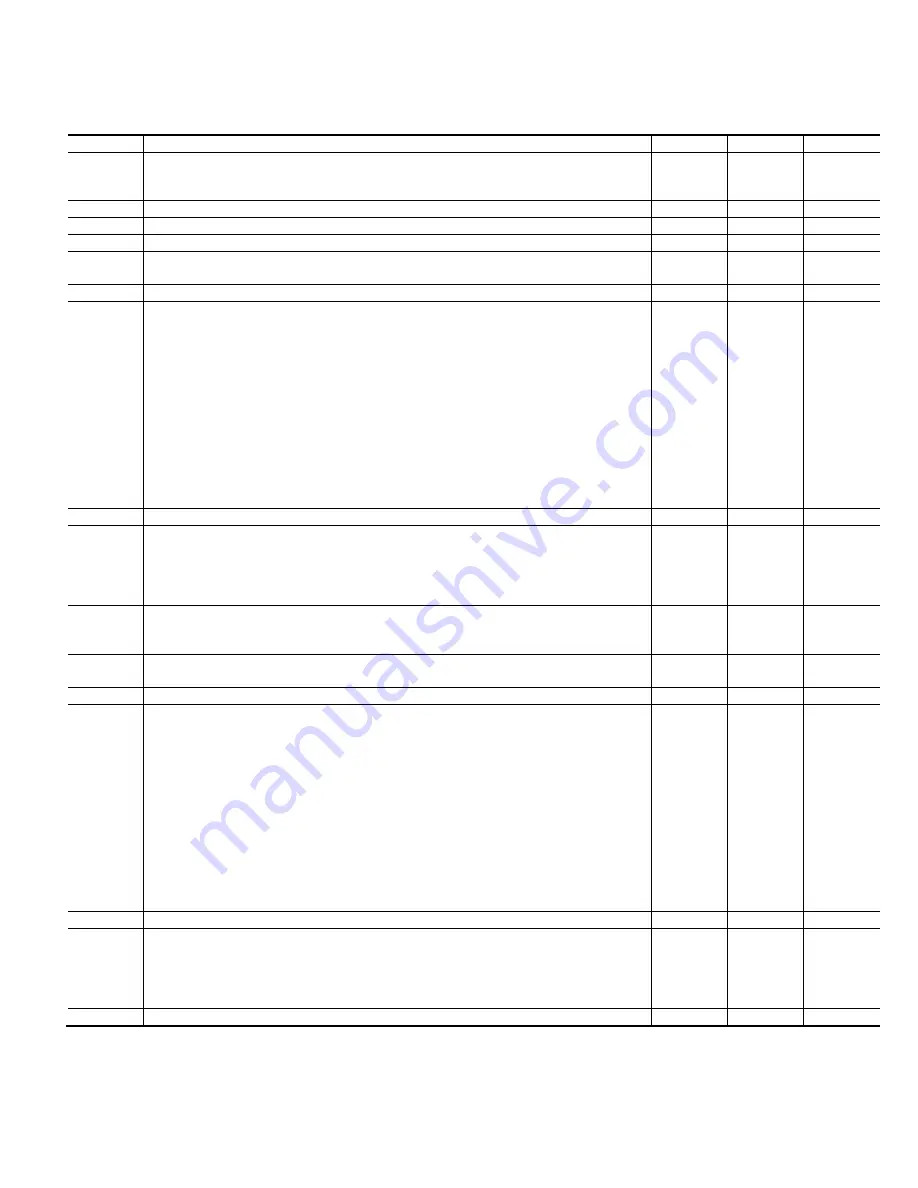
- 13 -
MINIMUM AND/OR MAXIMUM HEAT TEMPERATURE RISE TOO LOW - Generally, this
indicates the furnace is extremely underfired.
STEP
ACTION
YES
NO
GO TO
1.
Remove the blower door. Disconnect the communication connector PL7 (if used) or the R
thermostat lead (if used) from the furnace control board. If setup switch SW4-2 is ON then
turn it OFF.
2
2.
Depress the door switch. Use piece of tape to hold it closed.
3
3.
Put setup switch SW1-2 into the ON position.
4
4.
Jumper R, W/W1, and W2 thermostat terminals.
5
5.
Once the blower motor turns ON and the furnace is running in maximum heat, clock the
maximum heat gas rate. On propane installations check the manifold pressure.
6
6.
Is the maximum heat rate within 2% of that specified on the rating plate?
9
7
7.
Ensure the gas inlet pressure and burner orifices are correct. Reference the Installation, Start-
Up, and Operating Instructions. Then adjust maximum heat on the gas valve to the proper
manifold pressure. If maximum heat cannot be adjusted to the proper manifold pressure,
replace the gas valve GV.
Note:
The modulating furnace manifold pressure is set at two points. The first point is
maximum heat. The second point is minimum heat. Both adjustments are independent and
are done with the same rotary adjustment switch on the modulating gas valve. When
adjusting do not apply excessive force as you may damage the rotary adjustment switch. To
adjust, slowly turn the rotary adjustment switch counterclockwise to decrease manifold
pressure or clockwise to increase manifold pressure. Turn the rotary adjustment switch one
click per second until you obtain the desired manifold pressure. If you turn the rotary
adjustment switch too quickly the manifold pressure will not change.
11
8.
Fix problem.
11
9.
Check maximum heat temperature rise and external static pressure with blower door in place.
Temperature rise should be mid range or higher than midpoint of range stated on furnace
rating plate. External static pressure in maximum heat should be less then .7 in.w.c. If
return temperature is below 60 deg. F condensation may form on heat exchangers. If left
uncorrected failure will result.
10
10.
Remove the jumper from the R and W2 thermostat terminals. When the furnace is running in
minimum heat, clock the minimum heat gas rate. On propane installations check the
manifold pressure.
12
11.
Go to the page number indicated in Index for the CLEANUP AND STARTUP
INSTRUCTIONS.
INDEX
12.
Is the minimum heat rate within 2% of that specified on the rating plate?
14
13
13.
Ensure the gas inlet pressure and burner orifices are correct. Reference the Installation, Start-
Up, and Operating Instructions. Then adjust minimum heat on the gas valve to the proper
manifold pressure. If minimum heat cannot be adjusted to the proper manifold pressure,
replace the gas valve GV.
Note:
The modulating furnace manifold pressure is set at two points. The first point is
maximum heat. The second point is minimum heat. Both adjustments are independent and
are done with the same rotary adjustment switch on the modulating gas valve. When
adjusting do not apply excessive force as you may damage the rotary adjustment switch. To
adjust, slowly turn the rotary adjustment switch counterclockwise to decrease manifold
pressure or clockwise to increase manifold pressure. Turn the rotary adjustment switch one
click per second until you obtain the desired manifold pressure. If you turn the rotary
adjustment switch too quickly the manifold pressure will not change.
11
14.
Is outdoor condensing unit operating during heating cycle?
8
15
15.
Check minimum heat temperature rise and external static pressure with blower door in place.
Temperature rise should be mid range or higher than midpoint of range stated on furnace
rating plate. External static pressure in minimum heat should be less then .25 in.w.c. If
return temperature is below 60 deg. F condensation may form on heat exchangers. If left
uncorrected failure will result.
16
16.
Check return air ducts in unheated spaces for leaks.
11
440 08 4001 00
Содержание 9MAC/E series
Страница 39: ...39 Fig 2 Wiring Schematic 440 08 4001 00...
Страница 41: ...41 Figure 3 ECM Blower Motor 440 08 4001 00...
Страница 48: ...48 Replaces New Form ICP Eng 3 12 440 08 4001 00...