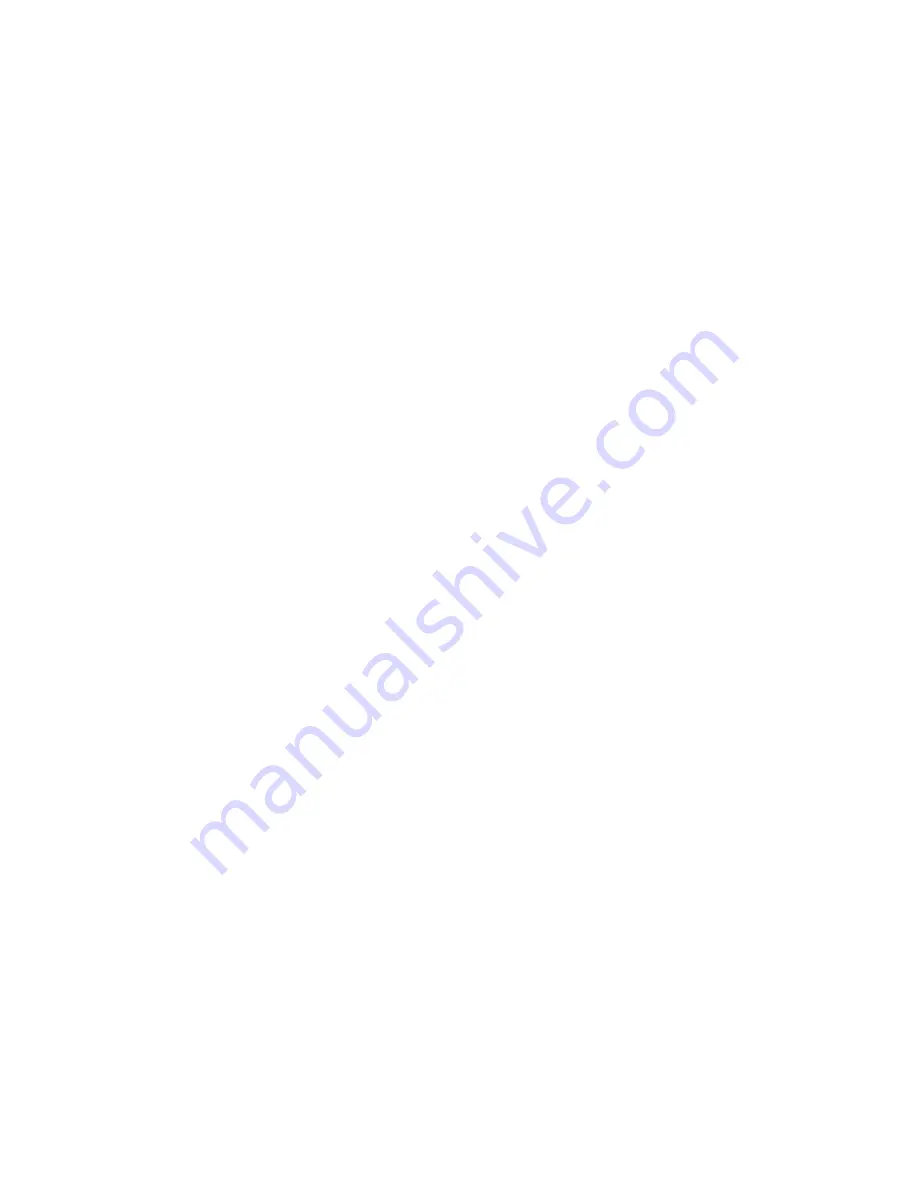
GWA
Gas-Fired Water Boilers –
Boiler Manual
12
Part Number 670 01 1001 00
Figure 8
System bypass piping in boiler loop with
separate system circulator, using primary/
secondary piping.
Figure 9
Boiler bypass piping — use only for high
water content systems —DO NOT use for
radiant panel systems.
Near-boiler piping
continued
Install all components specified above and adjust valves as described to prevent low temperature in the boiler. Failure to
prevent low water temperature in the boiler could cause corrosion of the boiler sections or burners, resulting in severe
personal injury, death or substantial property damage.
3
Install water piping
continued
System bypass method
1. Apply bypass piping of Figure 8 to high water content systems,
radiant panel systems or any system that is likely to operate
with low return water temperature for extended periods.
2. The bypass arrangement shown protects the boiler from damage
caused by condensate corrosion due to low return water
temperature and protects low temperature systems from too
high a supply temperature.
3. Adjust the bypass valves as indicated below.
Adjust Bypass valves 1 and 2 as follows:
1. Start with valve 2 fully closed, valve 1 fully open.
2. Slowly open valve 2 while closing valve 1. Adjust the valves
until the boiler pressure/temperature gauge reads 160 °F or
higher. As you open the valves, pause long enough to allow
temperatures to level off. It takes a while for the boiler water
temperature to rise as the flow changes.
3. Bypass valve 2 allows hot boiler outlet water to blend with colder
return water, raising the supply temperature to the boiler. Bypass
valve 1 balances the pressure drop through valve 2.
4. The purpose of this piping is to raise the return water temperature
to the boiler enough to prevent condensation of flue gases.
Boiler bypass method
1. Apply bypass piping of Figure 9 to high water content systems,
such as converted gravity systems.
2. The bypass arrangement shown protects the boiler from damage
caused by condensate corrosion due to low return water
temperature. This method does not provide protection from high
temperature water being supplied to the system.
3. DO NOT apply this piping to radiant panel systems.
4. Adjust the bypass valves as indicated below.
Adjust Bypass valves 1 and 2 as follows:
1. Start with valve 1 fully closed, valve 2 fully open.
2. Slowly open valve 1 while closing valve 2. Adjust the valves
until the boiler pressure/temperature gauge reads approximately
60 °F higher than the system temperature gauge. As you open
the valves, pause long enough to allow temperatures to level
off. It takes a while for the boiler water temperature to rise as
the flow changes.
3. Bypass valve 1 controls system flow rate. Bypass valve 2
controls flow through the boiler.
4. The purpose of this piping is to cause a high enough temperature
rise in the boiler that the average temperature will be warm
enough to prevent condensation of flue gases.
GWA
Gas-Fired Water Boilers –
Boiler Manual
25
Part Number 670 01 1001 00
❏
❏
❏
❏
❏
Check/test. . . . . . . . . .
Air vents and air elimination
1. Inspect automatic air vents (if used). Also inspect air separators
to ensure they are operational.
2. The cap must be unscrewed one turn to allow air to escape.
3. If the air vent is leaking, remove cap and briefly push valve —
then release to clean the valve seat.
4. Replace cap by twisting all the way onto valve and then
unscrewing one turn.
Limit controls and cutoffs
1. Inspect and test the boiler limit control. Verify operation by turning
control set point below boiler temperature. Boiler should cycle
off. Return dial to original setting.
2. Inspect and test additional limit controls or low water cutoffs
installed on system.
Expansion tank
1. Expansion tanks provide space for water to move in an out as
the heating system water expands due to temperature increase
or contracts as the water cools. Tanks may be open, closed or
diaphragm or bladder type. See Section 3, page 10 of this
manual for suggested locations of expansion tanks and air
eliminators.
Open-type — located above highest radiator or baseboard unit,
usually in the attic or closet. Has a gauge glass and overflow
pipe to a drain.
Closed-type — welded gas tight and located above boiler. Tank
is partially filled with water, leaving an air cushion for expansion.
•
Make sure this type of tank is fitted with a tank fitting, such
as the B & G Tank-Trol or Taco Taco-Trol. This fitting reduces
gravity circulation of air-saturated tank water back to the
system and prevents the air from bubbling up through the
water as it returns from the system.
•
Do not use automatic air vents in systems with closed-type
tanks. The air will escape from the system instead of
returning to the tank. Eventually, the tank will waterlog and
no longer control pressurization. The boiler relief valve will
weep frequently.
10 Service and maintenance
continued
❏
❏
❏
❏
❏
Check/test. . . . . . . . . .
Gas piping
1. Sniff near floor and around boiler area for any indication of a
gas leak.
2. Test gas piping using bubble test, per Section 4, page 13 of this
manual, if there is any indication of a leak.
Cold fill and operating pressures
1. While the system is cold, note the pressure reading on the boiler
pressure/temperature gauge. Verify that cold fill pressure is
correct.
2. Watch the pressure as the boiler and system heat up to ensure
pressure rise is normal. Too high a rise would indicate a
waterlogged or undersized expansion tank.
❏
❏
❏
❏
❏
Start-up. . . . . . . . . .
1. Perform start-up procedures Section 6, pages 15–17, including
“Verify operation” of burners and vent damper on page 17.
2. Verify cold fill pressure is correct and that fill system is working
properly.
3. Verify antifreeze level (if used) is at the right concentration and
that inhibitor level is correct.
4. Check gas piping, per Manual Section 4, page 13 and Section
6, page 15, verifying no indications of leakage and all piping
and connections are in good condition.
5. Read the “Lighting or Operating Instructions” (Manual Section 9,
pages 20 and 21 or Control Supplement) applying to the boiler.
6. Start the boiler following the “Lighting or Operating Instructions”
(Manual Section 9, pages 20 and 21 or Control Supplement).
Oiled-bearing circulators
1. The circulator shipped with the GWA boiler is water-lubricated.
No oiling is required.
2. Check other circulators in the system. Oil any circulators
requiring oil, following circulator manufacturer’s instructions.
Over-oiling will damage the circulator.
❏
❏
❏
❏
❏
Service. . . . . . . . . .
Содержание GWA 245
Страница 2: ......
Страница 4: ......
Страница 6: ......
Страница 8: ......
Страница 10: ......
Страница 12: ......
Страница 14: ......
Страница 16: ......
Страница 18: ......
Страница 20: ......
Страница 22: ......
Страница 24: ......
Страница 26: ......
Страница 28: ......
Страница 30: ......
Страница 32: ......
Страница 34: ......
Страница 36: ......