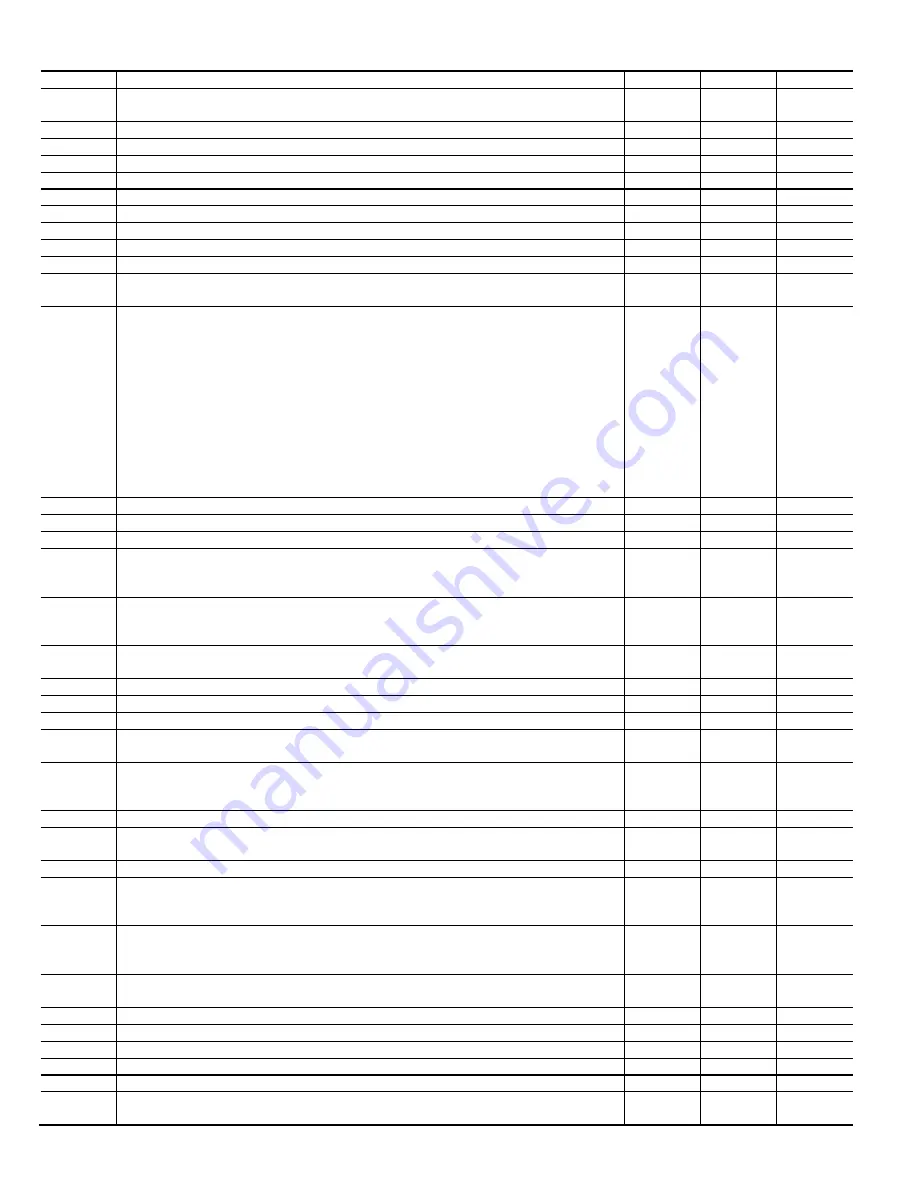
- 20 -
STEP
ACTION
YES
NO
GO TO
40.
Remove tape from door switch, turn power off at main disconnect, and remove jumper across
R and W/W1.
41
41.
Is the blower wheel firmly mounted on motor shaft?
42
26
42.
Does the model plug PL4 match the part number specified on the Rating Plate?
44
43
43.
Replace model plug.
10
44.
Clean or replace filter if necessary, then recycle furnace after limit resets.
45
45.
Turn power on and depress door switch. Use a piece of tape to hold switch closed.
46
46.
Jumper R and W/W1 thermostat terminals.
47
47.
Observe furnace operation for 15 minutes or until status code 4 starts flashing.
48
48.
Does status code 4 still occur during intermediate heat?
50
49
49.
Does a different status code flash?
5
10
50.
Is furnace considerably overfired (10% or more)? Clock input rate. Do not use manifold
pressure method unless using propane.
51
52
51.
Ensure gas inlet pressure and burner orifices (natural or propane) are correct. Then adjust gas
valve to proper rate per Installation, Start-Up, and Operating Instructions. If it cannot be
adjusted to proper rate, replace gas valve.
Note:
The modulating furnace manifold pressure is set at two points. The first point is
maximum heat. The second point is minimum heat. Both adjustments are independent and
are done with the same rotary adjustment switch on the modulating gas valve. When
adjusting do not apply excessive force as you may damage the rotary adjustment switch. To
adjust, slowly turn the rotary adjustment switch counterclockwise to decrease manifold
pressure or clockwise to increase manifold pressure. Turn the rotary adjustment switch one
click per second until you obtain the desired manifold pressure. If you turn the rotary
adjustment switch too quickly the manifold pressure will not change.
10
52.
Is temperature rise within rise range?
54
53
53.
Does the installation have a bypass humidifier or zoning system bypass?
58
61
54.
Turn power off and install a temperature probe in front of limit switch button.
55
55.
Turn power on and cycle unit. Does limit switch open at a temperature at least 10 deg. F
below temperature setpoint for limit switch? (EXAMPLE: The setpoint is 170 deg F, but the
switch opens at a temperature below 160 deg F.)
18
56
56.
The problem may be related to poor air distribution or excessive pressure drop across filter.
Check filter and return-air grilles for blockage. Add turning vanes, more supply openings, or
more return-air openings. Use Appendix D to evaluate external static pressure.
26
57.
With blower door in place record temperature rise across return air duct before and after the
bypass.
58
58.
Is temperature rise of return air from bypass greater than 15 deg. F?
59
60
59.
The bypass is oversized. Adjust damper or replace with properly sized bypass.
10
60.
Does installation have modulating zone dampers?
61
65
61.
Disable modulating zone damper system with all dampers in open position except bypass
damper. If installation is equipped with a bypass damper, it should be in the closed position.
62
62.
Turn power off and disconnect jumper from the R thermostat terminal. Turn power back on
and reconnect jumper to R thermostat terminal. Observe for 15 minutes with the blower door
in place.
63
63.
Does status code 4 flash?
65
64
64.
The problem is caused by the modulating zone damper system. Check the zoning system
manufacturer’s Installation and Troubleshooting guide for corrective action.
10
65.
Turn power off and install a temperature probe in front of limit switch button.
66
66.
Turn power on and cycle unit. Does limit switch open at a temperature at least 10 deg. F
below temperature setpoint for limit switch? (EXAMPLE: The setpoint is 170 deg F, but the
switch opens at a temperature below 160 deg F.)
18
67
67.
Adjust the blower airflow using dip switch SW1-3 and SW1-4 to get the temperature rise
within the rise range.
On systems with Communicating Wall Control set at the
Communicating Wall Control.
26
68.
Remove tape from door switch, turn power off at main disconnect, and remove jumpers
across R, W/W1, and W2.
69
69.
Put setup switch SW4-2 in the OFF position.
70
70.
Jumper R and W/W1 thermostat terminals.
71
71.
Observe furnace operation for 15 minutes or until status code 4 starts flashing.
72
72.
Does status code 4 flash occur during minimum heat?
74
73
73.
Does a different status code flash?
5
10
74.
Is furnace considerably overfired (10% or more)? Clock input rate. Do not use manifold
pressure method unless using propane.
51
65
440 08 4001 00
Содержание 9MAC/E series
Страница 39: ...39 Fig 2 Wiring Schematic 440 08 4001 00...
Страница 41: ...41 Figure 3 ECM Blower Motor 440 08 4001 00...
Страница 48: ...48 Replaces New Form ICP Eng 3 12 440 08 4001 00...