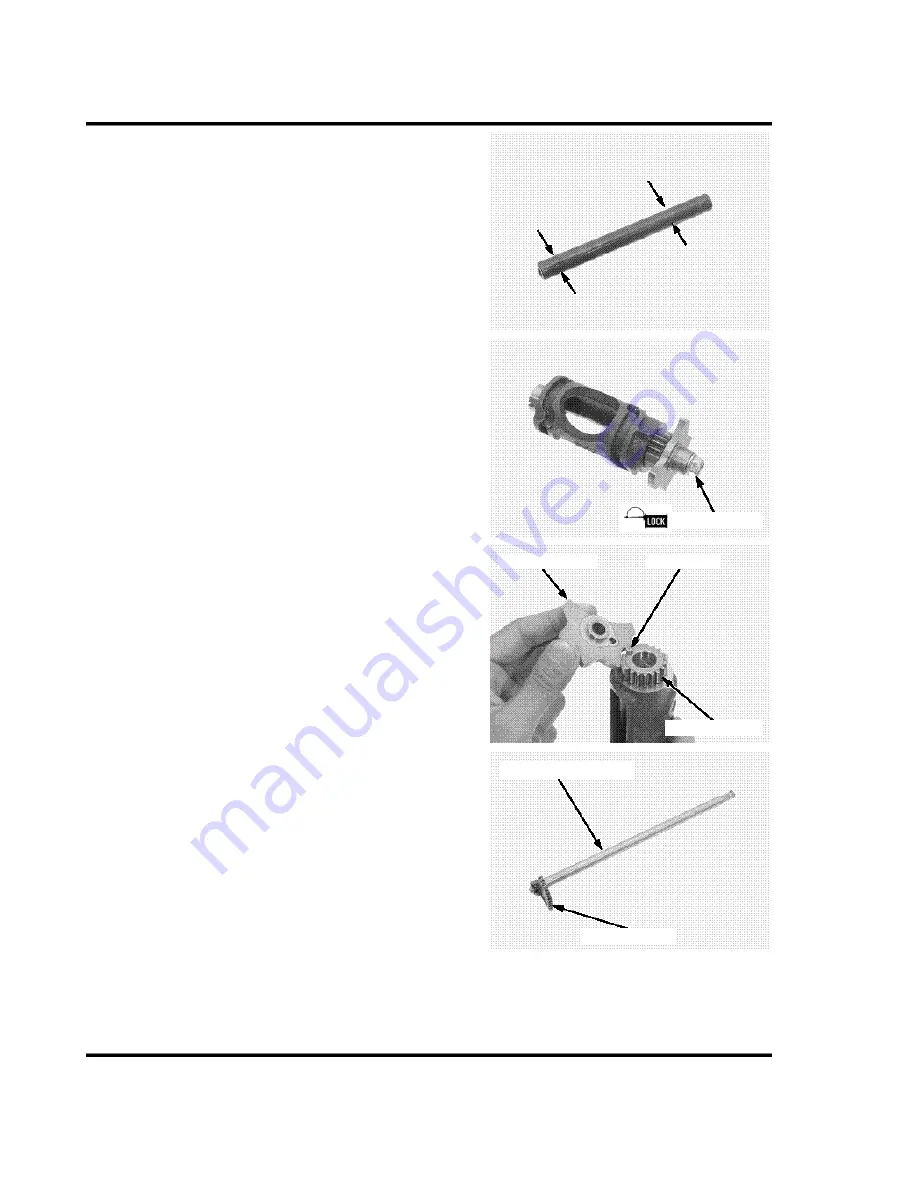
'61HN252' by American Honda Motor Co. - Page 240 of 540
http://services.honda.com/ServiceManual/SVC_MNL/61HN253/61HN2...
1 of 1
3/9/2008 10:58 PM
[2005-2008] [TRX500 FA/FGA]
SUB-TRANSMISSION/GEARSHIFT LINKAGE
Measure the shift fork shaft O.D.
SERVICE LIMIT: 10.96 mm (0.431 in)
Check the shift drum guide grooves for abnormal
wear or damage.
Check the shift drum center plate and shifter gear
for abnormal wear or damage.
Remove the bolt, center plate, shifter gear and
dowel pin if necessary.
CENTER BOLT
Install the dowel pin, drum shifter gear and center
CENTER PLATE
DOWEL PIN
plate.
Apply locking agent to the drum center bolt threads.
Install and tighten the bolt.
TORQUE: 27 N·m (2.8 kgf·m, 20 lbf·ft)
SHIFTER GEAR
Check the gearshift spindle for bending or damage.
Check the spindle shifter gear for abnormal wear or
GEARSHIFT SPINDLE
damage.
SHIFTER GEAR
12-10