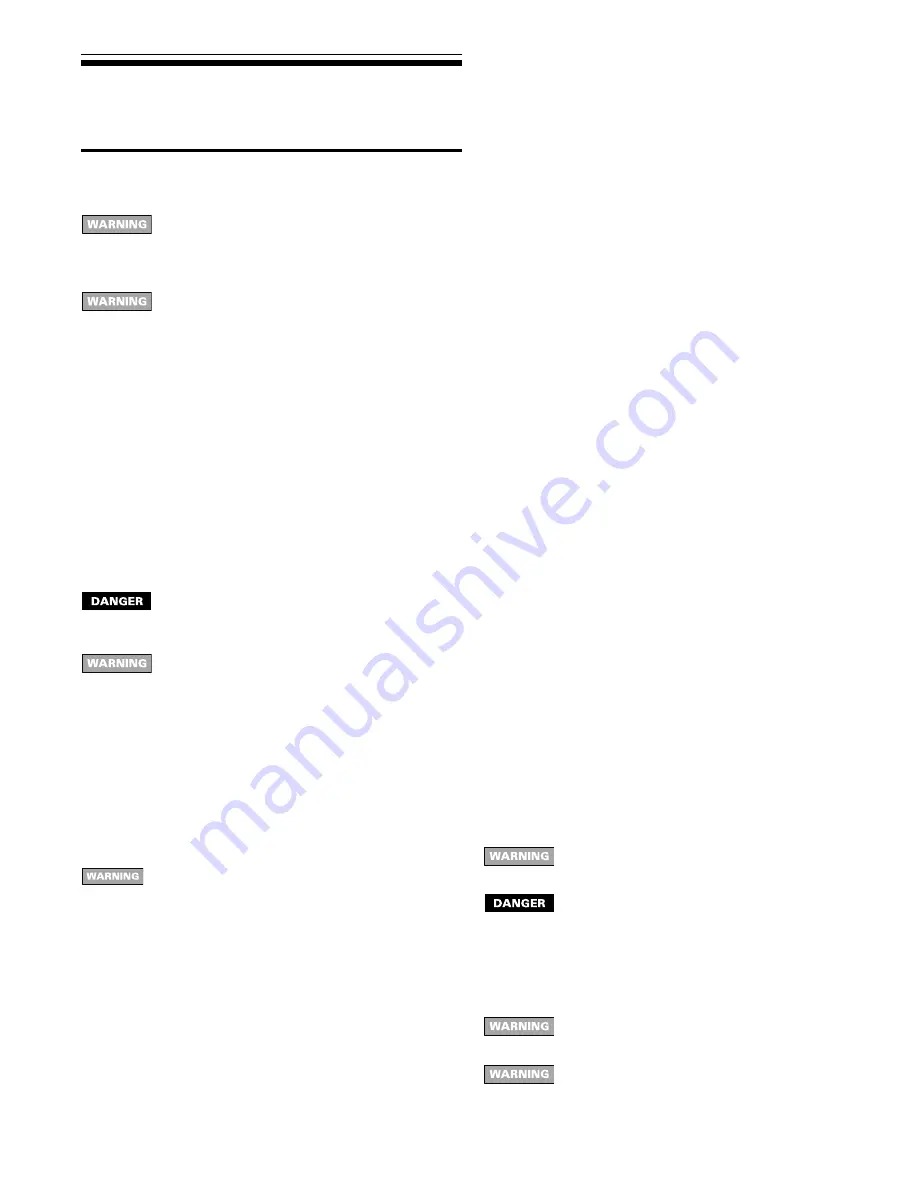
GWA
Gas-Fired Water Boilers –
Boiler Manual
15
Part Number 670 01 1001 00
Check for gas leaks
Before star ting the boiler, and during initial
operation, smell near the floor and around the boiler
for gas odorant or any unusual odor. Do not
proceed with start-up if there is any indication of a
gas leak. Repair any leak at once.
Propane boilers only — Your propane supplier mixes
an odorant with the propane to make its presence
detectable. In some instances, the odorant can fade
and the gas may no longer have an odor.
• Propane gas can accumulate at floor level. Smell near
the floor for the gas odorant or any unusual odor. If you
suspect a leak, do not attempt to light the pilot.
• Use caution when attempting to light the propane pilot.
This should be done by a qualified service technician,
particularly if pilot outages are common.
• Periodically check the odorant level of your gas.
• Inspect boiler and system at least yearly to make sure
all gas piping is leak-tight.
• Consult your propane supplier regarding installation
of a gas leak detector. There are some products on the
market intended for this purpose. Your supplier may be
able to suggest an appropriate device.
6
Start-up
Preparation
Fill the system with water
1. Close manual and automatic air vents and boiler drain cock.
2. Fill to correct system pressure. Correct pressure will vary
with each application. Typical cold water fill pressure for a
residential system is 12 psi.
3. Purge air from system:
a. Connect a hose to purge valve or valves, if installed.
Route hose to an area where water can drain and be
seen.
b. Close the boiler or system isolation valve between the
purge valve and fill connection to the system.
c. Close zone isolation valves.
d. Open quick-fill valve on cold water makeup line.
e. Open purge valve.
f.
One zone at a time, open the isolation valves. Allow water
to run through the zone, pushing out the air. Run until no
noticeable air flow is present. Close the zone isolation valves
and proceed with the next zone. Follow this procedure until
all zones are purged.
g. Close the quick-fill water valve and purge valve and remove
the hose. Open all isolation valves. Watch that system
pressure rises to correct cold-fill pressure.
h. After the system has operated for a while, eliminate any
residual air by using the manual air vents located throughout
the system.
i.
If purge valves are not installed in system, open manual air
vents in system one at a time, beginning with lowest floor.
Close vent when water squirts out. Repeat with remaining
vents.
4. Open automatic air vent (diaphragm-type or bladder-type
expansion tank systems only) one turn.
5. Open other vents:
a. Starting on the lowest floor, open air vents one at a time
until water squirts out.
b.
Repeat with remaining vents.
6. Refill to correct pressure.
Inspect system water piping
After filling the boiler and system with water, inspect all piping
throughout the system for leaks. If found, repair immediately. Repeat
this inspection after the boiler has been started and the system
has heated up.
Leaks must be repaired at once. Failure to do so can
damage the boiler, resulting in substantial property
damage.
Do not use petroleum-based cleaning or sealing
compounds in boiler system. Severe damage to boiler
will occur, resulting in substantial property damage.
Determine if water treatment is needed
Do not use petroleum-based cleaning or sealing
compounds in boiler system. Severe damage to
boiler will occur, resulting in substantial property
damage.
Eliminate all system leaks. Continual fresh makeup
water will reduce boiler life. Minerals can build up
in sections, reducing heat transfer, overheating
cast iron, and causing section failure.
Verify water chemistry
Consult local water treatment companies for unusually hard
water areas (above 7 grains hardness) or low pH water conditions
(below 7.0). Boiler water pH of 7.0 to 8.5 is recommended.
Freeze protection (when used)
Use antifreeze made especially for hydronic systems. Inhibited
propylene glycol is recommended.
Do not use ethylene glycol, automotive or undiluted
antifreeze. Severe personal injury or death can
result.
1. Determine antifreeze quantity according to system water
content. Boiler water content is listed on page 35. Remember
to include expansion tank water content.
2. Follow antifreeze manufacturer's instructions.
3. A 50% solution of propylene glycol/water provides maximum
protection to about -30 °F.
4. Local codes may require back flow preventer or actual
disconnect from city water supply.
5. When using antifreeze in a system with automatic fill, install
a water meter to monitor water makeup. Glycol will leak before
the water begins to leak, causing glycol level to drop. Added
water will dilute the antifreeze, reducing the freeze protection
level.
Inspect base insulation
Check to make sure insulation is secure against all four sides of
the base. If insulation is damaged or displaced, do not operate boiler.
Replace or reposition insulation.
Failure to replace damaged insulation or reposition
insulation can result in a fire hazard, causing severe
personal injury, death or substantial property damage.
The boiler contains ceramic fiber and fiberglass
materials. Use care when handling these materials
per instructions on page 23 of this manual. Failure to
comply could result in severe personal injury.
GWA
Gas-Fired Water Boilers –
Boiler Manual
22
Part Number 670 01 1001 00
Follow the “Service and maintenance” procedures given throughout this manual and in component literature shipped with
the boiler. See “Read this first” on page 2. Failure to perform the service and maintenance could result in damage to the boiler
or system. Failure to follow the directions in this manual and component literature could result in severe personal injury,
death or substantial property damage.
Table 6
Service and maintenance schedules (service technician and owner)
10 Service and maintenance
Service technician
(see following pages for instructions)
Owner maintenance
(see User’s Information Manual for instructions)
A
NN
NUA
L
ST
A
R
T
-
UP
❏
Inspect:
• Reported problems
• Boiler area
• Air openings
• Flue gas vent system
• Pilot and main burner flames
• Water piping
• Boiler heating surfaces
• Burners, base and inlet air box
❏
Service:
• Oiled-bearing circulators
❏
Start-up:
• Perform start-up per manual
❏
Check/test:
• Gas piping
• Cold fill and operating pressures
• Air vents and air elimination
• Limit controls and cutoffs
• Expansion tank
• Boiler relief valve
❏
Review:
• Review with owner
❏
Daily
• Check boiler area
• Check boiler pressure/
temperature gauge
• Check air openings
❏
Monthly
• Check boiler piping
• Check venting system
• Check boiler relief valve
• Check automatic air vents (if used)
• Check pilot and main burner flames
❏
Periodically
• Test low water cutoff (if used)
❏
Every 6 months
• Operate relief valve
❏
End of season
• Shut down procedure
Содержание GWA 245
Страница 2: ......
Страница 4: ......
Страница 6: ......
Страница 8: ......
Страница 10: ......
Страница 12: ......
Страница 14: ......
Страница 16: ......
Страница 18: ......
Страница 20: ......
Страница 22: ......
Страница 24: ......
Страница 26: ......
Страница 28: ......
Страница 30: ......
Страница 32: ......
Страница 34: ......
Страница 36: ......