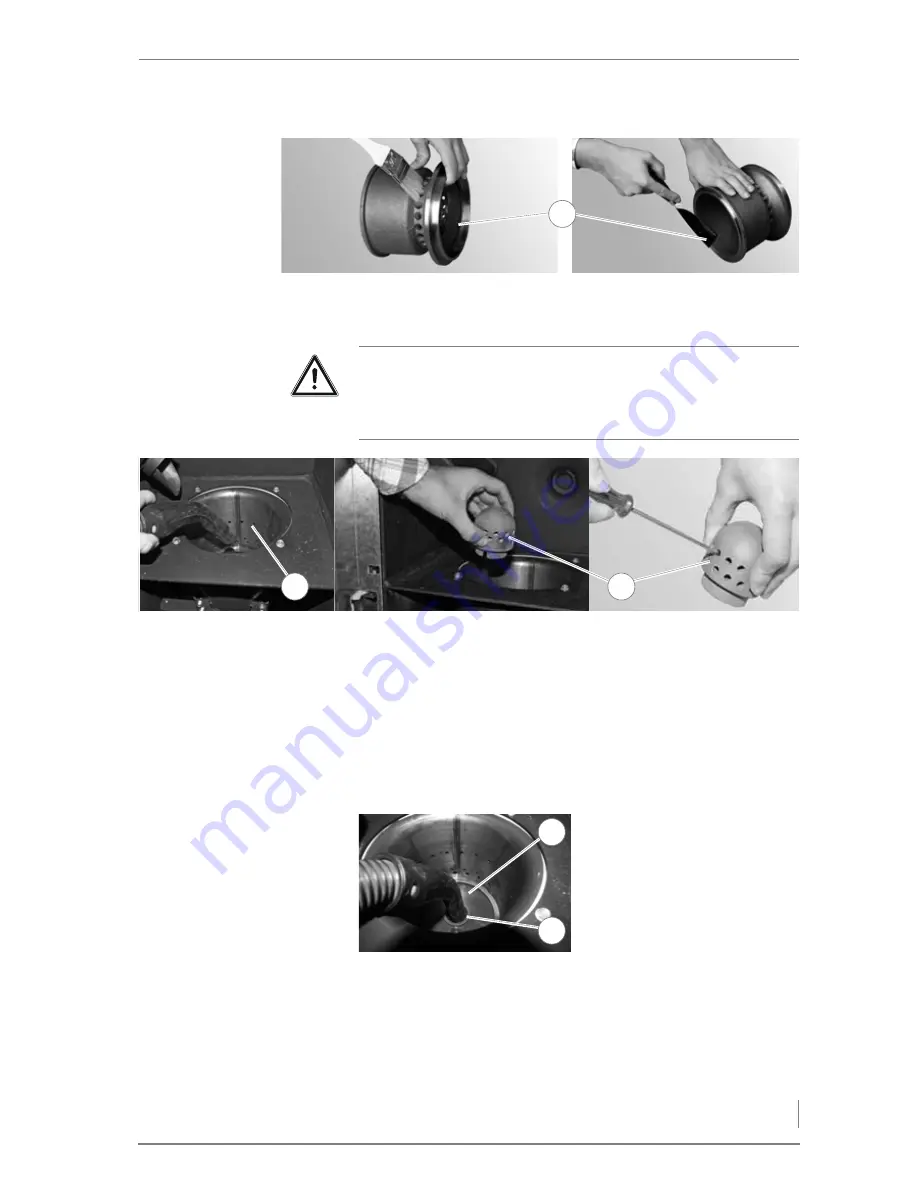
7 Cleaning and servicing the heating system – Procedure
51
9.
Clean the cone (1) on all sides using a brush and remove any hard
deposits with a scraper.
10.
Clean the burner pot (1) with a vacuum cleaner.
11.
Make sure that the secondary air openings in the burner pot (1)
are free.
12.
Take the primary air pin (2) out of the burner pot.
13.
Carefully clean the primary air pin (2) and the primary air holes
with a suitable tool (such as a screwdriver).
14.
Make sure that the primary air holes are free.
16.
Clean the remaining combustion residues in the burner pot and
the primary air pipe (1) using a vacuum cleaner.
17.
Ensure that there are no more combustion residues in the primary
air pipe since otherwise the ignition element can be damaged.
Figure 7/10 - Cleaning the cone
1
Important!
Always remove all the ash from the combustion chamber and
burner pot first. Only then can you take out the primary air pin for
cleaning.
Figure 7/11 - Cleaning the combustion chamber and primary air pin
1
2
15.
Use the cleaning tool to
remove any combustion
residue from the bottom of
the burner pot (1).
Figure 7/12 - Cleaning the primary air pipe
1
2
Содержание K10
Страница 1: ...hdg bavaria com HDG K10 15 21 26 33 Operating manual ...
Страница 2: ......
Страница 63: ......