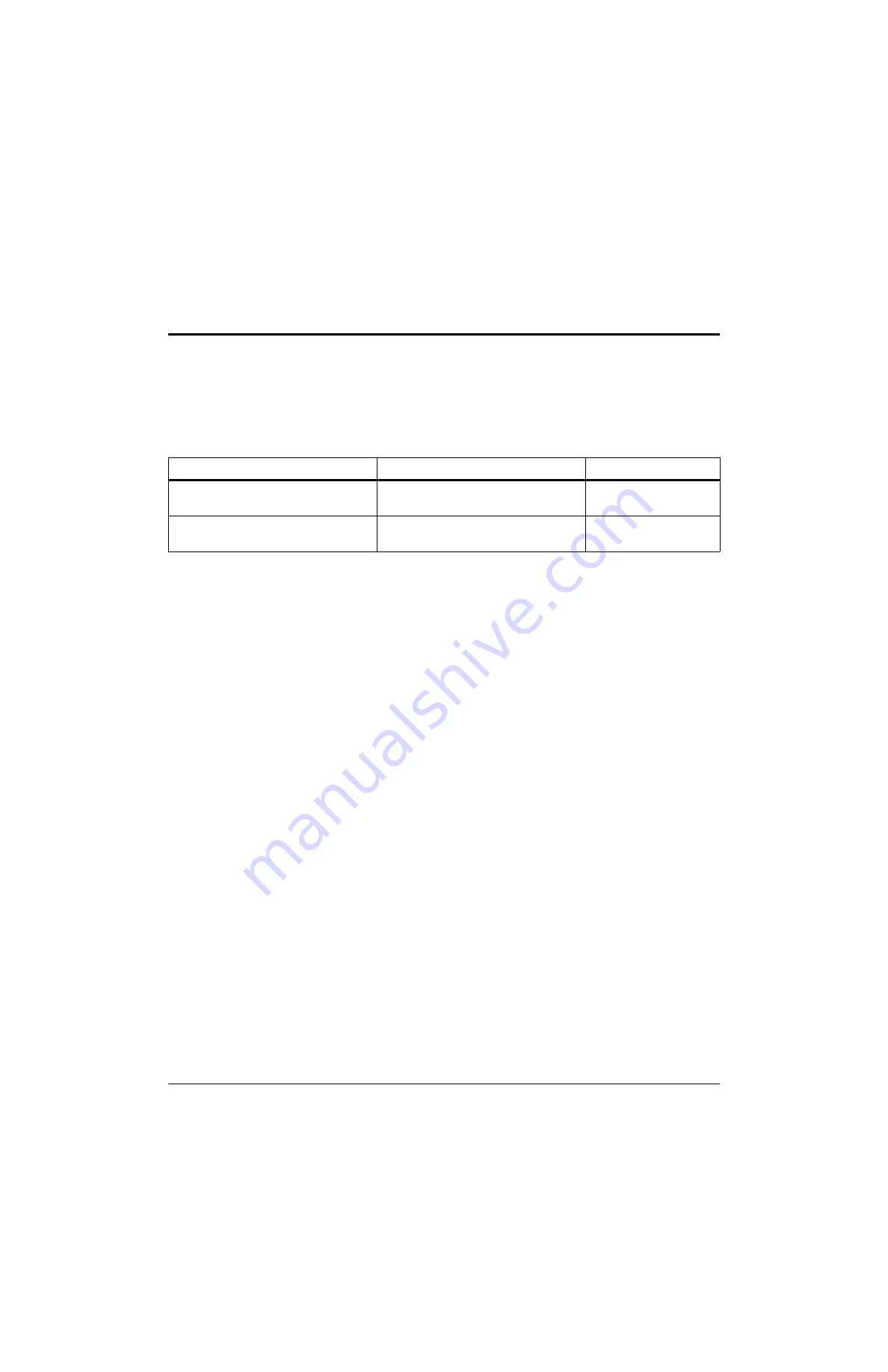
Operation
6
XPR300
Instruction Manual
809480
225
Factors of cut quality
Dross
Dross is more likely to occur on a hot workpiece. The first cut in a series often produces the
least dross. You can expect more dross with more cuts.
Changes in shield flow can dramatically influence dross formation on non-ferrous metals.
* Worn or damaged consumables can produce intermittent dross.
How to get the results you want
This section of the manual gives general recommendations for how to get the best results for many
processes.
For instructions on how to troubleshoot specific performance problems,
see
Diagnostics and Troubleshooting
General recommendations for all processes
Always start with the default settings for the process that you want to use. In most cases,
you can expect the best results when you use the default settings that come with a
process ID.
If you decide that it is necessary to adjust a default setting, use offset or override commands
to make incremental changes to the original value (values), within limits. (See
Do not allow the torch to touch the workpiece during cutting system operation. Contact with
the workpiece can damage the torch nozzle and shield. It can also damage the surface of
the workpiece.
Make sure that the torch is perpendicular (at a 90° angle) to the workpiece for
perpendicular-position processes.
Unsteady drive system and rail movement can make torch motion unsteady, which can
cause irregular cut patterns. Make sure to do routine service and maintenance to the drive
system and rails.
See the instruction manual that came with your cutting machine or table
for information on how to do this.
Do all cutting system maintenance tasks as scheduled. (See
Problem
Cause*
Solution
On mild steel, low-speed dross is
heavier, but easy to remove.
The plasma arc can move ahead of the
torch when the torch speed is too slow.
Increase the torch speed.
On mild steel, high-speed dross is finer,
but difficult to remove.
The plasma arc can lag behind the torch
when the torch speed is too fast.
Decrease the torch
speed.
Содержание XPR300
Страница 1: ...XPR300 Plasma Instruction Manual 809480 Revision 2 English ...
Страница 18: ...Contents 18 809480 Instruction Manual XPR300 ...
Страница 34: ...Specifications 1 34 809480 Instruction Manual XPR300 ...
Страница 66: ...Qualifications and Requirements 2 66 809480 Instruction Manual XPR300 ...
Страница 188: ...Connect for Communication 4 188 809480 Instruction Manual XPR300 ...
Страница 192: ...Coolant Installation 5 192 809480 Instruction Manual XPR300 ...
Страница 230: ...Operation 6 230 809480 Instruction Manual XPR300 ...
Страница 337: ...Parts List 9 XPR300 Instruction Manual 809480 337 ...
Страница 343: ...Parts List 9 XPR300 Instruction Manual 809480 343 ...
Страница 380: ...Wiring Diagrams 10 380 809480 Instruction Manual XPR300 ...
Страница 381: ...381 Overview Sheet 1 of 22 013403 013403 ...
Страница 382: ...382 Plasma power supply 1 Sheet 2 of 22 013403 ...
Страница 383: ...383 Plasma power supply 2 Sheet 3 of 22 013403 ...
Страница 384: ...384 Plasma power supply 3 Sheet 4 of 22 013403 ...
Страница 385: ...385 Plasma power supply 4 Sheet 5 of 22 013403 ...
Страница 386: ...386 Plasma power supply 5 Sheet 6 of 22 013403 ...
Страница 387: ...387 Plasma power supply 6 Sheet 7 of 22 013403 ...
Страница 388: ...388 Plasma power supply 7 Sheet 8 of 22 013403 ...
Страница 389: ...389 Gas connect console 1 Sheet 9 of 22 013403 ...
Страница 390: ...390 Gas connect console 2 Sheet 10 of 22 013403 ...
Страница 391: ...391 Torch connect console Sheet 11 of 22 013403 ...
Страница 392: ...392 Coolant system Sheet 12 of 22 013403 ...
Страница 393: ...393 Gas system 1 Sheet 13 of 22 013403 ...
Страница 394: ...394 Gas system 2 Sheet 14 of 22 013403 ...
Страница 395: ...395 Gas system 3 Sheet 15 of 22 013403 ...
Страница 402: ...402 Wireless subsystem block diagram Sheet 22 of 22 013403 ...