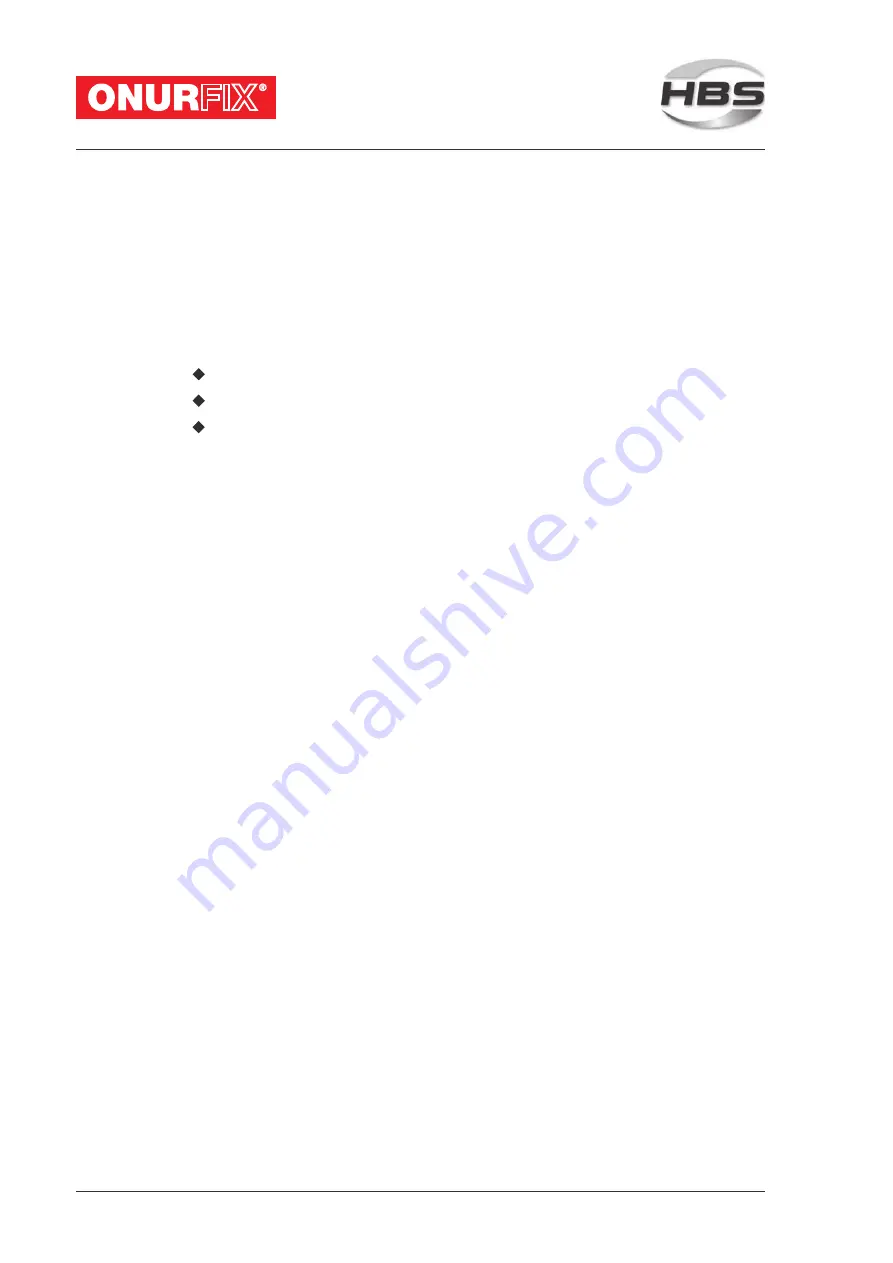
40
A 12 Order No. BA 93-20-270 Issue 01.03.08
6
Switching off the Welding Gun
This chapter describes what you should observe when you switch off the power unit
temporarily or completely.
6.1
Temporary Switching off
Switch off the power unit.
Unplug the control cable and the welding cable from the power unit.
Protect the stud welding gun against ingress of fluids and foreign bodies.
6.2
Disposal
If you shut down the installation, you can return the complete welding gun to HBS (for
address see page ii).
We will take care for environmentally correct material separation and disposal.
Содержание 93-20-270
Страница 1: ...A 12 Welding Gun 93 20 270 Operating Manual ...
Страница 45: ...A 12 Order No BA 93 20 270 Issue 01 03 08 45 Welding gun type A 12 93 20 270 ...
Страница 47: ...A 12 Order No BA 93 20 270 Issue 01 03 08 47 Shielding gas tripod complete A 12 93 40 021 ...
Страница 49: ...A 12 Order No BA 93 20 270 Issue 01 03 08 49 Ceramic tripod complete A 12 93 40 022 ...
Страница 61: ...A 12 Order No BA 93 20 270 Issue 01 03 08 61 Service Support ...
Страница 65: ......