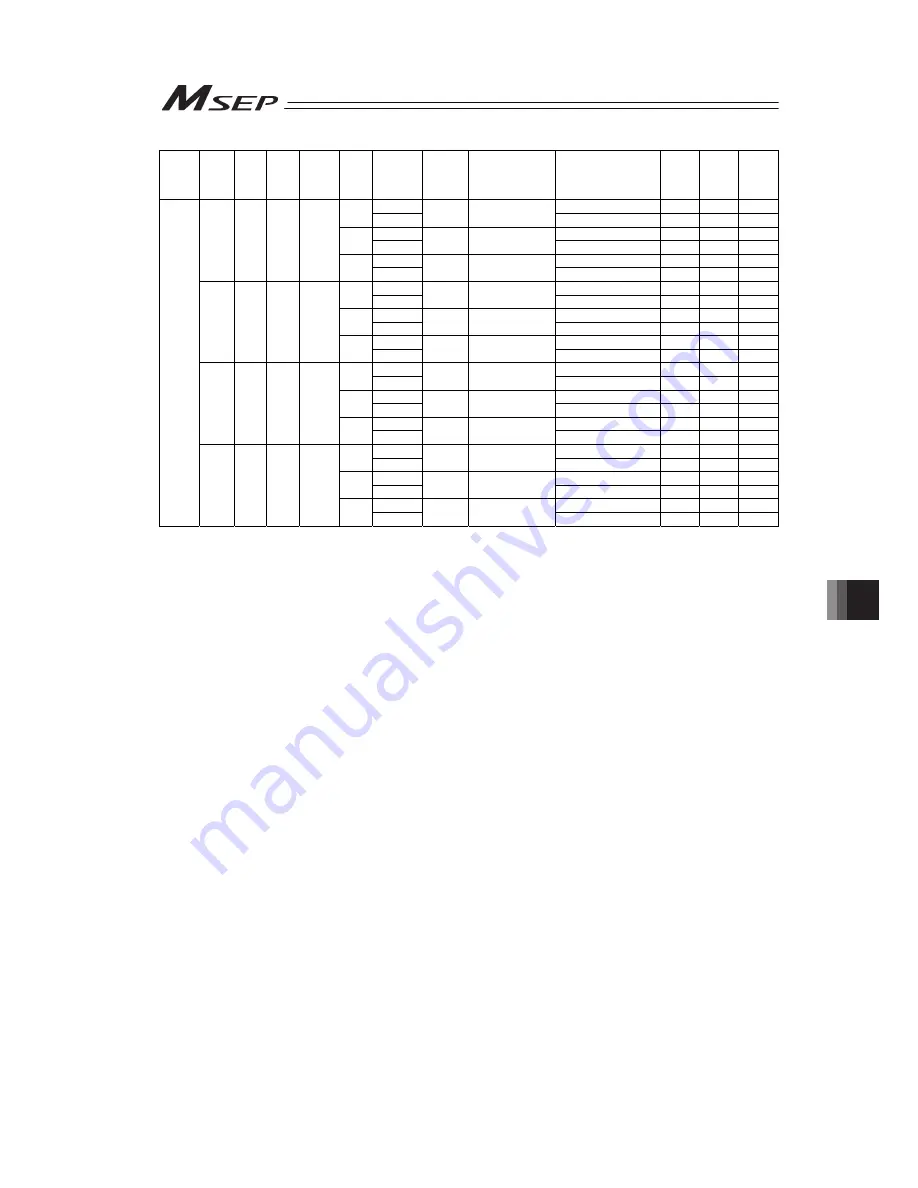
Chapter 7
Appendix
245
Motor
output
Lead
Minimum
speed
Maximum speed Maximum acceleration/
deceleration
Minimum
push force
Maximum
push force
Rated
push
speed
Actuator
series
Type Feed
screw
[W]
No. of
encoder
pulses
[mm]
Mounting
direction
[mm/s]
[mm/s]
[G]
[N]
[N]
[mm/s]
Horizontal
0.3
–
–
–
6
Vertical
7.5
300
0.2
–
–
–
Horizontal
0.3
–
–
–
4
Vertical
5
200
0.2
–
–
–
Horizontal
0.2
–
–
–
SA3C Ball
screw 10
800
2
Vertical
2.5
100
0.2
–
–
–
Horizontal
0.3
–
–
–
6
Vertical
7.5
300
0.2
–
–
–
Horizontal
0.3
–
–
–
4
Vertical
5
200
0.2
–
–
–
Horizontal
0.2
–
–
–
SA3R Ball
screw 10
800
2
Vertical
2.5
100
0.2
–
–
–
Horizontal
0.3
–
–
–
10
Vertical
12.5
380 (at 50st)
500 (at 100 to 500st)
0.2
–
–
–
Horizontal
0.3
–
–
–
5
Vertical
6.25
250
0.2
–
–
–
Horizontal
0.2
–
–
–
SA4C Ball
screw 20
800
2.5
Vertical
3.12
125
0.2
–
–
–
Horizontal
0.3
–
–
–
10
Vertical
12.5
380 (at 50st)
500 (at 100 to 500st)
0.2
–
–
–
Horizontal
0.3
–
–
–
5
Vertical
6.25
250
0.2
–
–
–
Horizontal
0.2
–
–
–
RCA2
(slider
type)
SA4R Ball
screw 20
800
2.5
Vertical
3.12
125
0.2
–
–
–
Содержание Msep
Страница 1: ...MSEP Controller Instruction Manual Fourth Edition ...
Страница 2: ......
Страница 4: ......
Страница 8: ......
Страница 202: ...3 10 Status LED 194 Note 1 blinking Note 2 single flash Note 3 double flash Timing of LED flashing ...
Страница 244: ...Chapter 6 Troubleshooting 236 ...
Страница 290: ...Chapter 7 Appendix 282 ...
Страница 294: ......
Страница 295: ......