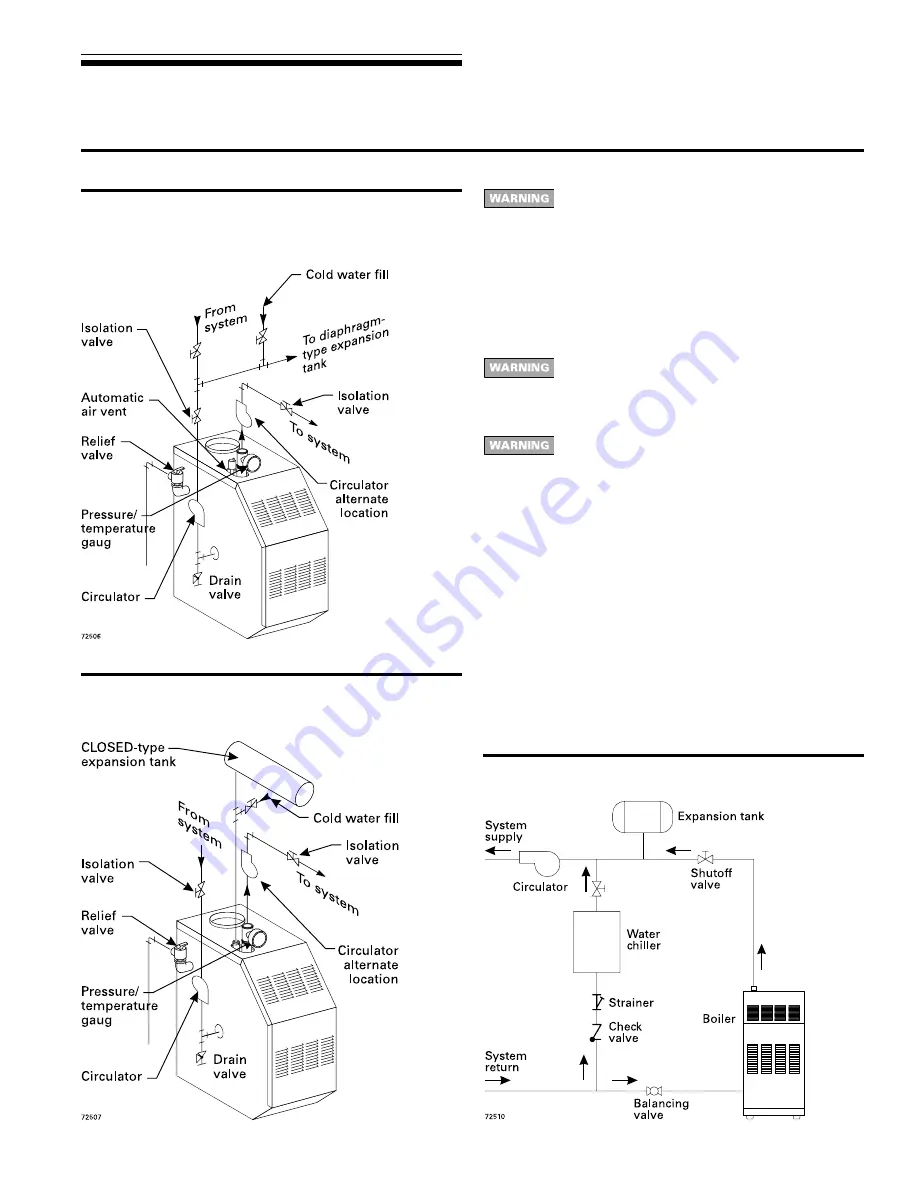
GWA
Gas-Fired Water Boilers –
Boiler Manual
11
Part Number 670 01 1001 00
Near-boiler piping
continued
Figure 7
Piping refrigeration systems
Water piping — refrigeration systems
Prevent chilled water from entering boiler
Install boiler so that chilled medium is piped in parallel with the
heating boiler. Use appropriate valves to prevent chilled medium
from entering boiler. See Figure 7 for typical installation of balancing
valve and check valve.
If system includes radiant heating circuits, provide
piping and controls to regulate the temperature
supplying the radiant circuits. Failure to comply could
result in substantial property damage.
Use Figure 5 or Figure 6 only for systems designed
for return water at least 130 °F. For systems with low
return water temperature possible, such as
converted gravity systems and radiant heating
systems, install bypass piping (see page 12) to
protect boiler against condensation. Failure to prevent
low return water temperature to the boiler could cause
corrosion of the boiler sections or burners, resulting
in severe personal injury, death or substantial
property damage.
Install boiler so that chilled medium is piped in parallel
with heating boiler (Figure 7). Use appropriate valves
to prevent chilled medium from entering boiler. Consult
I=B=R Installation and Piping Guides.
If boiler is connected to heating coils located in air
handling units where they can be exposed to
refrigerated air, use flow control valves or other
automatic means to prevent gravity circulation during
cooling cycle. Circulation of cold water through the
boiler could result in damage to the heat exchanger,
causing possible severe personal injury, death or
substantial property damage.
Figure 6
Closed-type expansion tank: Piping to
single-zone system using closed-type
expansion tank. See Table 4 for piping sizes.
Figure 5
Diaphragm- or bladder-type expansion tank:
Piping to single-zone system using
diaphragm-type or bladder-type expansion
tank. See Table 4 for piping sizes.
3
Install water piping
continued
GWA
Gas-Fired Water Boilers –
Boiler Manual
26
Part Number 670 01 1001 00
10 Service and maintenance
continued
❏
❏
❏
❏
❏
Check/test. . . . . . . . . .
continued
Diaphragm- or bladder-type — welded gas tight with a rubber
membrane to separate the tank pressurizing air and the water.
May be located at any point in the system, but most often found
near the boiler.
•
Systems with this type of expansion tank require at least
one automatic air vent, preferably located on top of an air
eliminator, as shown in examples in Manual Section 3,
page 10.
2. If relief valve has tended to weep frequently, the expansion tank
may be waterlogged or undersized.
Closed-type tank — tank is most likely waterlogged. Install a
tank fitting if not already installed. Then check fill level per fitting
manufacturer’s instructions. If fill level is correct, check tank
size against manufacturer’s instructions. Replace with a larger
tank if necessary.
Diaphragm- or bladder-type — first, check tank size to be
sure it is large enough for the system. If size is too small, add
additional tank(s) as necessary to provide sufficient expansion.
If tank size is large enough, remove tank from system and
check charge pressure (usually 12 psig for residential
applications). If tank won’t hold pressure, membrane has been
damaged. Replace tank.
Boiler relief valve
1. Inspect the relief valve and lift the lever to verify flow as in the
following warnings, excerpted from a relief valve manufacturer’s
warning label. Before operating any relief valve, ensure that it is
piped with its discharge in a safe area to avoid severe scald
potential. Read Manual Section 3, page 10, before proceeding
further.
2. After following the preceding warning directions, if the relief valve
weeps or will not seat properly, replace the relief valve. Ensure
that the reason for relief valve weeping is the valve and not
over-pressurization of the system due to expansion tank
waterlogging or undersizing.
❏
❏
❏
❏
❏
Review with owner
1. Review the User’s Information Manual with the owner.
2. Emphasize the need to perform the maintenance schedule
specified in the User’s Information Manual (and in this manual
as well).
3. Remind the owner of the need to call in a licensed contractor
should the boiler or system exhibit any unusual behavior.
4. Remind the owner to follow the proper shutdown procedure
and to schedule an annual start-up at the beginning of the next
heating season.
The boiler contains ceramic fiber and fiberglass
materials. Use care when handling these materials
per instructions on page 23 of this manual. Failure to
comply could result in severe personal injury.
1. Shut down boiler:
•
Follow “To Turn Off Gas to Appliance” instructions on boiler
and “Lighting or Operating Instructions”.
•
Do not drain boiler unless it will be exposed to freezing
temperatures. If using antifreeze in system, do not drain.
2. Follow shutdown procedure.
3. Remove venting system connection to boiler.
4. Remove top jacket panel. Turn back insulation.
5. Remove flue collector. Clean sealant from assembly and
sections.
6. Remove radiation plates hanging between sections.
7. Remove burners from base. Brush and vacuum burners to
remove all dust and lint. Verify that all burner ports are free of
debris.
8. Place newspapers in base of boiler to collect soot.
9. Clean between sections with wire flue brush.
10. Remove newspaper and soot. Vacuum or brush base and
surrounding area.
11. Reinstall radiation plates.
12. Replace collector box/transition assembly. Seal with sealant.
Obtain gas-tight seal to prevent flue gas spillage and carbon
monoxide emissions, resulting in severe personal injury or death.
13. Replace insulation and jacket top panel.
14. Start up boiler following section 6, pages 15–17 of this manual
and the boiler “Lighting Instructions”, pages 20 and 21.
Excessive sooting indicates improper gas combustion. If found,
check for proper combustion and make any necessary
adjustments.
❏
❏
❏
❏
❏
Cleaning boiler heating surfaces
Safety relief valves should be reinspected AT LEAST
ONCE EVERY THREE YEARS, by a licensed plumb-
ing contractor or authorized inspection agency, to
ensure that the product has not been affected by
corrosive water conditions and to ensure that the
valve and discharge line have not been altered or
tampered with illegally. Certain naturally occurring
conditions may corrode the valve or its components
over time, rendering the valve inoperative. Such con-
ditions are not detectable unless the valve and its
components are physically removed and inspected.
This inspection must only be conducted by a plumb-
ing contractor or authorized inspection agency — not
by the owner. Failure to reinspect the boiler relief valve
as directed could result in unsafe pressure buildup,
which can result in severe personal injury, death or
substantial property damage.
Following installation, the valve lever must be oper-
ated AT LEAST ONCE A YEAR to ensure that wa-
terways are clear. Certain naturally occurring min-
eral deposits may adhere to the valve, rendering it
inoperative. When manually operating the lever, wa-
ter will discharge and precautions must be taken to
avoid contact with hot water and to avoid water dam-
age. Before operating lever, check to see that a dis-
charge line is connected to this valve directing the
flow of hot water from the valve to a proper place of
disposal otherwise severe personal injury may re-
sult. If no water flows, valve is inoperative. Shut down
boiler until a new relief valve has been installed.
Содержание GWA 245
Страница 2: ......
Страница 4: ......
Страница 6: ......
Страница 8: ......
Страница 10: ......
Страница 12: ......
Страница 14: ......
Страница 16: ......
Страница 18: ......
Страница 20: ......
Страница 22: ......
Страница 24: ......
Страница 26: ......
Страница 28: ......
Страница 30: ......
Страница 32: ......
Страница 34: ......
Страница 36: ......