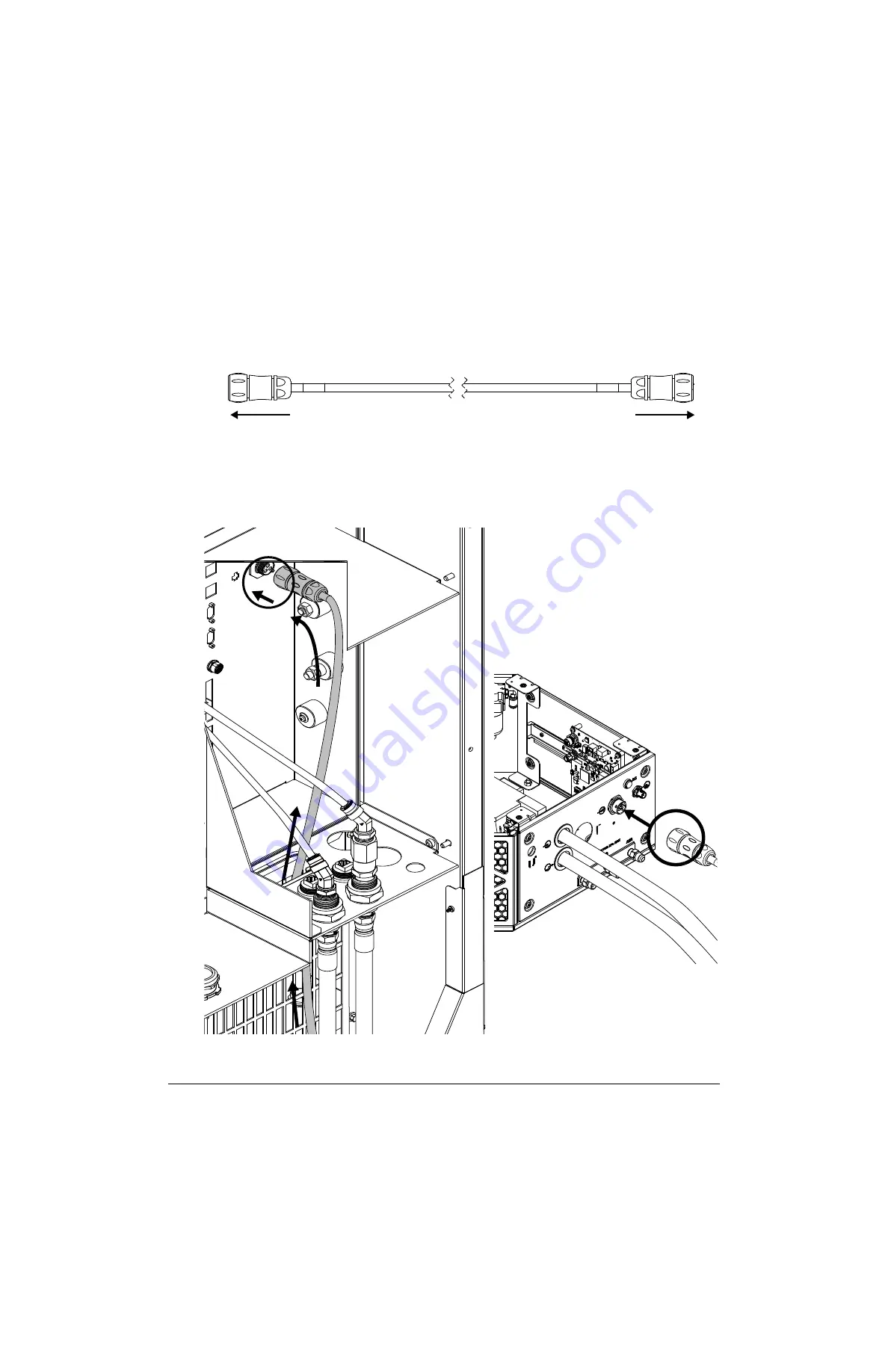
Installation
3
XPR300
Instruction Manual
809480
103
Connect the power cable
Figure 13
– Power cable
For lengths, see
on page 362 of the
.
Figure 14
– Connect the power cable
To plasma power supply (male cable connector)
To gas connect console (female cable connector)
Plasma power supply
Gas connect console
Содержание XPR300
Страница 1: ...XPR300 Plasma Instruction Manual 809480 Revision 2 English ...
Страница 18: ...Contents 18 809480 Instruction Manual XPR300 ...
Страница 34: ...Specifications 1 34 809480 Instruction Manual XPR300 ...
Страница 66: ...Qualifications and Requirements 2 66 809480 Instruction Manual XPR300 ...
Страница 188: ...Connect for Communication 4 188 809480 Instruction Manual XPR300 ...
Страница 192: ...Coolant Installation 5 192 809480 Instruction Manual XPR300 ...
Страница 230: ...Operation 6 230 809480 Instruction Manual XPR300 ...
Страница 337: ...Parts List 9 XPR300 Instruction Manual 809480 337 ...
Страница 343: ...Parts List 9 XPR300 Instruction Manual 809480 343 ...
Страница 380: ...Wiring Diagrams 10 380 809480 Instruction Manual XPR300 ...
Страница 381: ...381 Overview Sheet 1 of 22 013403 013403 ...
Страница 382: ...382 Plasma power supply 1 Sheet 2 of 22 013403 ...
Страница 383: ...383 Plasma power supply 2 Sheet 3 of 22 013403 ...
Страница 384: ...384 Plasma power supply 3 Sheet 4 of 22 013403 ...
Страница 385: ...385 Plasma power supply 4 Sheet 5 of 22 013403 ...
Страница 386: ...386 Plasma power supply 5 Sheet 6 of 22 013403 ...
Страница 387: ...387 Plasma power supply 6 Sheet 7 of 22 013403 ...
Страница 388: ...388 Plasma power supply 7 Sheet 8 of 22 013403 ...
Страница 389: ...389 Gas connect console 1 Sheet 9 of 22 013403 ...
Страница 390: ...390 Gas connect console 2 Sheet 10 of 22 013403 ...
Страница 391: ...391 Torch connect console Sheet 11 of 22 013403 ...
Страница 392: ...392 Coolant system Sheet 12 of 22 013403 ...
Страница 393: ...393 Gas system 1 Sheet 13 of 22 013403 ...
Страница 394: ...394 Gas system 2 Sheet 14 of 22 013403 ...
Страница 395: ...395 Gas system 3 Sheet 15 of 22 013403 ...
Страница 402: ...402 Wireless subsystem block diagram Sheet 22 of 22 013403 ...