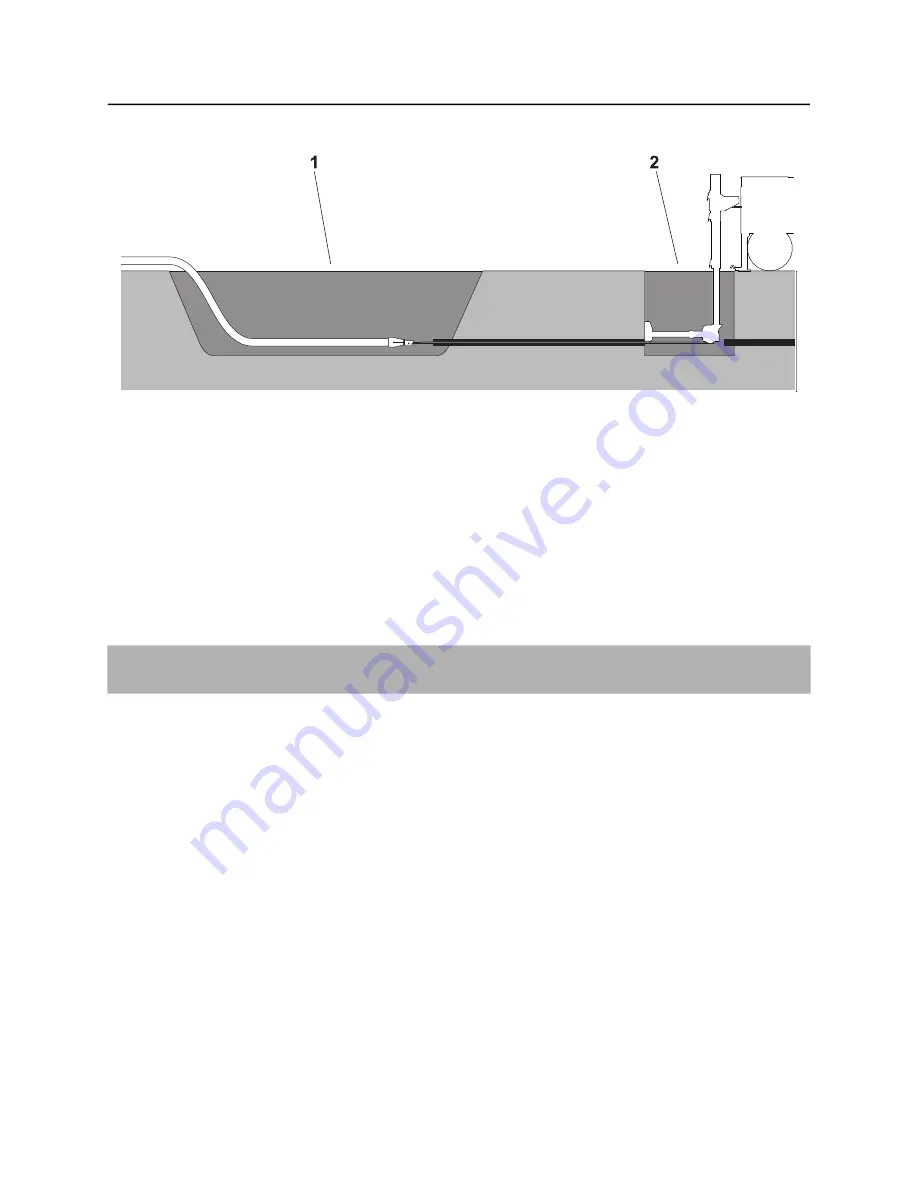
HG2200/HG2200AT Operator’s Manual
Check Supplies and Prepare Equipment
60 - Prepare
Requirements
Installation Pit (1)
•
Pit dimensions depend on pipe depth and product being installed.
•
Must be in line with existing pipe.
•
Sloped back end aids new product installation. Consider new product bend radius.
Bursting Pit (2)
•
Must accommodate the length and angle of the downhole unit.
Check Supplies and Prepare Equipment
Check Supplies
•
marking flags or paint
•
fuel
•
hydraulic oil
•
keys
•
cutting heads, clevis
•
barrier cones and tape
•
Wire cable (See “Wire Cable” on page 92.)
•
personal protective equipment, such as hard hat and safety glasses
•
notepad and pencil
NOTICE:
Follow U.S. Department of Labor regulations on excavating and trenching (Part 1926, Subpart
P) and other similar regulations.
j57om021w.eps
Содержание HG2200AT
Страница 1: ...TECHNICAL PUBLICATIONS Operator s Manual HG2200 HG2200AT Issue 2 1 960 1119 Original Instruction...
Страница 51: ...HG2200 HG2200AT Operator s Manual Battery Disconnect 50 Controls...
Страница 75: ...HG2200 HG2200AT Operator s Manual Retrieve Tracked Unit 74 Transport...
Страница 87: ...HG2200 HG2200AT Operator s Manual Finish Installation 86 Burst Pipe...
Страница 129: ...HG2200 HG2200AT Operator s Manual As Needed 128 Service...
Страница 133: ...HG2200 HG2200AT Operator s Manual Declaration of Conformity Information 132 Specifications...
Страница 136: ...HG2200 HG2200AT Operator s Manual Service Record 135 Service Record Service Performed Date Hours...
Страница 137: ...HG2200 HG2200AT Operator s Manual 136 Service Record Service Performed Date Hours...
Страница 138: ...HG2200 HG2200AT Operator s Manual Appendix 137 Appendix Chapter Contents Tire Safety Information...
Страница 146: ......